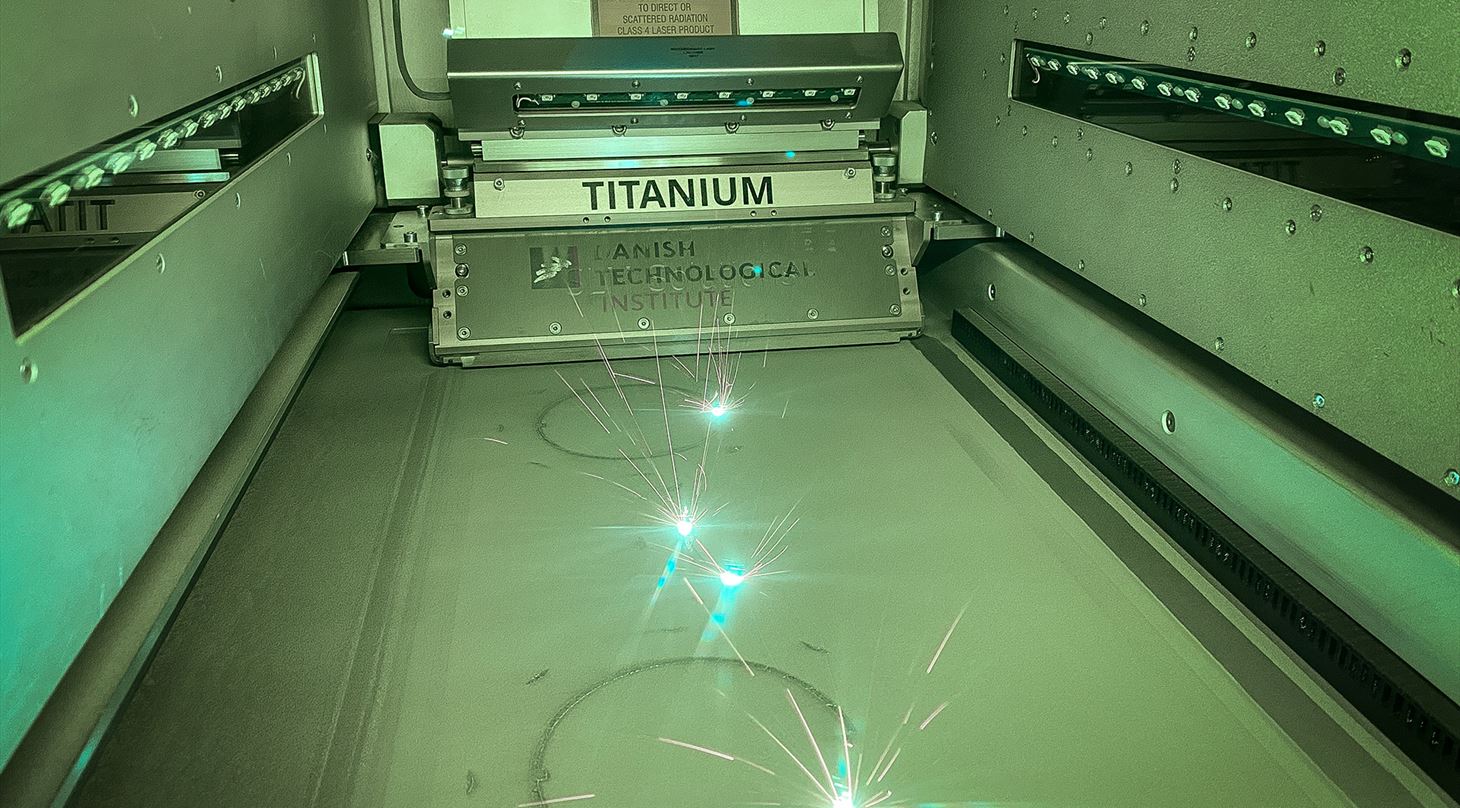
Newtec got familiar with 3D printing in MADE project - "It was easier than expected"
In a MADE Demonstration project together with the Danish Technological Institute, the Danish machine manufacturer Newtec has tested metal 3D printing on two exciting applications: a nozzle in stainless steel and a sorting roller in titanium. For Newtec, the experience from the project was surprising - it turned out that metal 3D printing is both cheaper and further developed than they expected. The experience has already proved useful in other parts of Newtec.
The Danish company Newtec produces weighing, packing, and sorting machines - mainly for the fruit and vegetable industry. Newtec was part of a MADE demonstration project to gain new knowledge about 3D printing.
- We chose to apply for the MADE Demonstration project, as it gave us the opportunity to work with metal 3D printing for the first time, says Bjarke Jensen, who is a research scientist at Newtec
For 3D printing of the metal parts as well as consultancy and sparring about the development, Newtec received help from the Center for Industrial 3D printing at the Danish Technological Institute.
