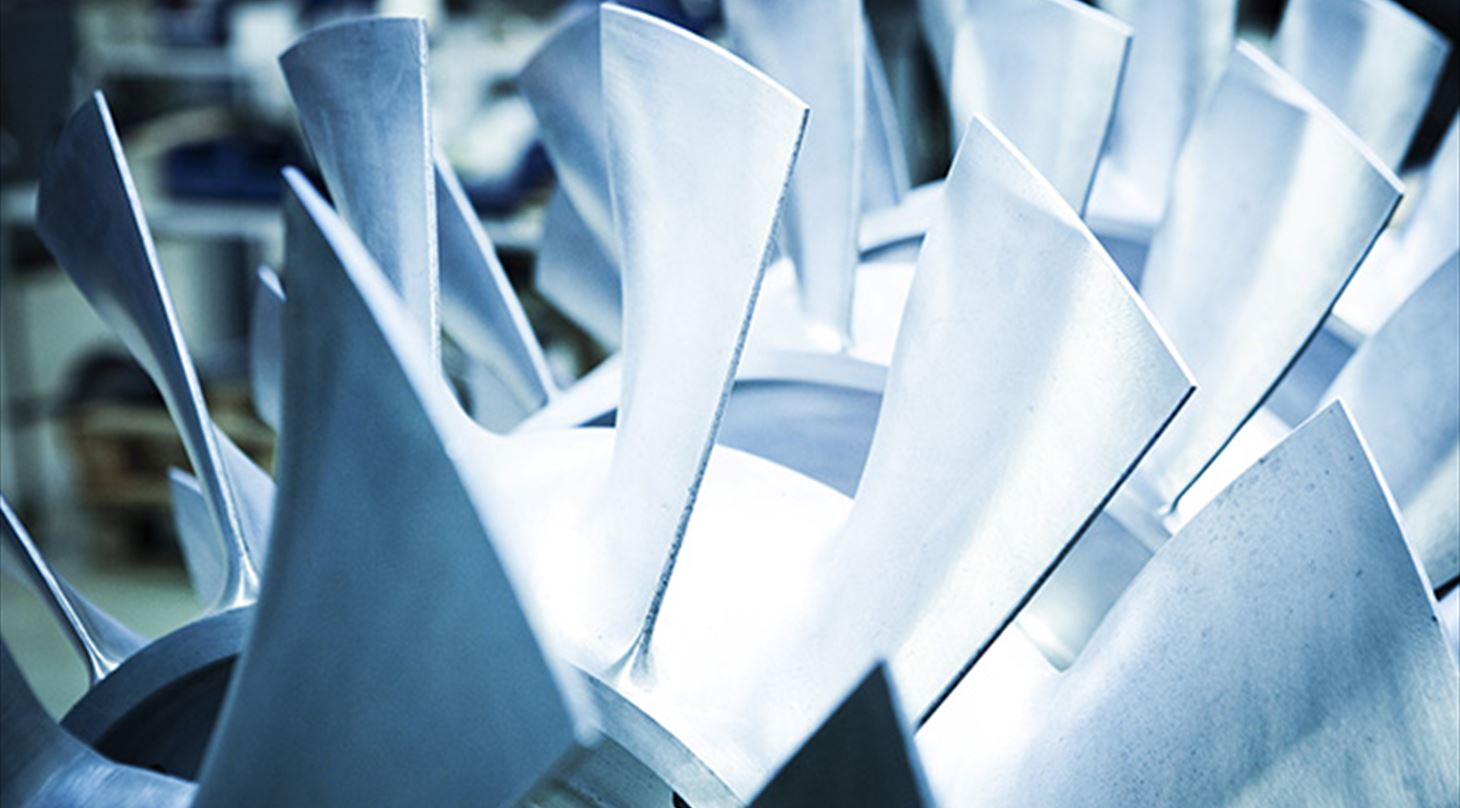
Residual stress in metals
Residual stress and strain in e.g. steel and aluminum components will build up during material processing and use.
The residual stress state has a huge impact on the properties of the material, such as its fatigue strength and resistance to stress corrosion cracking, and thereby on the lifetime of the product. Based on knowledge of the level and distribution of stress, it is possible to obtain better, more cost-effective and reliable products, e.g. by validating or providing input for Finite Element computational models.
Challenges with residual stress will often manifest either in the form of deformation after machining and fatigue fractures, while also leading to the use of exaggerated safety factors.
Knowing the residual stress levels makes it possible to:
- Optimize component design .
- Achieve better production procedures (e.g. machine settings).
- Streamline product development and reduce the time-to-market.
- Reduce over-conservative safety procedures or -factors
- Reduce material consumption.
- Improve lifetime and lifetime estimates of products.
- Ease/diminish the need of (extra) warranties or spart part stock.
We apply many different analysis techniques depending on the individual sample and desired information about residual stress. The residual stress can be measured accurately using both destructive and non-destructive methods, and information depth can range from surface-only to several cm in depth. As the best suited method varies significantly with material, geometry and processing history, each case is unique.
The choice of method depends on the component geometry, material, required spatial resolution, and on how deep into the material measurements are required. Ask our specialists to find out how we best can perform measurements on your product.
Besides the more traditional techniques for residual stress determination such as lab-based X-ray diffraction, hole-drilling and contour mapping, we offer residual stress measurements using X-ray or neutron radiation from large research facilities. Such analysis can determine the full magnitude and physical directions of stress in 3D inside an object. The techniques are non-destructive, and have fewer restrictions on object geometry. Due to the non-destructive nature, they also provide the opportunity to follow stress/strain evolution during processes such as fatigue testing or manufacturing.