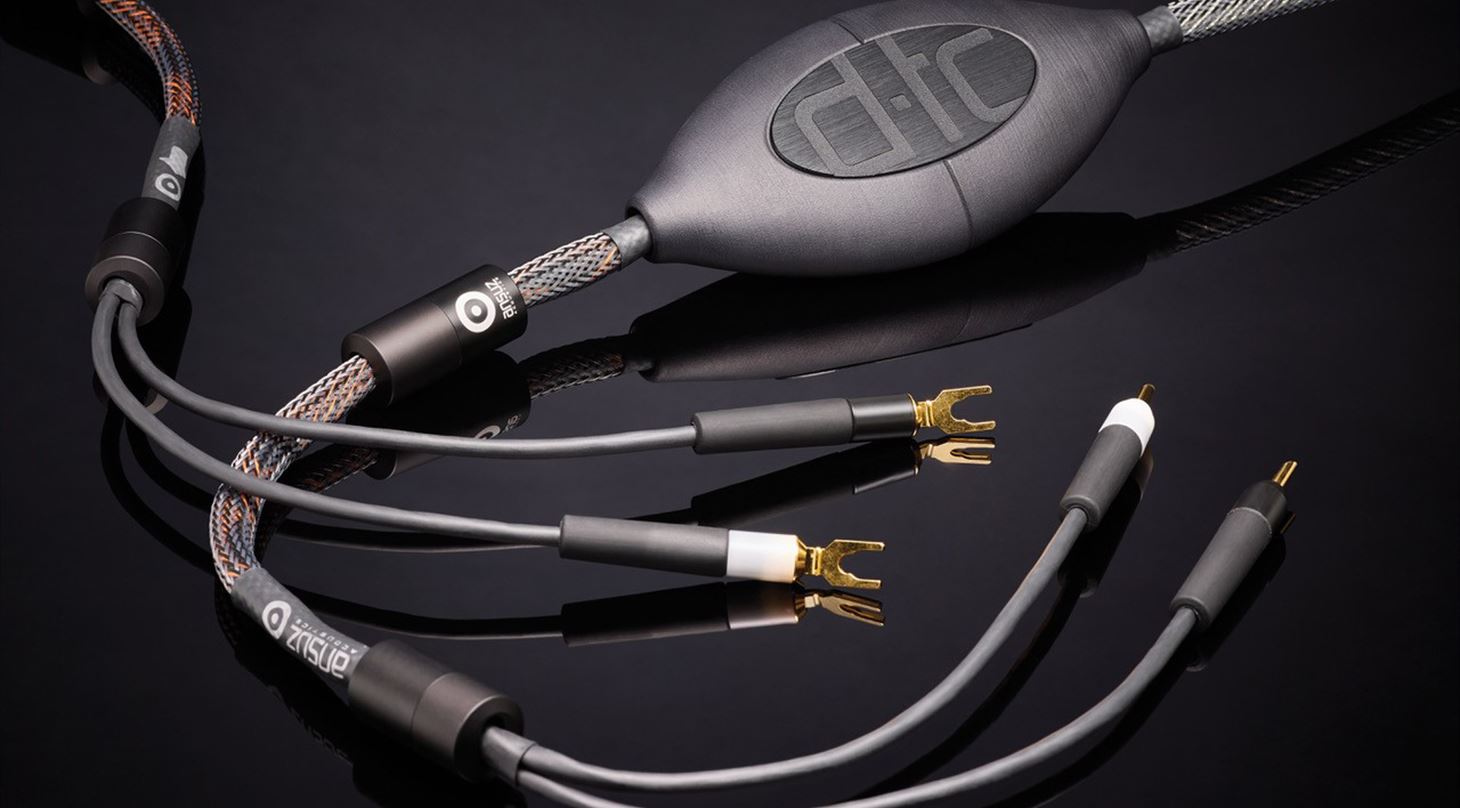
3D printing encapsulates supreme sound from Ansuz Acoustics
Ansuz Acoustics is a Danish company that develops and manufactures cables and accessories for high-end music systems, and with tremendous freedom of design and short development time on new products, 3D printing has proven to be the perfect solution for the housing where the cables are assembled.
Ansuz Acoustics is a market leader in their narrow field, and they take pride in spoiling their audiophile customers with solutions that make any music system perform to its fullest. So, if you just bought an exclusive anniversary pickup from Ortofon, a NAIM audio system and a couple of state-of-the-art speakers from Aavik, a set of cables from Ansuz Acoustics will be the icing on the cake.
One of the technologies used by Ansuz Acoustics to achieve the best results is Additive Manufacturing, which is used to make the housing where the cables are assembled and where the electronic processing takes, thereby making the sound in the speakers noticeable better. The housing is 3D-printed at the Danish Technological Institute, which Ansuz has worked with for a number of years.
