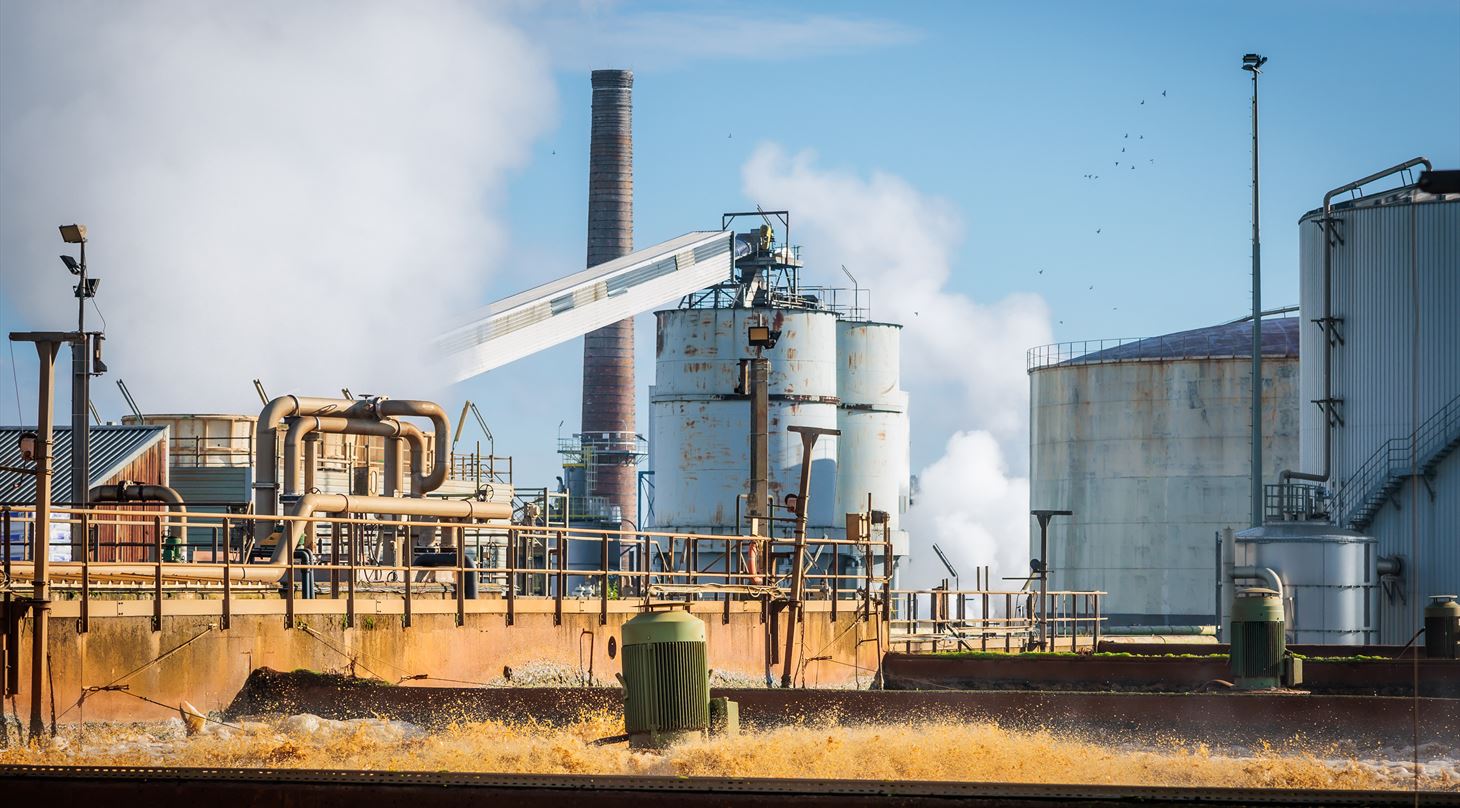
SPIRIT - Implementation of sustainable heat upgrade technologies for industry
Design of new high-temperature heat pumps for process industry. High-temperature heat pumps are a key technology in the electrification of the process industry as well as in efforts to reduce CO2 emissions from the industry's process heat towards 2030. Right now, Danish Technological Institute is participating in an international project - SPIRIT - which is precisely about demonstrating high-temperature heat pumps for process heat delivery at temperatures up to 160 °C.
The purpose of the SPIRIT project is to demonstrate stable and robust operation of three industrial heat pumps, integrated into operational production facilities at a Belgian sugar company, a Norwegian prawn processing plant, and a Czech paper mill. Three well-known technology providers (GEA, Mayekawa and Spilling) will design and construct the industrial heat pumps which will use waste heat and upgrade this waste heat to supply temperatures of 139 °C, 143 °C, and 157 °C. These demonstrations will increase the technical knowledge of and provide guidelines on heat pump integration in industry, and at the same time it will be demonstrated that industrial heat pumps can be integrated into existing processes without disturbing the production process.
