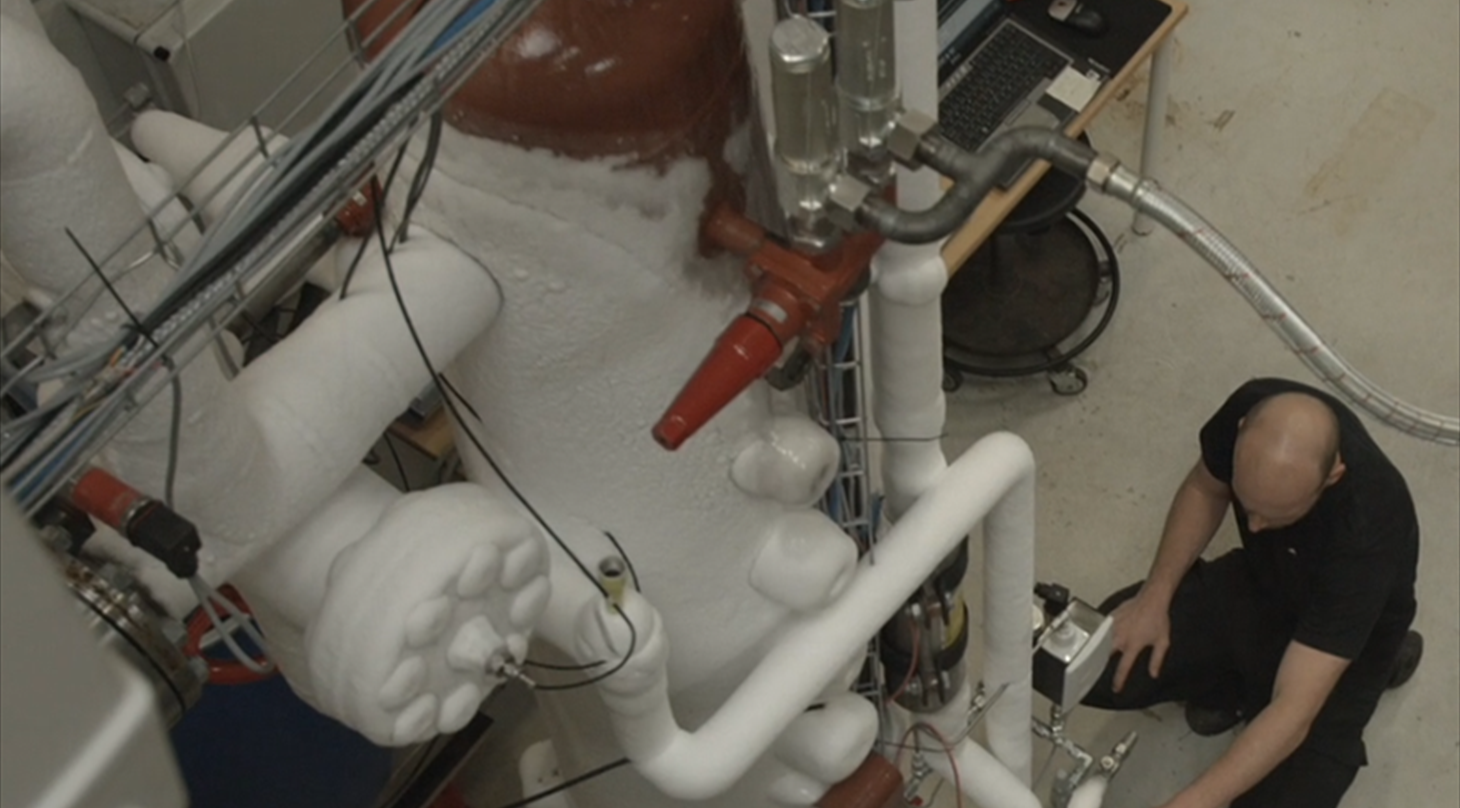
Reduce the fillings in industrial ammonia refrigeration systems – and increase efficiency!
Securing the future of the most efficient refrigerant for the industrial market.
