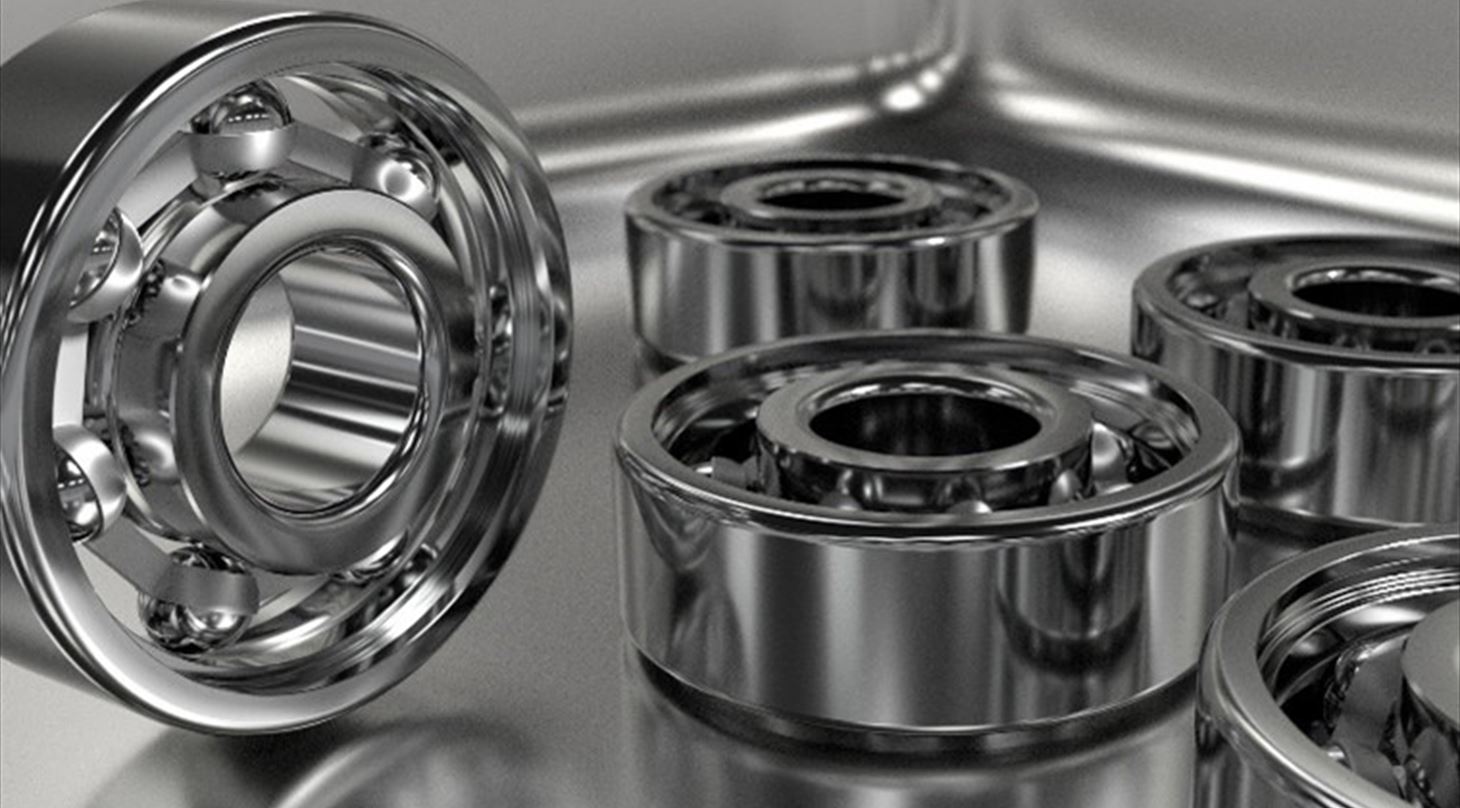
Advanced non-destructive characterization of metal components
Uncover the hidden depths of metal components by conducting non-destructive analyses at large-scale facilities.
DTI can help you gain new insight into the challenges of the metal industry, including fatigue, manufacturing and corrosion related issues by utilizing advanced characterization.
Structure and residual stresses
Diverse properties that are of importance to the performance of the metallic materials and components can be measured precisely and in the bulk of the material using x-ray or neutron radiation. The properties that we can measure include
- Mapping of grains
- Grain size
- Phase analysis
- Residual stresses
- Chemical composition
- Magnetic properties
Distinctive features
Due to the nature of the radiation from large-scale facilities, we are able to conduct very fast measurements with high resolution in the bulk of the material. This gives unique opportunities to see structural details within metals or monitor processes in realistic fabrication or in-situ conditions, for example
- Processes like laser powder bed fusion (LPBF) additive manufacturing of steel can be captured with high temporal resolution in each laser pulse.
- 3D visualization of the internal structure of components, such as cracks and pores. Crack propagation can also be visualized during in-situ experiments.
- Deep information depths and sensitivity to hydrogen differentiates us from conventional analysis methods.
Relevance of non-destructive techniques
As we specialize in non-destructive methods, these techniques are crucial for evaluating important factors for the long-term durability of critical components, for example in the aerospace industry and for the reuse of critical components.
Impact on material properties
An example would be residual stresses in metal components, which can drastically affect fatigue strength and may cause deformation after machining, leading to issues keeping within dimensional tolerances. Stress corrosion cracking is a critical phenomenon often caused by unresolved residual stresses and is challenging to detect before a catastrophic failure occurs.
Huge potential
These analysis methods offer great flexibility and potential for exacting unseen details in any kind of material, from stainless steel to aluminum and titanium alloys. Each solution is customer specific, so do not hesitate to contact us for more information.