The potential is great in the selected sectors. The paper & pulp and the food & beverage industries together cover 63 % of the potential high-temperature heat upgrade market. The expectation is that demonstration of the technology at these temperatures will pave the way for further development to achieve even higher temperatures in the future and thus spreading the use of the technology in the industry even further.
Improved technical and economic performance
In the project, work must also be done to improve the technical performance. Technical performance will be enhanced by reducing efficiency losses and by extending the operating range of compressors, reduce heat loss from oil cooling, and by using zeotropic working media.
Economic performance is improved by lowering both capital expenditures and operating costs. Capital expenditures are lowered, i.e., by using standard components in the heat pump, and operating costs are reduced by increasing the technical performance and developing compressor designs that require less maintenance.
Significant reduction of energy consumption
The project aims to have a sustained operation of between 2000 and 4000 hours per year for each demonstration system. This will demonstrate heat pump technology as a robust and reliable technology. At the same time, there is an expectation that a reduction in energy use of at least 30 % will be achieved - and as a result, a corresponding reduction in energy costs and CO2 emissions
The impact of industrial heat pumps must be maximized
In SPIRIT, strategies must be developed to ensure that the effect of industrial heat pumps is as great as possible. The activities include a comprehensive market assessment, including spin-off to other sectors (e.g., district heating) and benefits in terms of energy and CO2 emission reductions. Business cases for several sectors will be analyzed, and possible policy, regulatory and other non-technical barriers preventing the deployment of heat pump technologies will be analyzed with recommendations to overcome these barriers. Finally, a web-based tool is developed that allows end-users to assess the benefits of industrial heat pumps.
Demonstration at three sites
In the project, three technologies will be demonstrated at three different demonstration sites. The three plants will be demonstrated in relevant capacities for representative applications to emphasize their broad applicability and maturity in terms of electrifying entire industries:
Tiense Suiker’s primary sugar production process is fossil fuel-driven with boilers. The fuel for the boilers is primarily natural gas with a smaller amount of own produced biogas (around 4 %). A fraction of the fuel currently used is coal, which will be phased out soon and replaced with natural gas. The amount of CO2 created based on the current energy supply is around 100 kton/year.
Tiense Suiker's long-term ambition is to electrify its sugar refinery process fully. The first step to achieve their goal is to join the SPIRIT project and integrate a high-temperature heat pump in their production process. The technology provider coupled with Tiense Suiker is GEA. GEA is German experienced manufacturer of customized heat pumps for a wide range of temperatures and capacities.
The goal is to demonstrate a GEA heat pump system with a screw compressor to generate steam around 139 °C at a 4 MW capacity, replacing the steam produced from fossil fuel-based boilers. Tiense Suiker's production processes will thus be partly electrified, and it is expected that the demonstrated technology has the potential to eventually electrify the entire process heat demand at Tiense Suiker.
Stella Polaris aims toward a climate-neutral production; consequently, they have joined the SPIRIT project. The goal is to demonstrate a high-temperature heat pump based on a screw compressor with a hydrocarbon as the working fluid.
The heat pump will supply steam temperatures at around 143 °C with a capacity of 1.2 MW, replacing the steam produced from the fossil fuel-based boiler, and hence electrify the prawn cooking production processes of Stella Polaris. The technology provider for this demonstration case is Mayekawa, an experienced manufacturer of customized heat pumps for a wide range of temperature and capacities.
Steam is the driving force for any drying process of the paper sector, which for the demonstration site of Smurfit Kappa is being produced by using a natural gas boiler. The production of steam is done using a boiler that utilizes natural gas (95 %) and biogas (5 %). The yearly fuel consumption of such an installation is in the order of 353 TJ which translates into almost 19 kton of CO2 per year.
The ambition of Smurfit Kappa is to reduce the dependence on fossil fuel sources and to reduce their CO2 emission. Therefore, the integration of industrial heat pumps and the participation in the SPIRIT project align with their ambition.
The technology supplier chosen for this demonstration case is Spilling, who has a portfolio of steam compression systems capable of raising the pressure of unusable low-pressure steam or waste/excess steam from production. The Spilling piston compressor will produce high-pressure steam (6 bar), delivering 0.7 MW of heat at a temperature of 157 °C to the process.
About the project
In this project, which will run for three and a half years (starting September 2022), Danish Technological Institute will collaborate with a wide range of partners. The project group is strong and consists of technology suppliers, end-users, knowledge providers and business and market experts:
- TNO (coordinator), Deutsches Zentrum für Luft- und Raumfahrt, European Heat Pump Association, Mayekawa, SINCLOC, EURAC, Euroheat and Power, Technical University of Denmark, TVP Solar, Tiense Suiker, TLK Energy, GEA Refrigeration Germany, Spilling Technologies, Smurfit Kappa Paper Services, Smurfit Kappa Czech and Stella Polaris.
The project receives funding from the European Union’s Horizon Europe research and innovation programme under grant agreement No. 101069672 (SPIRIT).
Photo: Tiense Suiker.