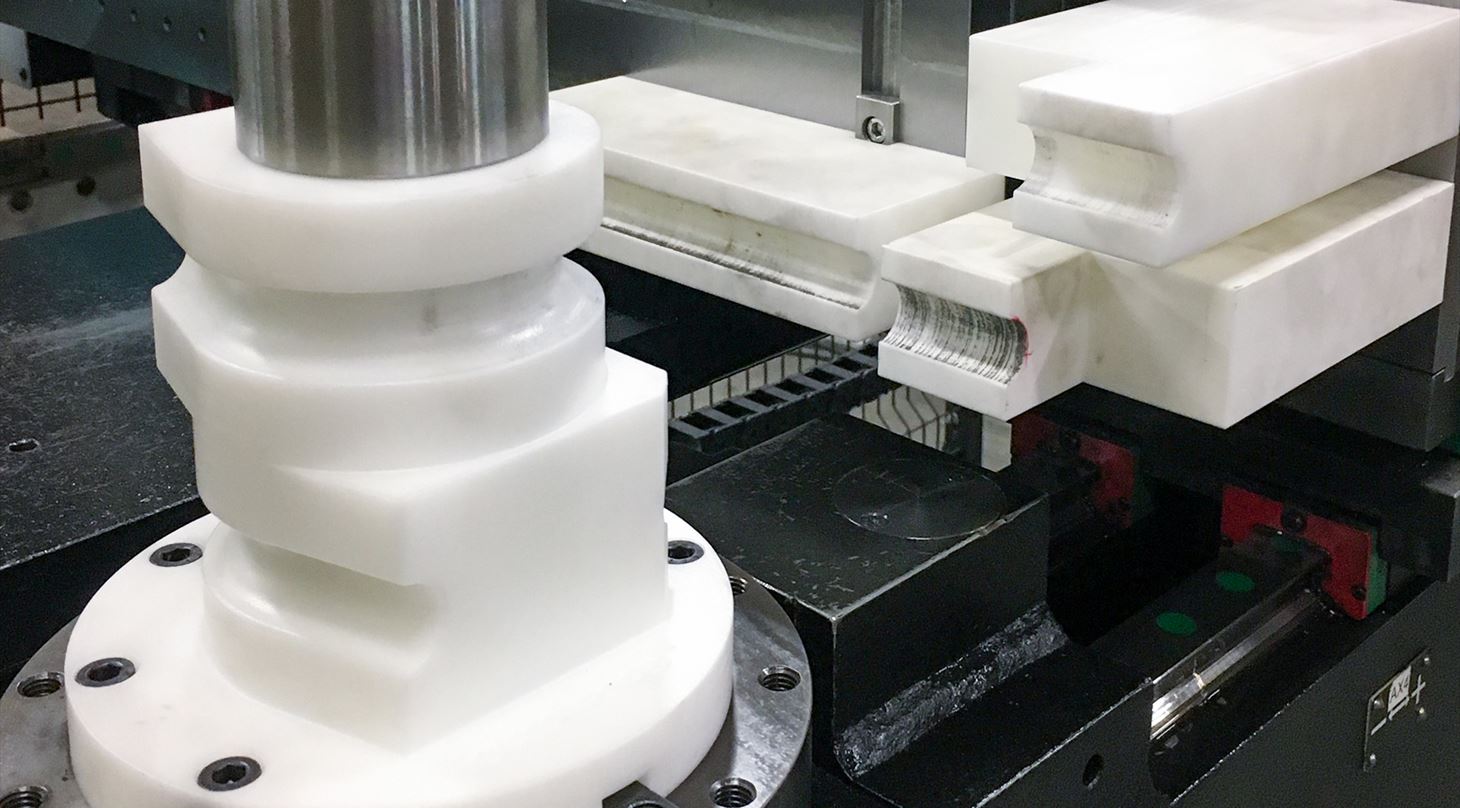
BSM gained new insight into 3D printing - "We see a 1,000 other scenarios for the technology"
Scratches and marks on designer furniture do not work. Therefore, the Danish family-owned company BSM investigated whether it is possible to replace steel tools with softer 3D-printed tools in the manufacture of tubes for the furniture industry – this was done in collaboration with the Danish Technological Institute in a MADE Demonstration project.
For the past 40 years, BSM has gone from a traditional forging company to a high-tech machine factory with some of the latest machines for metal processing. The SME from Bjerringbro specializes in manufacturing for the quality-demanding furniture industry, and it was in this connection that they wanted to investigate whether 3D printing could contribute to production.
Specifically, BSM wanted to test 3D printing of bending tools for tube bending as well as 3D printing of 1: 1 furniture prototypes, and then they wanted to investigate which printing technologies were best suited for these purposes. In the MADE demonstration project, BSM collaborated with the Danish Technological Institute's Center for Industrial 3D Printing to uncover the possibilities.
From the beginning, we might have considered 3D printing for one purpose, but now that we've gained hands-on experience with the technology and know what can be done, we suddenly see a 1,000 other scenarios where it can be used
- Kristian Wolthers Rasmussen, Product Developer, BSM
Testing and sparring provided new experiences
BSM carried out several tests during the project, where the Danish Technological Institute helped with advice on 3D printing - including how to design for the technology - as well as the production of 3D-printed parts.
- BSM had a hope that 3D printing could accelerate a time-consuming development process for new products. At first glance, they have not innovated and invested as much in this area as in the production apparatus itself - therefore the process is still relatively expensive and time consuming. The MADE project was a good opportunity for BSM to gain more knowledge about how 3D printing could help them optimize both the development and parts of production, says Kristoffer Ryelund, business manager at the Danish Technological Institute.
