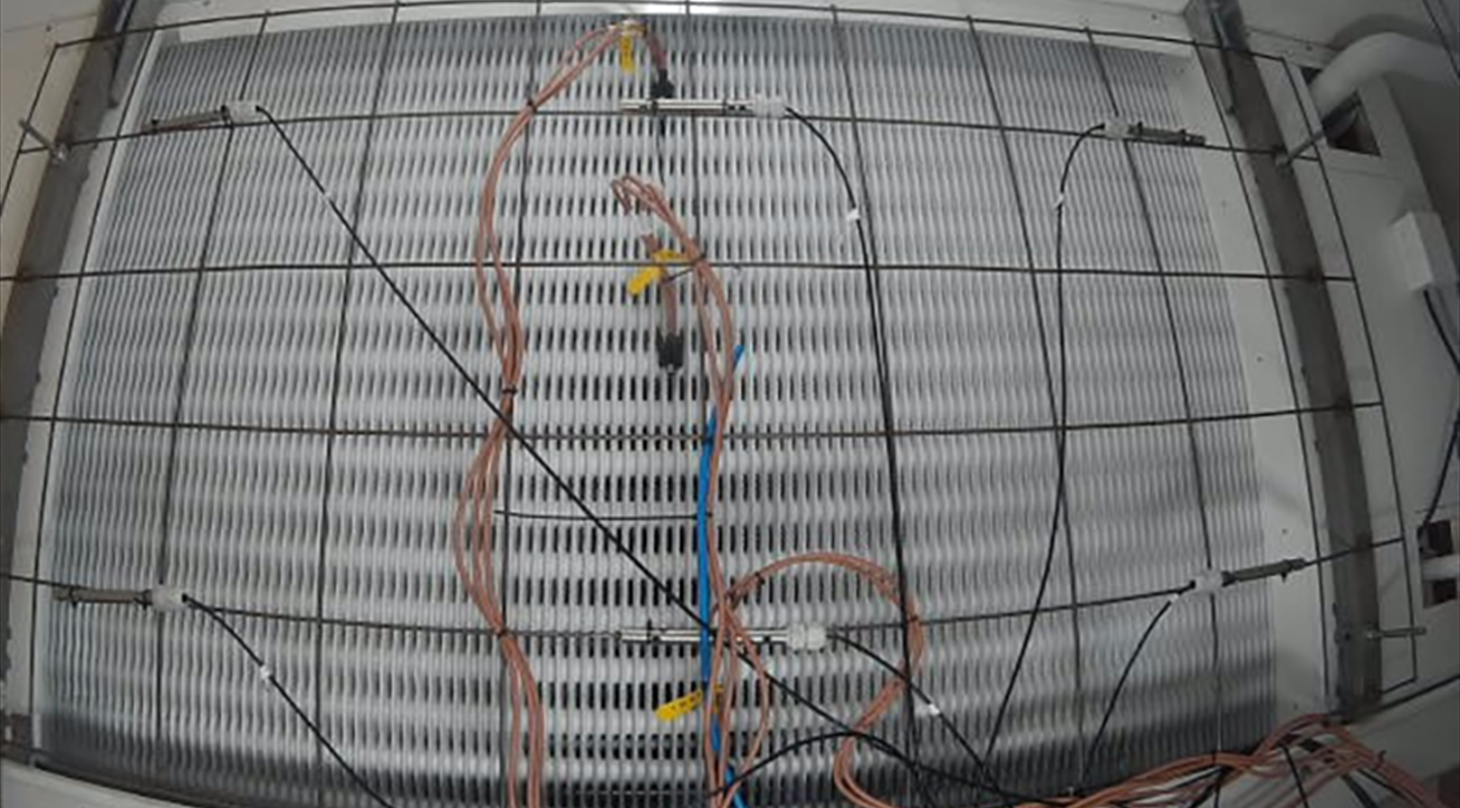
Future Ammonia Refrigeration Systems
Project start October 2017. The project is completed.
Purpose of project
The overall purpose of the project is to develop industrial ammonia evaporator systems with improved energy efficiency, so that they can compete with other less efficient alternative solutions. This will ensure the market position of the energy efficient ammonia as refrigerant for industrial refrigeration systems of the future.
Objectives
Ammonia (NH3) has excellent thermodynamic properties and is used worldwide in most industrial refrigerating and freezing installations. Danish industry is a world leader in this field – not only in the form of the refrigeration industry, but also through the large machinery industry producing and delivering to the food industry, where refrigeration equipment plays a key role.
Powered by new rules - in particular in the USA, a trend towards the use of significantly less refrigerant charges has started, and the overall objective of the project is to ensure that Danish industry will be able to offer new solutions to this new global trend with the highest overall energy efficiency.
The objective is also to develop new system solutions that reduce the energy consumption in industrial refrigeration and freezing equipment significantly. The systems can be used in connection with both existing and new industrial evaporators for ammonia which through active control will minimize the considerable extra energy losses that exist in the system designs used today (so-called pump circulated systems).
The new solutions and control systems will be based on detailed research and simulations of evaporator characteristics under varying operating conditions which occur in industrial systems. The project will demonstrate the future evaporator design in a laboratory followed by demonstrations in real-life industrial plants.
At the end of the project, the partners will have fully developed products in the form of control systems, separation systems, and valve systems for state-of-the-art evaporators and full scale proof-of-concept for future high-efficiency evaporator technologies with very low refrigerant charges in order to continue with further marketing of the concepts.
The project is conservatively expected to lead to 15 GWh in annual electricity savings in Denmark alone, and since industrial refrigeration is used in almost every food production company in the world, the potential is expected to be even higher. In addition, there will be a corresponding growth in companies that can use the developed technologies in their products.
Activities
The project is divided into five phases:
- Knowledge gathering. In order to create a full overview of the current stage of the research within the technical areas, the project will gather relevant knowledge about CCR evaporators (Controlled Circulation Rate), DR evaporators (Dry Return), microchannel evaporators, and the challenges regarding above, e.g. water, oil, defrost, air, etc.
- Research and development of new evaporator systems. In this phase, the research and development of the new solutions will take place. This includes the designing of the CCR/DR solutions and the microchannel evaporator.
- Verification of solutions at DTI. The developed solutions are verified by measurements carried out at DTI. This includes test setup at DTI, collection of data, verification of the CCR and DR systems, validation of the research from DTU, verification of the microchannel evaporator solution, and validation of the microchannel research from DTU.
- Verification of solutions at the industrial plants. In this phase, the CCR and DR solutions will be implemented in industrial systems. The project will collect data and verify the CCR and DR systems as well as validate the research from DTU.
- Dissemination of knowledge. The results of the project are disseminated through articles published in relevant magazines, participation in conferences, information on websites, and through the final project report.
Participants
- Danish Technological Institute (DTI) – Jóhannes Kristófferson (project manager)
- Danfoss
- Aluventa
- Scanico
- Claus Sørensen
- Technical University of Denmark (DTU)
- Innoterm
Funding
The project is funded by EUPD.