Ammonia has excellent thermodynamic properties and is utilized in the clear majority of industrial refrigeration installations across the world. The current industrial ammonia refrigeration systems include a great amount of the natural refrigerant and can potentially become far more energy efficient. Danish Technological Institute are currently leading a project, where the goal is to develop industrial ammonia refrigeration systems with increased energy efficiency and lower fillings. Systems that can withstand the competition from other, less efficient, solutions.
Ammonia (NH3) is utilized as a refrigerant in the greater part of all industrial refrigeration- and freezing systems in the world – and Denmark presents world leaders on the market. Not only directly via the refrigeration industry, but also through the large industries that deliver machines to the food industry where installation of refrigeration technologies play a central role.
In a new project, Danish Technological Institute is working on developing new system solutions, that will reduce the energy consumption in industrial ammonia refrigeration systems. At the same time the solutions must meet a new global trend that revolves around increasing the system’s security by reducing the fillings in the systems dramatically. The development work will ensure, that the future of the Danish industry will supply ammonia refrigeration systems that are not only safe, but also include the highest total energy efficiency.
The traditional systems
Traditionally industrial ammonia systems are flooded – meaning that there is excess circulation through the evaporator – as it gives a more efficient performance of the evaporator itself. This causes a pressure loss from the evaporator to the compressor, as liquid needs to be drawn back when the cooling agents return from the evaporator, which then results in extra consumption of energy.
In systems where other refrigerants than ammonia are used, direct expansion (DX) is often the method of use. This technology usually entails value loss because of the demands regarding overheating – which is followed by extra energy consumption. On the other hand, the technology enables both simpler and cheaper system installations. The extremely high latent heat and low mass flow that characterizes ammonia as a refrigerant it can be hard to control. Therefore, the DX-technology has never managed to become popular in industrial ammonia refrigeration systems. Water and oil, which are always a part of industrial refrigeration systems with ammonia, also serve as extra challenges when the DX-technology is used for the evaporators. Especially water can lead to problems – even in small quantities.
Designing new solutions
In contrary to the traditional systems the new systems should include components, that can control the traditional systems and lead them to a lower energy consumption and decreased fillings. The pressure loss is minimized by developing a continuous active governance and control. This can secure operation via minimal circulation through the evaporator and a reduction or elimination of the need for returning the fluid. This active governance will minimize the energy loss found in the system solutions found today.
In order to meet the goals two methods need to be developed. The first is CCR (Controlled Circulation Rate). This method sets the circulation of the evaporator to the lowest possible setting, testing it under different load rates. In this way energy is saved due to the reduced pressure loss in the return pipes, and at the same time the filling is minimized because of a reduced circulation in the pipe systems. This method is actually already being developed to existing evaporators.
The second method is called DR (Dry Return) and entails the development of equipment that can ensure that the gas leaving the evaporator is dry, but never overheated. If this is executed, it will be possible to decrease the cost of the systems while making the control easier – and increasing efficiency in comparison to existing solutions.
To further increase efficiency and decrease the fillings on the evaporators, microchannel profiles are to be examined. The challenges that should be considered here include the development of white frost on the evaporators, as well as the defrosting afterwards. Furthermore, the influence that oil and water have on the evaporator will be studied.
Significant reduction of energy consumption
Jóhannes Kristófersson, senior project leader in Refrigeration and Heat Pump Technology has high expectations for the new solutions:
“A conservative expectation to the new solutions is an energy reduction – alone it Denmark it is expected to be reduced by 15 GWh per year. Given the industrial refrigeration is used in almost all food production companies in the world, we expect that the potential is even greater if we succeed in spreading this technology globally. Added to this, we expect a corresponding growth in the companies that can utilize these technologies in their products”.
If you want to learn more about the project, please contact Jóhannes Kristófersson on +45 72 20 32 54 or via jkri@teknologisk.dk.
About the project
The project, which will be running across the next three years, is a collaboration between Danish Technological Institute, Danfoss, DTU, Innoterm, Aluventa, Scanico and Claus Sørensen.
The project is funded by EUDP.