- At the Danish Technological Institute, we have helped Newtec with 3D printing in metal, and they have gained extra knowledge about the technology - e.g. what it can do and how to design for it, but also how the finishing looks and how the quality is, says Sigurd Vigen Pedersen, consultant at the Danish Technological Institute and Newtec's contact person in the MADE demonstration project.
Two birds with one stone
There were two applications that Newtec wanted to uncover in the MADE demonstration project. The first application was a nozzle, and according to Bjarke Jensen, it was quite obvious to produce with 3D printing due to its conical shape.
The project where the nozzle is to be used is a development project, and there is still some way to go before we have a real product. But the MADE demonstration project has given us valuable insight into metal 3D printing and its possibilities
- Bjarke Jensen, Newtec
The second application was a large sorting roller with grooves, and here the focus was on testing materials. The roller itself was not necessarily the most obvious part to make with 3D printing, as the part was large. But with a modest investment, Newtec was given the opportunity to test titanium as a material for an important component on one of their machines. Here, 3D printing was thus used as a prototype tool, and it provided insight into the possibilities of using titanium as well as what surface treatments the part can get to become more resilient in production.
- In the project with the roller, we have had the opportunity to test a new material that would otherwise have required a large investment. Whether it turns into something concrete is too early to say, but our tests gave promising results, says Bjarke Jensen, and adds:
- Our laboratory is already working closely with national and international researchers and scientists, universities, and PhD students to identify new developments and gain insight into what has the potential to transform the entire industry tomorrow. Be it advances in materials science, nanotechnology, the next generation of optics, artificial intelligence (AI) and a myriad of other industry-related technologies, says Bjarke Jensen.
See an example of one of Newtec's packaging machines in the video below.
3D printing is cheaper - and further developed - than expected
One of the major experiences that Newtec takes away from the project is that metal 3D printing is further developed than they had anticipated.
- We were surprised that the technology is already as far advanced as it is. Furthermore, it was easier than expected, but also cheaper than expected. We had not expected that the 3D-printed nozzle would be cheaper than a similar stump made in the traditional way, says Bjarke Jensen.
With 3D printing, the nozzles have become significantly cheaper than if Newtec had to design and produce the optimized nozzle in a conventional way. Before, there were five parts that had to be assembled, and now there is only one optimized part where cooling fins have been added, and it has a better air flow - this results in a significant time saving in assembly. 3D printing has thus been an essential technology in this project, which has resulted in good, practical, and usable results.
It has been valuable to have a close dialogue with Newtec in the design and optimization process. That way, we have been able to take full advantage of the possibilities with 3D printing, but also make sure that the part is as simple as possible to manufacture – i.e. with minimal post processing
- Sigurd Vigen Pedersen, Danish Technological Institute
Positive experiences for the future
Newtec is now working on the nozzle, and the sorting roller requires some more tests.
- The nozzle fulfils the purpose it has right now, and the project has shown that metal 3D printing is a usable technology - also in terms of cost. Especially if you make some slightly obscure shapes. For the roller, there is still some work ahead, but the different coatings look super interesting, and so does the material, says Bjarke Jensen.
Experience reduces barriers
The MADE demonstration project has given Newtec an insight into the possibilities of metal 3D printing, and already now the company can see other projects and parts that can benefit from the technology.
- Ultimately, for us, it is about adding value to our customers' production and delivering the best quality with cost-effective machines and solutions that will continue to work for many years to come. With our own laboratory, we ensure that even the smallest components are quality-assured and food-approved in relation to e.g. material and surface treatment, Bjarke Jensen explains before he goes on to conclude:
- As a consequence of the results in the MADE Demonstration project, we have just discussed the possibility of moving forward with metal 3D printing in a completely different context. Here, we need a weight saving on some parts in our cameras, which we develop and produce for our optical sorting machines. In addition, I recently spoke with one of our other designers who was considering metal 3D printing for a small component because it is so difficult to manufacture in a conventional way. So the fact that we have gotten familiar with these things means that the activation barrier has been significantly reduced for us.
A MADE Demonstration project is a really good opportunity to test metal 3D printing and get some experience with the technology. You can assess whether it can be used in the company - and whether it can add value or not. Once the experience is gained, the basis for decision-making is better and the barriers are fewer.
Facts about the project
Title: ’Metal 3D-printed components for the next-generation of packaging and sorting machines’
Project period: 22. september 2020 – 30. april 2021
Project partners: Danish Technological Institute and Newtec
This article is a translation of the article ”Det var nemmere end forventet”: Newtec har fået 3D-print ind under huden via et MADE Demonstrationsprojekt” published by MADE – the national cluster for Advanced Production.