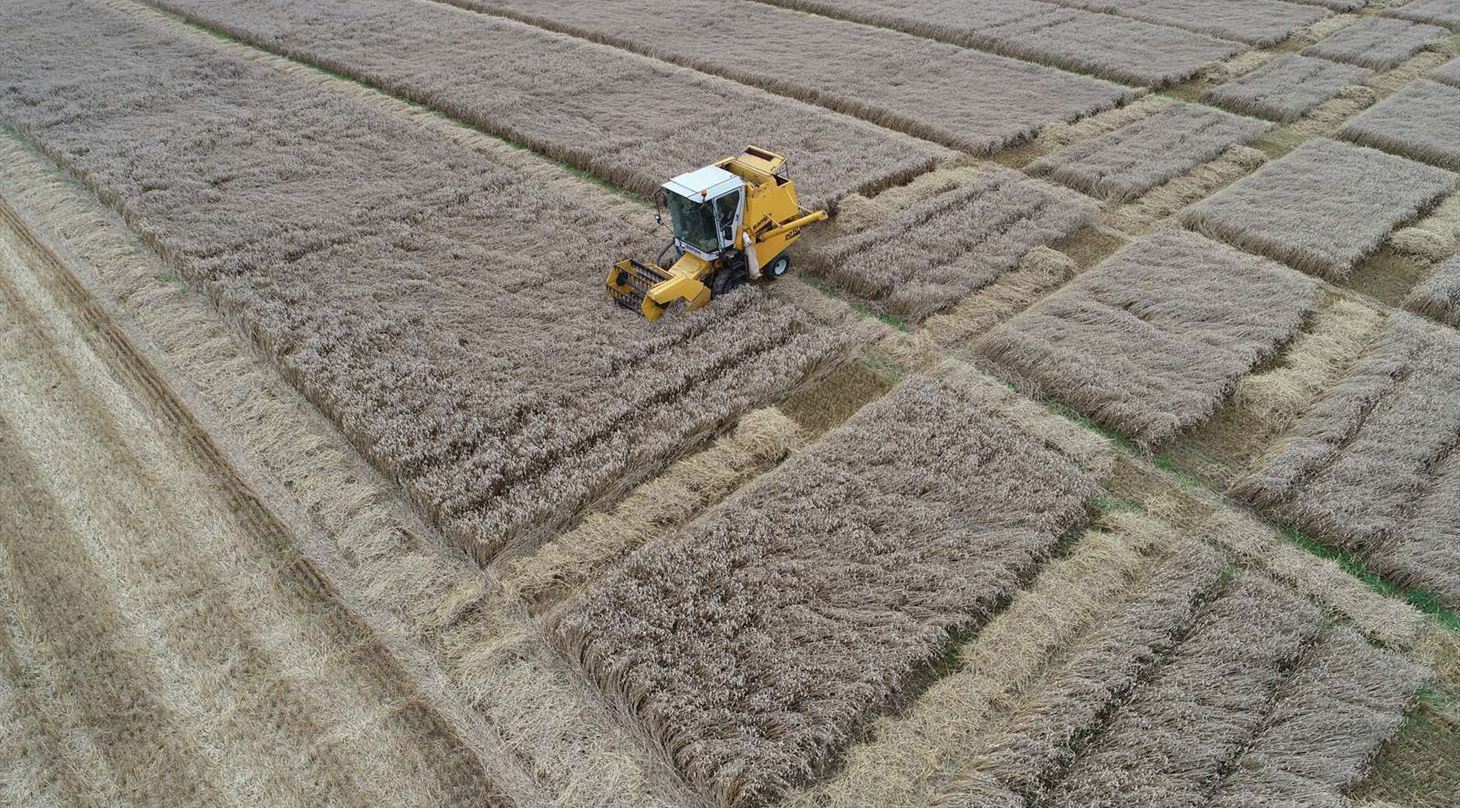
3D printing of racks for test vials led to huge savings
The Danish Technological Institute has specialists within many business areas, each of which produces impressive results. But when you take advantage of the synergies between the various skills, it can lead to even more benefits - both internally and for customers. One of the most recent examples was a collaboration between the specialists within 3D printing, field trials and food technology, which led to enormous savings and increased flexibility.
In the spring of 2022, the Danish Technological Institute's departments for field trials and food technology faced a challenge in a large project. As part of the project, they had to sample and analyse just over 30,000 nitrous oxide samples in the first year alone.
For this, they had invested in an analysis machine with a so-called autosampler, so that the analysis of the many samples could be automated as much as possible - both to save time but also to eliminate manual errors in the process. The process works by placing a series of vials in a rack, which is then inserted into the machine where the samples are taken.
- The autosampler came with two racks, each with 60 positions for vials. Obviously, this wasn’t enough to accommodate our sample volume, as we had to reach a minimum of 300 analyses a day, says Sune Petersen, consultant at the Danish Technological Institute.
Need for adaptation – and more room
The challenge was partly a need to have more racks but at the same time have room for more vials in the rack - and actually also some different sized vials than the existing ones, which then had to be arranged in a different way in the rack. BUT: The racks, which are originally made of aluminium, are extremely costly from the manufacturer, so it was simply too expensive to just order new ones.
I contacted the manufacturer and got a price of for 8 racks with room for 60 vials each, which was well above pour budget. Then I remembered a LinkedIn post from our colleagues in 3D printing, who had printed a really nice hand in titanium - and I thought that if they could make that, they could probably also make racks for us
- Sune Petersen, Danish Technological Institute
The wish was therefore to design a new rack that could be 3D printed in plastic, as there was no need for it to be aluminium - and at the same time there was a strong desire to reduce the price. Therefore, the specialists in Industrial 3D printing were contacted, and they created a design and the first prototype in just a few weeks. Subsequently, the design was adjusted slightly before the right solution was in place.
Lower price and greater flexibility
- The result was a design that could easily be adapted to the various test setups. The new plastic rack could be 3D-printed much cheaper, and at the same time it offered increased flexibility, as the design is easy to adapt, says consultant Sigurd Vigen Pedersen, who made the 3D-printed rack.
So far, 22 new racks have been printed, which have resulted in savings of 85 percent – and the new racks can be delivered within 10 days, even when it comes to new designs.
Thanks to the Danish Technological Institute's diverse competences, we now have a setup that is far superior in terms of both design and price compared to the 'off the shelf' product from the manufacturer
- Sune Petersen, Danish Technological Institute