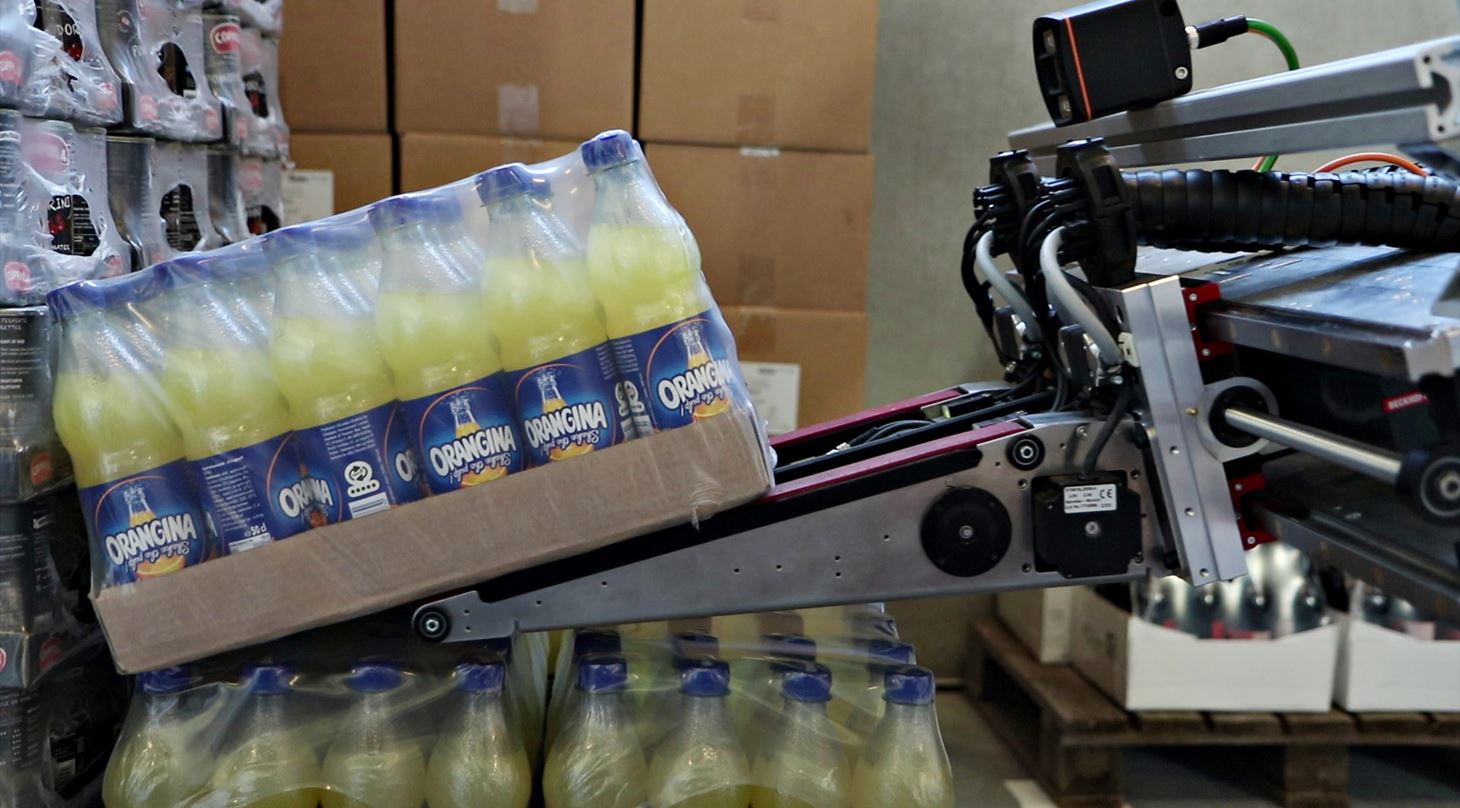
The seven most overlooked opportunities for robots and automation in manufacturing companies
Do you also have the feeling that you are missing out on opportunities with robots and automation? Robot consultants at the Danish Technological Institute (DTI) identify seven areas or process types in the manufacturing industry that can be advantageously automated.
Many companies have a realisation that they are missing opportunities for automation.
This is shown by our survey of 122 business leaders, where 69 percent of companies that already have robots find that they are missing opportunities to automate further.
In the article below, DTI's experienced robot consultants identify the areas and tasks that most companies could benefit from automating - and which many overlook either due to a lack of knowledge or a focus on daily operations.
1. Automation of quality control
Many production systems perform quality control using spot checks, as it is not possible to have staff staring at uniform items for several hours each day.
Fatigue, errors, and the speed required mean that personnel can only do quality control checks in short shifts so either a large number of personnel have to be trained or the quality control task gets reduced to a random check.
It is possible to use camera technology (and an increasing number of artificial intelligence options) to perform continuous quality control that sees each product and at the same time creates traceability for each item and each product type.
Automatic quality control can also be useful on the input side – that is, checking that you get what you paid for.
2. Automation of transport
In our daily work, we often have small tasks where we must move an item from one station to another. It may only be 50 meters to walk, but it takes time away from focused work.
This can be solved with a simple mobile robot that can shuttle between set destinations like a taxi that is called when goods are ready to be moved.
3. Automation of handling (and processing)
Although handling is a task that most companies automate, it is still worth mentioning as an overlooked opportunity.
The robot is often seen as the executing actor, screwing, grinding, or otherwise processing a workpiece. But another option is to let the robot control the workpiece while a human uses the tool.
In this way, it can be easier for the employee to reach all corners, look into all nooks and crannies, or ensure all tolerances, all the while maintaining a good working environment without poor working postures.
4. Automation of welding
With the increase in the number of "collaborative" robots - also called cobots - there are also better opportunities for manual welding tasks to be automated via the process-savvy welders transferring some of their knowledge to the user-friendly robots.
Then the employees could avoid the boring and physically demanding repetitive work, the sparks flying around the ears, and having to man the welding station around the clock. The whole process becomes safer.
5. Automation of palletising
Cobots are becoming able to lift more and more and reach further and further. This makes them suitable for taking over more of the heavy, manual palletising tasks.
A cobot's user-friendly programming also means that you do not necessarily need to bring in an expensive engineer, but can upskill your operators to program the desired palletising patterns.
In addition, a forest of 'plug and play' tools has gradually grown up that can suck, grab or otherwise handle your product, whereas in the past you had to get someone to develop a special tool.
However, classic industrial robots may still be the best way to go in several cases, depending on size, weight, and the production environment.
6. Automation of counting
1, 2, 3... Many companies still require employees to manually count products into packs or sets, for example, 30 items in a package.
Counting can be advantageously automated – possibly also in combination with quality control and automated packaging of the products.
7. Partial automation
Not all tasks can or should be 100 percent automated.
Often it is advantageous to have a robot handle items and solve 80 percent of the repetitive work and then have personnel handle the last 20 percent, which is often more complex.
This leads to a cheaper solution that is faster to implement and service. It also leaves company employees with more interesting and less physically demanding tasks.
From ambition to investment
Only 12 percent of Danish companies have a written strategy for automation and robots – and a strategy by itself is not enough. You must have a plan for how to go from ambition to investment.
DTI can help you with that.
Our experienced specialists and consultants guide you through all phases - from strategic planning to implementation.
Contact Henrik Jacobsen from DTI at hnjn@dti.dk or +45 72 20 28 15 if you want to know more.