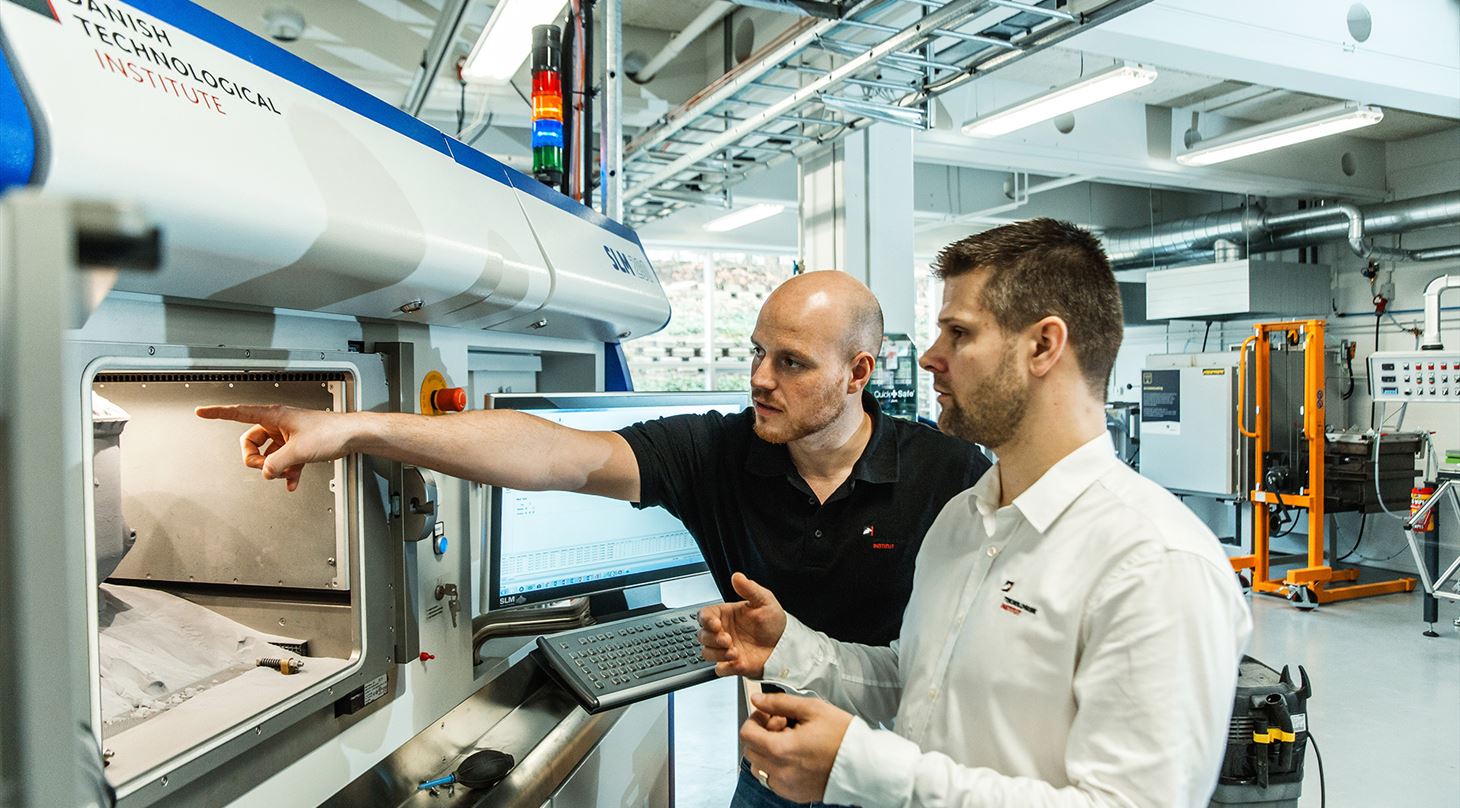
Shattering the myths about additive manufacturing in metal
The additive manufacturing industry is on the rise with an average annual growth of almost 25 percent over the past four years. Especially sales of industrial printers for metal are increasing, and last year, a survey from the Danish Technological Institute showed that 30 percent of Danish manufacturing companies expect to use additive manufacturing in metal – however, only 3 percent have actually started using the technology. We take a look at some of the myths that might stand in the way of an industrial additive manufacturing breakthrough in Denmark.
