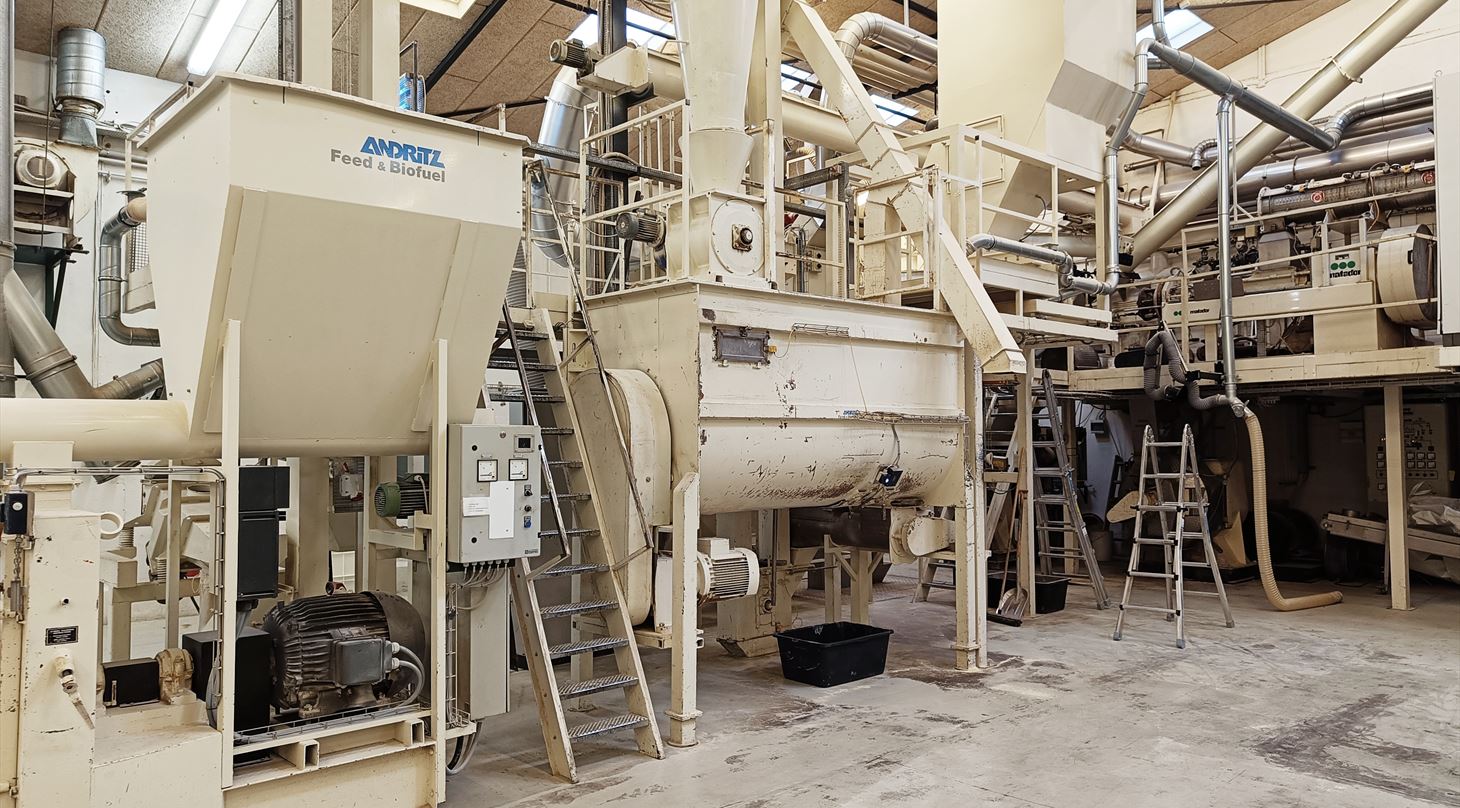
Pelleting of animal feed - energy experiments
At Danish Technical Institute, we have the capability to conduct energy experiments on our pilot plant to identify energy-saving opportunities in pelleted animal feed. This is exactly what we assisted dsm-firmenich with when they aimed to reduce expenses for their customers during the crisis.
In animal feed production, the energy consumption of the pellet press can account for more than half of the total electrical consumption in the production. By knowing the exact energy consumption of the pellet press, resources can be better managed, production capacity can be planned, and processes can be optimized to reduce costs - and most importantly, minimize the overall environmental impact.
– At dsm-firmenich, we were interested in exploring if our customers could achieve energy savings during the crisis. We wanted to investigate if lowering the inlet temperature would result in overall energy savings and if the lower temperature would lead to increased electricity consumption in the pelleting process, says Arne Korsbak from dsm-firmenich. He further adds, “Additionally, I was interested in assessing if we would achieve higher efficacy of our carbohydrase enzymes at the lower temperature."
Identification of energy-saving opportunities
Factors that can reduce electrical consumption in the pelleting process include specific ingredients added to the mixture before pelleting, temperature, recipe formulation, conditioning time, and die design.
At Danish Technical Institute, we have the capability to conduct tests in our pilot production while measuring energy consumption separately for steam and pellet press. This allows us to identify any correlations between electricity consumption, pellet quality, raw materials, and binding properties, thus finding the most energy-efficient production methods.
Measurement of energy consumption
The experiment was designed with two temperatures, two retention times, and two dies, and it was conducted on a production line where we could control the entire process from mixers to pellet press, thereby controlling temperatures, capacity, pellet size, steam, and pellet quality.
– We conducted 8 tests with dsm-firmenich's products to evaluate how they affected energy consumption during pelleting under different factors. In each test, we measured the amount of energy used by the pellet press and from steam, allowing us to calculate the specific energy consumption per ton of feed, says Troels Veng Samuelsen, section leader at Danish Technical Institute.
Knowledge for the future
When conducting energy experiments, we measure the specific energy consumption per ton of feed for steam and the pellet press. This is done to calculate the total energy costs if process parameters are adjusted at specific stages, enabling informed decision-making regarding potential changes.
In this experiment, we measured, among other things, whether an increase in temperature during conditioning would reduce the energy consumption of the pellet press enough to lower the overall energy cost of production. However, it was found that the costs associated with increasing the conditioning temperature outweighed the reduction in pellet press consumption.
Overall, significant improvements in energy consumption in production could not be achieved. However, the experiment has provided knowledge and calculations that can be used to adjust process parameters based on current energy prices.
– At dsm-firmenich, we will utilize the results from the experiment for future purposes. We can see that feed mills are also considering the benefits of extended conditioning, says Arne Korsbak.
Are you interested in having your pellet production's energy costs measured and obtaining knowledge about possible adjustments? Contact our pelletizing team at pelleting@dti.dk