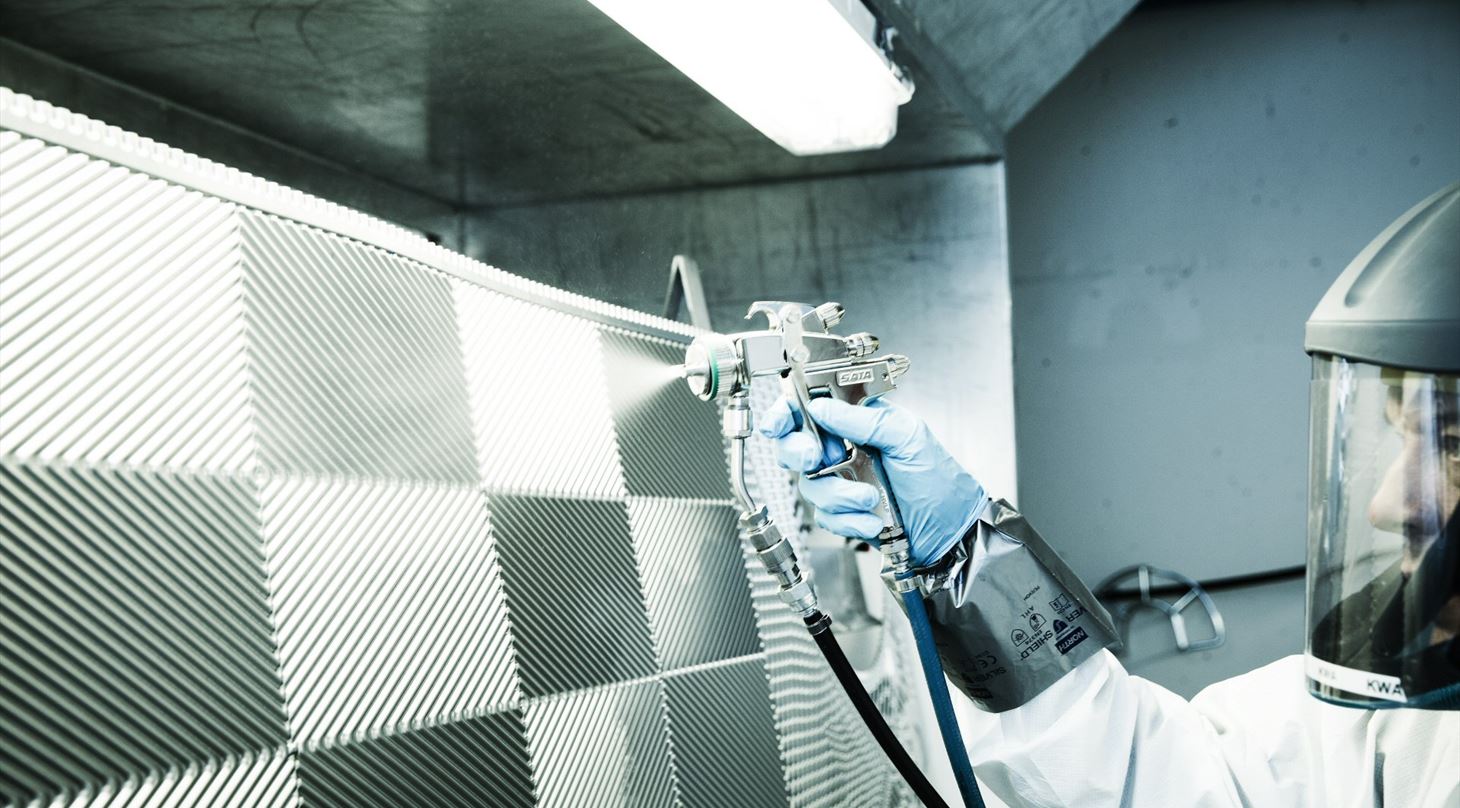
Coating of Plate Heat Exchangers Boosts Maintenance Processes
Danish Technological Institute has developed a coating which, at Alfa Laval, has been used on plate heat exchangers for the tempering of crude oil. This coating ensures extended operating time for the heat plate exchangers, minimizes energy consumption, ensures increased operating time, and reduces the environmental impact.
Crude oil extraction is a complicated process which calls for a tempering process, among others, to ensure the correct viscosity and to minimize the risk of evaporation of explosive gasses. In the plate heat exchangers used for such tempering a challenging factor is the large amount of material deposition. Such deposition reduces the efficiency of the exchangers, causes interruption of production, and calls for large-scale and expensive maintenance.
Before maintenance to the heat exchanger can be carried out, it needs to be taken apart at the offshore location itself; a process that requires a lot of personnel and which has an environmental impact due to the risk of oil leaks during such process. When the plate heat exchanger has been taken apart, it will be placed in a container and by a service vessel carried to the shore where a lorry will transport it to a service centre. At this centre, the plate heat exchanger will undergo a mechanical clean-up and a purging process before being returned to the platform.
Danish Technological Institute has developed a thin glass-ceramic-like coating, CORE Coat 010, which effectively prevents material deposition on the surface of plate heat exchangers thereby ensuring an extension of their operating time, minimizing the need for maintenance, and a reduced environmental impact as a result.
Coating – Plate Heat Exchangers
At Alfa Laval, a global producer of pumps, valves, and heat exchangers, the unique coating developed by Danish Technological Institute has been used in several company products which has resulted in increased optimization.
- We have several commercial installations with plate heat exchangers coated with CORE Coat 010, and we have received the best possible feedback indicating that they are all performing very well. Among our clients we have seen examples where the time between service checks has been extended from six months up to three years – a result that can be transferred directly to the bottom line, says Mats Nilsson, R&D manager at Alfa Laval.
At present, a laboratory has been set up at Danish Technological Institute, Aarhus, Denmark, for the purpose of producing the actual coating and the application for Alfa Laval’s plate heat exchangers. Should this coating result in increased demands from Alfa Laval’s clients, the company will consider investing in similar equipment.
Mats Nilsson explains that this coating makes it possible for Alfa Laval to supply a product of higher quality than their competitors which is an important asset to their business.
- We have greatly appreciated the competences added to our production by Danish Technological Institute as we have not ourselves at present been able to develop the relevant coating technique.