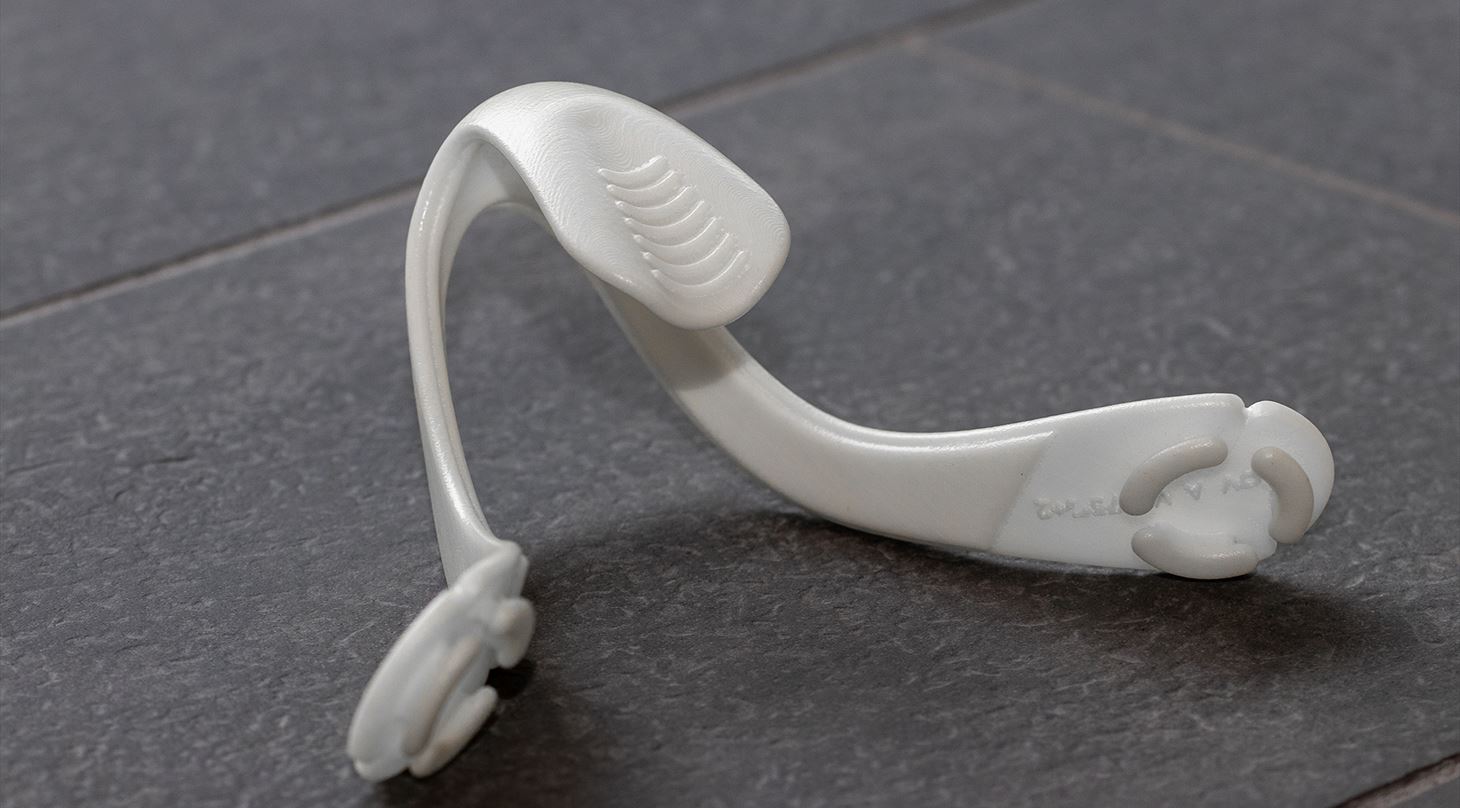
Hegenberger Speculum accelerates development with Additive Manufacturing
Nurseries still use a tool from 1845 when women are being sewn after giving birth. Midwife Malene Hegenberger decided to change that, and by using Additive Manufacturing at the Danish Technological Institute, she succeeded in accelerating the development of her new invention - Hegenberger Speculum.
