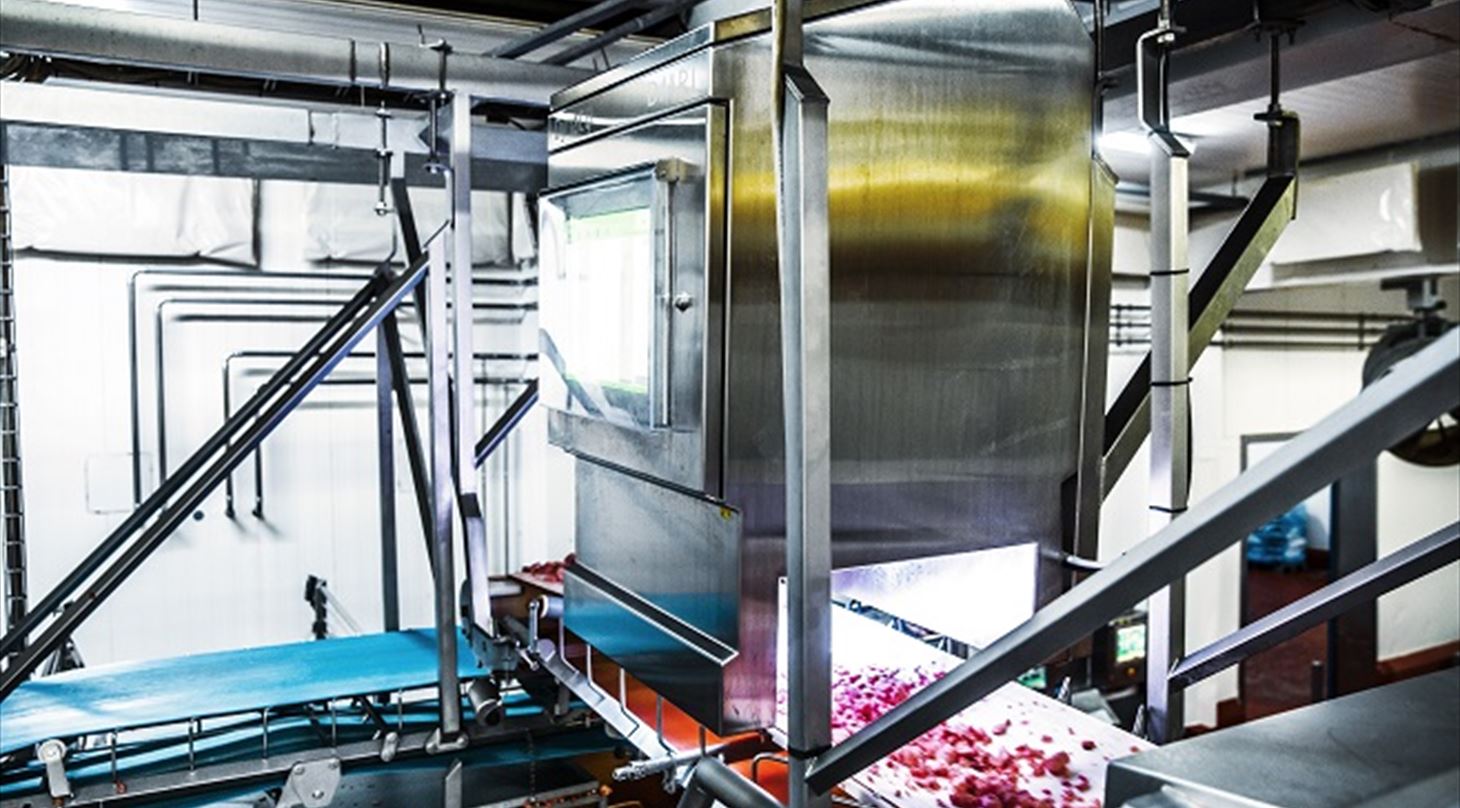
Vision-recognition detects plastic in food products with high sensitivity at high speed
The food industry is keenly focused on preventing contaminants from reaching the consumer. Contaminants are defined as metal fragments, bone fragments and hard or soft shreds of plastic that have inadvertently ended up in produce, ingredients or products. If these go undetected in products leaving the factory, this can give rise to complaints, product recalls and perhaps even liability suits, all of which can be very harmful to a manufacturer’s reputation. Metal fragments can be detected in products using a metal detector or an X-ray device. Bone fragments embedded in meat can only be found using an X-ray detector.
Automatically detecting small shreds of plastic in foods is a far more difficult task. Plastic cannot be detected in food using an X-ray device, as the fragments are often tiny, thin fragments of plastic film used to package the products before they are processed, or small fragments of aprons or gloves. Small, hard plastic fragments from belts, boxes and vessels are also a problem. As mentioned, these items are usually quite tiny, i.e. below the detection limit for an X-ray device, and plastic’s ability to stop X-ray radiation is almost the same as the product surrounding it. Needless to say, plastic cannot be detected by a metal detector as it is usually neither electrically conductive nor magnetic. A powder can be added to certain types of plastic to make it detectable by a metal detector, but in practice this procedure only works if large pieces of plastic are involved. Practical experience shows that these are usually tiny contaminations containing insufficient metal to be detectable by a metal detector.
Up to now, the food industry’s only safeguard against plastic contamination has been to deploy staff on the production line to inspect products to find plastic fragments and remove these from the product by hand. This cost-intensive process is ultimately ineffective as well, as visual inspection is an exhausting, difficult task for line workers, particularly at high line speeds.
DynaCQ – plastic detector
Vision-based equipment – named DynaCQ (Dynamic Check of Quality) – has been developed at the Danish Technological Institute. The equipment automatically detects fragments of plastic in foods during the production process. The equipment has been installed at a number of production sites, replacing monotonous, tiring manual labour. The equipment is capable of inspecting the surface of foods moving on a conveyor belt at speeds of up to 70 metres/minute. On a 70-cm-wide conveyor belt, the equipment can find plastic items as small as 2 x 2 mm, and often smaller. When the equipment detects a contaminant, it sends a signal to the conveyor belt’s control system indicating that something has been found. This enables the individual contaminated product to either be removed from the belt manually after stopping the belt or to be removed automatically.
The vision equipment comes in two versions: a single-camera solution which is used if products can be spread out in a thin layer across the conveyor belt; and a dual camera solution, which inspects the upper and lower sides of the products.
DynaCQ has been used for the entry and exit inspection of produce and products such as sausages, protein powder and minced meat products. The equipment has also been successfully tested on bacon cubes, sweets and pizzas, where plastic contaminants can also cause problems.
As the equipment is colour-calibrated according to familiar colour standards, it can also be used to quality-sort produce used in the production process or in the exit inspection of finished products. In addition, DynaCQ can inspect ready-made pizzas to see if toppings are evenly distributed across the entire pizza surface.
For the meat industry, DynaCQ has also been developed to include programs for automatic product identification. The equipment has been “trained” to recognise different cuts of meat in boxes of meat from a cutting line or different individual cuts directly after the cutting belt. In these cases, the vision-based equipment can reduce the number of employees needed to verify box contents by hand – thereby increasing the line capacity, reducing the error rate and ensuring that products reach the right destination.
DynaCQ is designed to be a flexible, robust and hygienic measurement platform. It is also expected that it can be customised for many other food-quality inspection processes, e.g. in the fish industry, for by-products, etc.