Let us help you with AM production
- As a company we have always been aware that Additive Manufacturing existed. But the fact that we can use it for production is due to the fact that the technology has matured over time. And the printers used by the Danish Technological Institute are a perfect match for some of the requirements that we have for our components, says Michael Børresen, Development Manager at Ansuz Acoustics.
To begin with, Ansuz Acoustic was a client in the Tribology Center at the Danish Technological Institute's, where they had various cosmetic coatings applied to their products. It was through this collaboration that the company was introduced to Additive Manufacturing at the institute approximately five years ago – and to the opportunities offered by the technology.
The hi-fi industry is very seasonal, and time-to-market is crucial. That's why Ansuz Acoustics needs to be able to quickly develop components for their new product launches and continuously showcase news at trade shows and the like. This requires fast development and fast delivery, and Additive Manufacturing meets all these requirements.
Great freedom of design and minimal use of tools
The large cable houses that are 3D-printed at the Danish Technological Institute are almost 20 cm high with circumference like a pint of drinking water. Previously, these houses were assembled at the middle, but that made it more difficult to connect the cables and mount the electronics during the final production. Consequently, Ansuz Acoustics made a design change along the way so that most houses today are assembled longitudinally. The change required no use of tools, and it made production easier for Ansuz Acoustics, making it a very good example of the valuable design freedom offered by Additive Manufacturing.
- We have chosen to use Additive Manufacturing in production and not just for design verification because it provides us with an unparalleled freedom of design that allows us to build components that we couldn’t achieve though a casting process, says Michael Børresen.
The freedom of design means that Ansuz Acoustics doesn’t have to think about whether a particular design can be achieved through e.g. injection molding. In fact, the 3D-printed surface, which is not as smooth as seen with injection molding, is an intentional part of the design. Ansuz Acoustics even compares it to ceramics, where the large houses almost look like a vase with a turning track from where the hands have moved, so you can see the natural material in it.
See what we offer in terms of AM production
Based on these wishes, the Danish Technological Institute has then specified a surface where you can still see some of the layers from the construction process, and a black coloring that the houses must have every time - whether it’s the small or the large models.
- Through the collaboration with the Danish Technological Institute, Ansuz Acoustics has built up a greater knowledge of what you can do with Additive Manufacturing and what the limitations are, and they utilize that knowledge in their designs. In terms of the 3D printing itself, there may be some things where we optimize the process a bit - for example, it may make sense to thin out the material, so the houses weigh less and thus can be printed faster, cheaper and in a more monotonous way, says Mads Østergaard, section manager for the Additive Manufacturing production at the Danish Technological Institute.
During the development phase, Ansuz Acoustics also makes frequent use of revision changes that are easy to make with Additive Manufacturing. A typical course is that the Danish Technological Institute receives one or two models - revision A and B - which are printed together. Anzuz Acoustics get these back, after which cables and electronics are put together and everything is tested. Maybe there will be a few design changes, after which some new editions are printed and tested again. That way, Ansuz Acoustics can achieve 3-4 revisions in 1-2 weeks and then end up with a finished product which can be immediately produced - and the appearance doesn’t change compared to the prototypes, as all print parameters have already been set.
Additive Manufacturing is perfect for smaller series
In addition to enabling a rapid development phase, the Additive Manufacturing technology also has the advantage that you can make small series without the price per item being too high. This is crucial for Ansuz Acoustics, as they don’t produce very large volumes of these exclusive cables - and this is an important reason for choosing 3D-printed cable housings. To illustrate, the Danish Technological Institute currently prints about 50-100 houses a year for the large cables, and 2-300 houses for the smaller and cheaper speaker cables, where more cables can be assembled in one housing.
Furthermore, production with Additive Manufacturing means that Ansuz Acoustics has a very low inventory level. Many of the orders to the Danish Technological Institute are e.g. for 20 sets with delivery two weeks later in the quality that Ansuz wants. So, the inventory level and the delivery time are also important contributing factors when choosing Additive Manufacturing as production technology.
- We produce relatively small series. We do not need tens of thousands of items, we may need hundreds of items of a given design each year, and with Additive Manufacturing we have infinite freedom to have different variants, without the extra cost of tools or large inventory levels. And Additive Manufacturing also has the unique advantage that we can actually have a finished item in a few days. This flexibility is hard to do without in our company, says Michael Børresen.
Over time, the production has been so well established that the designer and the development manager are only in contact with the Danish Technological Institute when designing new housings. Other than that, it is procurement who makes contact when ordering more items – and then the Danish Technological Institute knows the quality requirements and has reference items in stock so that the items can be quickly produced and delivered.
- In our collaboration with the Danish Technological Institute, we always encounter a great hospitality and flexibility as well as a willingness to try out new things. It's easy for me as a designer because the Danish Technological Institute knows what needs to be done and how the finish should be when I send them my drawings, so the accuracy is extremely high. On top of that, I don’t feel treated like a customer, but more like a partner, and that's really nice, Michael Børresen concludes.