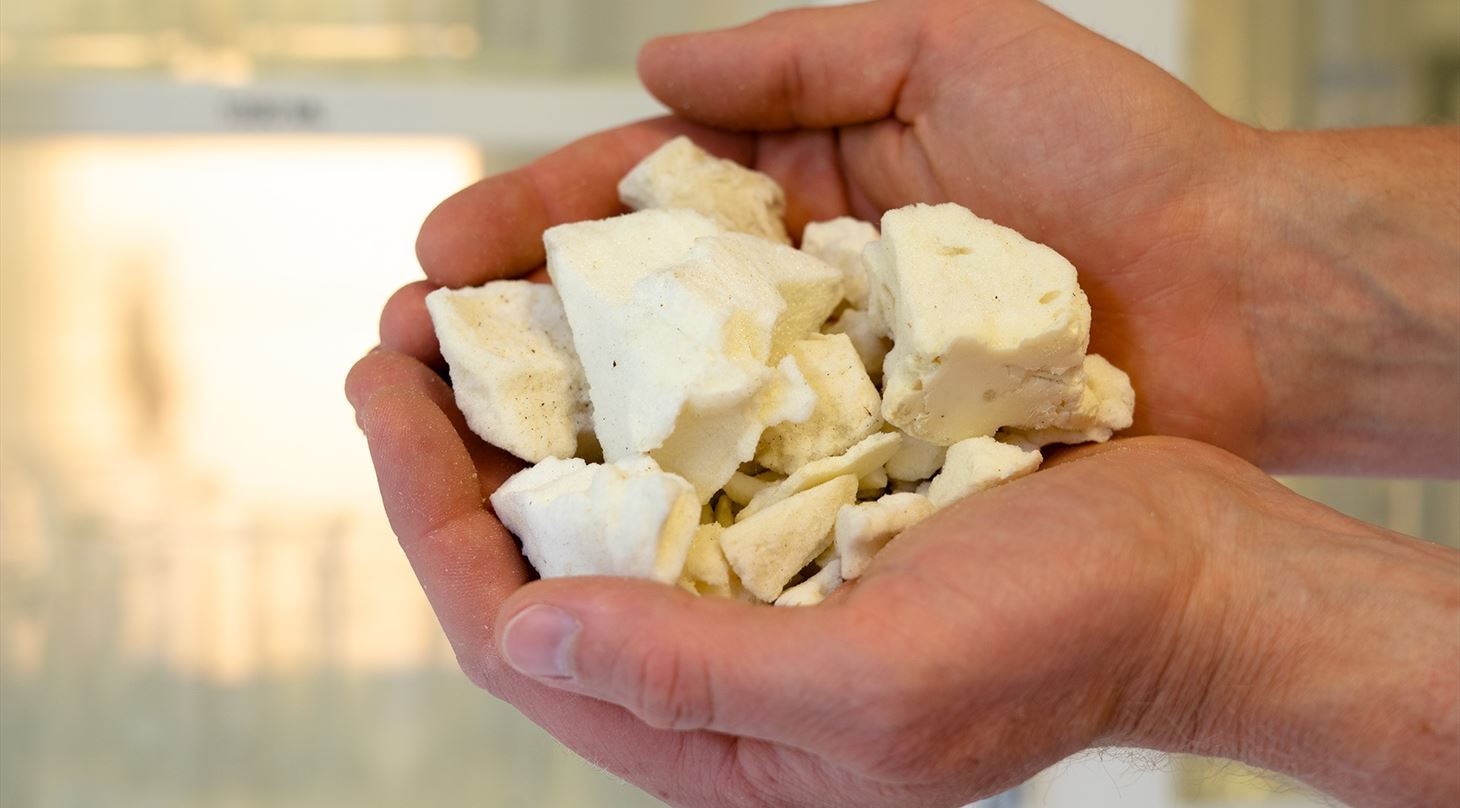
Danish consortium develops new technology for deconstruction of polyurethane based plastics
Danish researchers have developed a chemical recycling method for polyurethane targeted at handling end-of-life products. This new technology is considered a first important step towards a circular plastic economy for polyurethane that until now is governed by recycling methods leading to downgraded materials.