Malene Hegenberger's idea for the Hegenberger Speculum had been around for many years. It appeared when she discovered that despite 18 years of experience as a midwife, it was not getting easier to sew women who were fractured after giving birth. The Hegenberger Speculum works by placing it in the woman's vagina after birth, thereby expanding the midwife's vision, which allows her to sew the woman properly and without the help of an assistant who is often needed today.
In 2015, it was time to realize the idea, and as is often seen with inventors, Malene Hegenberger started at home at the kitchen table with paper, scissors and glue. Along the way, she received professional sparring from midwives and doctors at Aarhus University Hospital, and in 2017 she joined a course under the inventor’s advisory at the Danish Technological Institute in Taastrup. Here, she could discuss her thoughts and ideas in a confidential forum and at the same time use the counseling workshops. Let us help you with AM production
Additive manufacturing accelerated development
During the course with the inventor’s advisory, Malene Hegenberger came into contact with Industrial 3D printing at the Danish Technological Institute in Aarhus, and from there the development took off. The Additive manufacturing experts helped Malene seek financial support from the InnoBooster program under the Ministry of Innovation, and with this support it was possible to further develop the prototype using Additive Manufacturing - something that Malene Hegenberger was very excited about:
- You can make your drawing first, and then you can see the 3D print on the screen while doing it, and then you can have it in physical form within a few hours. That has a major impact on the development process - that the vision you have had in your head can be physically in your hand within a very short time, says Malene Hegenberger.
In the video below, you can hear more about the development process - the case continues after the video (video is in Danish).
Additive Manufacturing is very suitable for this type of development, where it is necessary to quickly test the prototype along the way, and where a number of adjustments must be made based on the feedback from the various tests. Along the way, the Additive manufacturing experts at the Danish Technological Institute have provided professional sparring about the development and the opportunities, and Malene Hegenberger was excited about the collaboration. In addition to the professionalism, she emphasizes that there was a good common understanding - not only for the product, but also for the development phase itself.
- I have only good things to say about the Danish Technological Institute. The collaboration is innovative in itself, and there is a lot of positive synergy in the fact that us professionals who know what we need team up with an Additive Manufacturing engineer. The fact that the two professionals work together on something result in some really good products, says Malene Hegenberger.
35 versions in two monthsDuring the course of the development, Malene Hegenberger was able to visit the Danish Technological Institute on Friday when she had changes to the speculum. Together with the Additive Manufacturing specialists, she made changes to the drawings, and then the new versions were printed and finished over the weekend. On Monday, Malene could pick up the new items and test them in practice, and on Tuesday she could come back with feedback and changes based on the results of the test - for example, it could be size or angles that needed to be changed. There can be a lot of things that need to be changed during a development process, but with Additive Manufacturing, the changes can be made right away so that the development cadence does not slow down.
- During the development process, we managed 35 different editions in two months. So Additive Manufacturing helped speed up the process at very low costs compared to casting or milling out the item, where major changes would have to be made to molds or programming. Here, we could create several items in a very short time at a very low price, says Mads Østergaard, section manager in Industrial 3D printing at the Danish Technological Institute.
See how we can help you with AM production
After arriving at the right prototype, Malene Hegenberger made a number of tests and some further adjustments, and during the development and testing process she has received a lot of positive feedback – for instance when she exhibited Hegenberger Speculum at a Nordic conference for obstetricians and gynecologists in Odense last year and experienced great enthusiasm from the professionals. Since then, Malene Hegenberger has received a big investment from CAPNOVA to put the prototype into production, and Hegenberger Speculum is expected to be launched on the Nordic market during 2019.