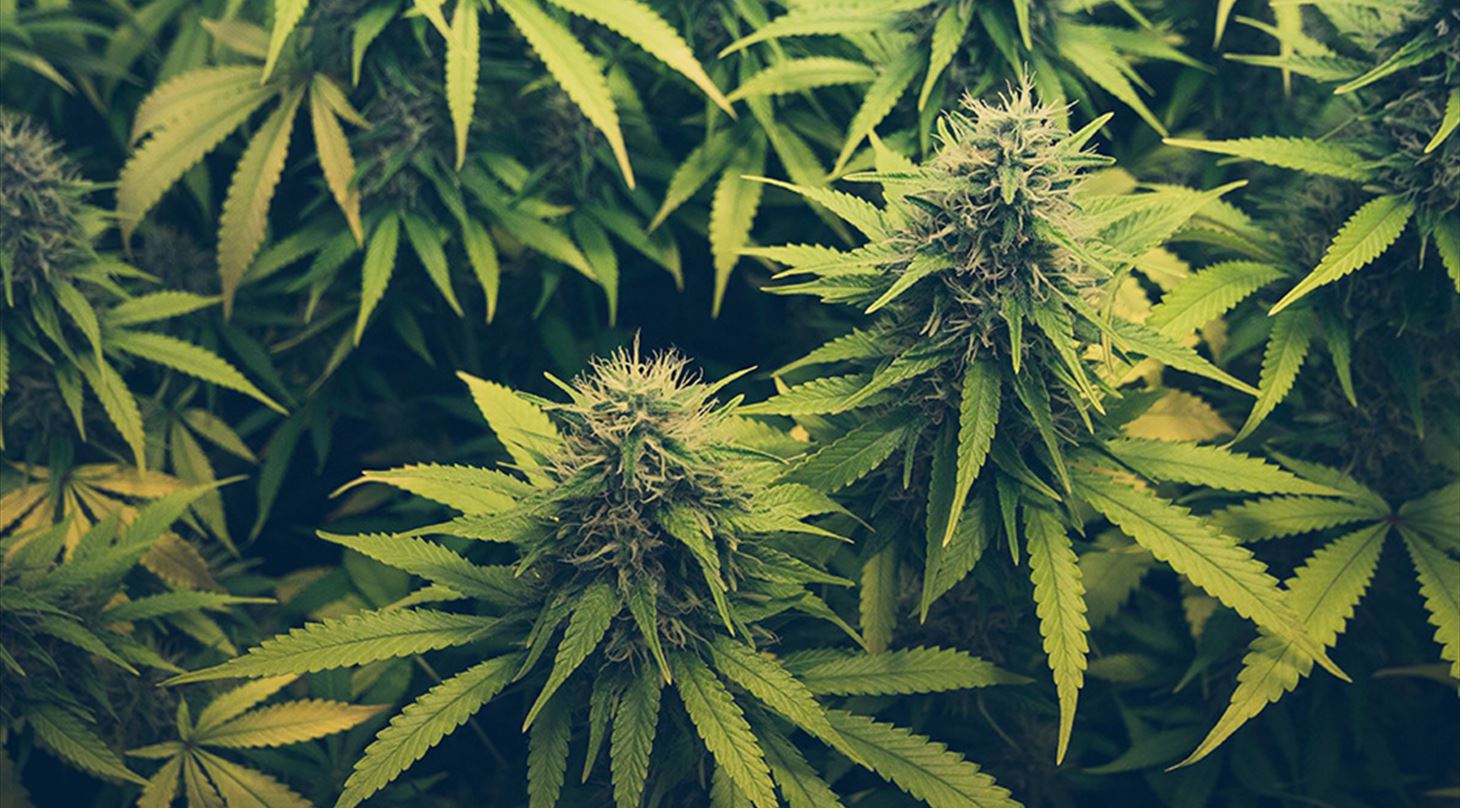
Danish hemp turns into biodegradable plates
Is it possible to injection-mold hemp to make 100% biodegradable plates? The answer is yes, but there is room for further development. This is what the startup Sustainable Service Solutions discovered in a MADE Material Demonstration Project, where the Danish Technological Institute helped develop and test the right hemp recipe.