- The collaboration with the Danish Technological Institute has been very positive. It was always easy to get in touch with them, and their advice in the project has given us a greater knowledge of how we construct, design, and optimize parts specifically for 3D printing, says Kristian Wolthers Rasmussen, Product Developer at BSM.
Overall, the project gave a lot of new experience regarding the use of 3D printing. BSM gained greater knowledge of which 3D printing technologies make the best sense in different contexts. In this project, for example, it turned out that SLA and SLS, which are both plastic printing technologies, were best suited as they gave the best combination of high resolution and great strength on the 3D printed parts.
In the video below, you can see what it looks like when BSM bends tubes for the furniture industry using 3D-printed tools.
Bending tools revealed both challenges and opportunities
When bending tubes, there is a big difference in how difficult a bend is to perform - and thus also how great the requirements are for the bending tools. In the MADE demonstration project, BSM has been successful in performing easy bends with a fully 3D-printed tool set for both prototypes and zero series. In this context, a full toolkit consists of a main die, a press resistance, and a gripping resistance.
For more difficult bends, BSM experienced challenges in being able to grip the tubes adequately with the 3D-printed bending tools. This is a general problem when bending tubes - especially in the design world, where there is often a short length between each bend. The challenge is even more pronounced in the furniture industry because there can be no marks. Therefore, you cannot just grip harder on the tubes, even if it is possible with the existing steel tools. With the 3D-printed tools, the challenge arises because plastic is softer than steel, so you CANNOT grip as hard - and due to the difference in strength, the 3D-
- In order to succeed with the 3D-printed bending tools, we must continue to work with the strength of them - and with the grip problem. Among other things, we will test other materials and other structures on the surface plus new designs of the grip resistance. Some things work and some things do not work, but we have not yet found an easy solution to the challenge, says Kristian Wolthers Rasmussen.
On the other hand, the 3D-printed tools have the advantage that there are far fewer scratches or marks in the tubes that are bent, and this is important when the tubes are used for designer furniture - with steel tools there are sometimes marks that subsequently need to be sanded and polished.
- The starting point for the project was to accommodate scratches and marks, so in that way it has clearly been a success. But it is a bit of a compromise because the existing steel tools are more expensive and have a longer lead time than 3D-printed tools - on the other hand, 3D printing has a shorter lifespan, says Kristian Wolthers Rasmussen.
Optimized production with 3D printing
As mentioned in the introduction, BSM had a hope of reducing development time with 3D printing, and at the same time they wanted to offer customers a more flexible and less costly process, which hopefully could also optimize the collaboration. Finally, 3D printing had to reduce 'wasted time' in production, as production would only begin when 3D-printed models had ensured that they had the right design, so that no corrections had to be made along the way.
It is still too soon to conclude anything precise in terms of the reduction of development time, as the project continues to run internally at BSM - but the expectation is still that the development time can be significantly reduced.
- We can measure the cost price and delivery time of e.g. bending tools, and here we can see that 3D printing is cheaper - how much cheaper depends on the part being printed. On delivery time, 3D printing is approximately twice as fast. Will the 3D-printed bending tools then work in production? We cannot really conclude that yet, says Kristian Wolthers Rasmussen.
BSM has run some major tests and cycles with 3D-printed bending tools to see how long it takes before they break or make a bend that is not within tolerances. But it is necessary to test over a long period of time, and BSM will continue to do so whenever possible - so far, it is only a specific type of order where BSM uses 3D-printed tools.
- If 3D printing does not work 100 percent for bending tools, then at least it does for the manufacture of complex parts for furniture prototypes or fixtures for early prototypes. Both parts can be made faster with 3D printing, so no matter what, it makes sense for us to use the technology - also for the production of very small series, says Kristian Wolthers Rasmussen and adds:
After gaining more experience with 3D printing, we can offer our customers new opportunities to get 3D-printed prototypes. This allows them to see their design in a physical sense and make changes before production begins - it is both an advantage for them and for us
- Kristian Wolthers Rasmussen, BSM
The project was a technological eye opener
At BSM, the goal of learning more about how 3D printing can be used has clearly been achieved, and the demonstration project has opened the eyes to the many possibilities that 3D printing can provide in terms of optimizing production and prototype development.
Although the internal process has not yet been fully completed - and hasn’t given exactly the results that were hoped for in all areas - BSM believes that the new knowledge about 3D printing will bring the company closer to the vision of shorter delivery times. In addition, they suddenly see many other options with 3D printing.
- Whether the project is 100 percent achieved is actually irrelevant - we have gained valuable experience with 3D printing, and now we see the technology as a tool we can develop and use, Kristian Wolthers Rasmussen concludes.
He has no doubt that BSM will work much more with 3D printing in the future. Therefore, he does not hesitate to recommend the MADE Demonstration Project to companies that may face similar challenges and needs:
- If you have the hours for it, then it makes very good sense to apply for a MADE demonstration project - it is a good opportunity to get in depth with a new technology and get it tested.
Facts about the demonstration project
Title: ‘Uncovering of 3D for the development process in a steel production’
Project period: July 2020 – February 2021
Projekt partners: Danish Technological Institute and BSM
This article is a republishing of "Vi ser 1.000 andre scenarier for 3D-print”: BSM fik ny indsigt i MADE Demonstrationsprojekt" published by MADE