The novel method breaks down polyurethane into chemical building blocks that serve at feed-stock for new polyurethane products. Importantly, the chemical recycling process is robust and will, for the first time, be able to convert a wide variety of different polyurethane materials.
Irreplaceable and hard to recycle
Polyurethanes (PUR) can be found in everyday objects like refrigerators, mattresses, and shoes, but also in more sophisticated materials like wind turbine blades and aircrafts. Polyurethane currently accounts for at least 5 percent of the global plastic production. The demand is expected to grow in the decade to come.
– Polyurethane is a versatile and irreplaceable type of plastic used in countless industries. However, its chemical structure makes polyurethane hard to recycle. As a result, end-of-life products end up in landfills or is sent for energy recovery through incineration. The promising results in this project are a first step towards recycling these materials, says Anders Lindhardt (PhD), Senior Specialist at the Danish Technological Institute.
Waste is turned into new building blocks
In their most recent study, researchers show for the first time that through chemical recycling, it is possible to deconstruct commercial and end-of-life PUR materials into its monomeric building blocks.
– In practice, a range of different polyurethane materials, including examples of insulation foams, pillows, mattresses, and shoe soles have been deconstructed back into two chemical fractions. These fractions can be used for construction of new virgin PUR materials by using a catalyst in the combination with a green solvent and dihydrogen, says Anders Lindhardt, who will present the results of RePURpose at the POLYMER21 conference on 3 November.
The results were recently published in the highly esteemed Journal of the American Chemical Society – Au, an open access journal.
– This result is ground-breaking because for a plastic like PUR, the chemical structure makes recycling very difficult. As PUR cannot be remoulded, waste PUR is often mechanically recycled and used as fillers in other materials or by application in rebound polyurethane products. This all results in a secondary PUR material where the performance characteristics are deteriorated when compared to the original material, says Dr. Steffan Kristensen from Aarhus University.
Growing demand for polyurethane
As PUR recycling technologies are underdeveloped, most end-of-life and postconsumer products are landfilled or incinerated. Global annual production of PUR is estimated to be above 16 million tons, a number set to increase in the years to come.
Therefore, with a focus on circular economy, RePURpose is working towards developing technologies that move both production spill and end-of-life products towards a circular economy where polyurethane is recycled at its highest possible value.
Towards a circular economy for polyurethane
RePURpose started in 2019 with the purpose of making polyurethane recyclable. Only a few plastics like high density polyethylene, polypropylene, polystyrene, and polyethylene terephthalate are recycled. These plastics belong to a class of plastic, called thermoplastics, where the molecular structure of the material makes it possible to perform mechanical recycling, like remoulding.
The presented technology is still in its early face, but it demonstrates that a potential circular plastic economy is possible for PUR, where recycling of PUR does not give a secondary PUR-material or where PUR-waste ends up being landfilled or send for energy recovery. Future work within the
RePURpose consortium will focus on upscaling the process to ensure a cost-efficient methodology.
The RePURpose project (2019-2021) is partly funded by Innovation Fund Denmark. The consortium consists of partners from the Danish Technological Institute, Ecco Sko, Dan-Foam, Logstor, Tinby, Plixxent, H. J. Hansen and Aarhus University. Innovation Fund Denmark has invested 1.5 mio.
EUR in the project that has a total budget of 2.5 mio. EUR.
To read more, please find the open-access article here (no subscription needed):
For further information
Anders T. Lindhardt, Senior Specialist, PhD, Danish Technological Institute
Phone: +45 72 20 11 43
Mail: andl@dti.dk
Steffan K. Kristensen, Assistant Professor, PhD, Aarhus University
Phone: +45 28 15 41 00
Mail: skk@inano.au.dk