Sustainable Service Solutions (SSS) is a green startup that manufactures packaging and service solutions for the restaurant and food industry. The company was founded by three business developers from these industries, and they aim to produce 100% biodegradable, recyclable tableware.
Therefore, SSS participated in a MADE Material Demonstration Project, collaborating with the Danish Technological Institute to develop biodegradable tableware made from Danish-grown hemp – for example, plates.
The project proved that it is possible to injection-mold hemp.
The guidance we have received is worth its weight in gold
- Kim Nielsen, Sustainable Service Solutions
Lack of technical knowledge led to MADE
SSS’s challenge was a lack of technical knowledge about the materials, or the injection molding process needed to produce the 100% biodegradable tableware.
- We have a sustainable agenda, but we don’t have the technical knowledge about the material and the injection molding process, says Sustainable Service Solutions.
SSS was recommended by their North Jutland supplier of certified THC-free hemp fibers (hemp fibers without cannabis) to apply for a MADE Material Demonstration Project. They did this to explore how much of the carefully selected hemp fibers could be implemented in the 100% biodegradable product, while still meeting other requirements and criteria. The image to the right shows the finished blended and granulated material, consisting of the biodegradable binder and hemp. The granulate has been divided into pellets and is ready for injection molding.
- The product must be 100% biodegradable, and for example, it should also withstand an industrial dishwasher – preferably many times – and it must be suitable for injection molding, says Jens Kromann Nielsen, product manager and specialist in advanced materials and process development at the Danish Technological Institute, who helped develop the hemp blend formula.
Not possible with 100 percent hemp fibers
SSS’s goal was to develop a product consisting of 100 percent hemp fibers, but due to the requirements mentioned above, tests showed that it was not possible. When they tried to injection-mold the granulate with a higher proportion of hemp, the granulate could not be fed through the machine and therefore could not be molded.
In the project, SSS has worked to find the right hemp formulas. This has been done with the help of the Danish Technological Institute, which has tested different percentages of hemp fibers in the ‘recipe’ – either hemp shives or hemp fibers – to create a prototype granulate for SSS to work with.You have to imagine that hemp fibers are similar in texture to rockwool insulation material, so it obviously needs something to bind it together. Therefore, we suggested using a suitable, 100% biodegradable binder
- Jens Kromann Nielsen, Teknologisk Institut
Based on the tests, a granulate has been developed, which in a confidential formula consists of hemp shives and a 100% biodegradable binder. The image on the left shows rings injection-molded from the granulate.
- If you increase the percentage of hemp shives or fibers, problems can arise with feeding during the mixing process, and then the mixture becomes too thick to be extruded through the small nozzles of the blending machine. That’s why we ended up with the specific blend, says Jens Kromann Nielsen.
A success with development potential
For SSS, it is a success to have developed a formula, and the startup now has a material that has been successfully injection molded.
- We have done what we hoped for; namely, to find a usable formula. So for us, it is a success. Of course, we can continue to work on it, and hopefully implement a higher proportion of hemp in the blend, says SSS.
According to SSS, the MADE Material Demonstration Project has contributed to a deeper understanding of the material and the concept of circular economy. In addition, the entrepreneurs point out that, through the MADE project, they have expanded their network and established relationships with experts, suppliers, and other entrepreneurs who can help them advance their agenda.
- To others considering applying for a MADE project, I would say: Just get started. It’s a fantastic experience. We felt well-supported by the Danish Technological Institute, we were kept informed along the way, and we were invited behind the scenes. The guidance we received is worth its weight in gold, concludes Kim Nielsen.
About the MADE Material Demonstration Projects
With a MADE Demonstration Project, a small or medium-sized company can receive up to DKK 100,000 in support to solve a specific challenge or test a new technology in production.
By connecting with the Danish Technological Institute, FORCE Technology, Alexandra Institute, and DAMRC, companies gain access to the technologies, knowledge, and skills necessary to solve their specific challenge.
This can involve either materials or production. There are ongoing application deadlines for demonstration projects. The next deadline is 1 February 2024. MADE Demonstration Projects are made possible with support from the Danish Industry Foundation and the Danish Board of Business Development.