In Europe, industrial additive manufacturing has already taken off, and especially companies in the automotive and aerospace industry have long been aware of 3D printing in metal as a cost-effective production process for demanding applications. In Denmark, however, we are still trailing behind.
A small group of Danish companies has started 3D printing in metal, but there is still a long way to go before we reach the 30 percent of Danish manufacturing companies, who pointed to additive manufacturing as a technology that they expected to use in future production. The reasons could be many, but among the companies that see additive manufacturing as relevant, there are two barriers which are highlighted: price and quality. 27 percent of the respondents considered the price of additive manufacturing in metal to be too high, while 21 percent pointed out that the quality was not yet good enough.
A missing domino effect is of course another possible reason for Denmark lagging behind its neighbouring countries when it comes to additive manufacturing in metal. There are still very few metal printers in Denmark, and the Danish Technological Institute is the only one that offers production as a service or as a subcontractor.
- In Europe, the subcontractors have more printers, and furthermore Denmark does not have an automotive or aerospace industry to lead the way. But if we suddenly see more 3D-printers in the industry, designers and constructors will exploit the opportunity, and then the development will quickly take off, says Mads Østergaard, Team Manager in the Industrial 3D printing sectionat the Danish Technological Institute in Aarhus.
Dangerous to ignore the potential
Although additive manufacturing in metal has not yet obtained its industrial breakthrough in Denmark, it is indisputable that the potential is there – and that it exists in almost all industries and in both small and large companies. The advantages are well-known and include weight optimization, production flexibility, and the possibility of complex product designs, but compared to large industrial plants, additive manufacturing in metal is also a relatively cheap technology that can reduce the costs a company has when getting started.
If we look at the technological development, the perceived barriers to additive manufacturing in metal - the myths if you want - can be dangerous, as they risk overshadowing the potential. Prices are dropping rapidly, while the quality and the possibilities increase dramatically. So even if the reservations about price and quality may have been true last year, that is not necessarily the case year. Companies that the relevance of additive manufacturing should therefore keep an eye on the new opportunities - otherwise they risk being overtaken from within.
Below we try to break with some of the most widespread myths about additive manufacturing in metal, and the video will covre some of the myths as well (video only available in Danish)
Four myths about additive manufacturing in metal
- The price is too high
It's a widespread misunderstanding that the price of additive manufacturing in metal is very high. This used to be true, but as the technology has matured, the prices have dropped in recent years, so additively manufactured metal items today are far cheaper - and often competitive with traditional manufacturing. One reason is that materials have become cheaper, but the production time has also decreased as the printers have become faster and the print chambers bigger – hence, the stock price on the items will be lower.
When we consider the price, it is also important to keep in mind that it is far from all items that are suitable for additive manufacturing - neither from an economic or a functional perspective. It is important to evaluate the individual items and see if additive manufacturing can optimize them or add new features, such as lower weight or consolidation of multiple items into one. Here, design plays an important role, and one of the biggest changes in the field of additive manufacturing is the increased focus on design (DfAM or 'design for additive manufacturing). With this it is possible to utilize the benefits of the technology and add new or increased value – in other words, the total effect will be greater than the sum of the parts. According to Wohlers Report 2019, this tendency of increasingly focusing on the design is expected to have the greatest impact on the uptake of additive manufacturing in the industry. - The quality is not good enough and there is a lack of standards
Previously, there were some quality issues - particularly on 3D printed metal items. But a lot has happened with the quality over the past few years, and now it meets the demands of the industry. This is proved by the fact that we now see 3D printed items in the space and aerospace industry, where quality and safety requirements are extremely high. In addition, the density of additive manufacturing in metal today is up to 99.9%, thereby possessing the properties that you would expect from a ‘normal’ metal item.
At the same time, an increased focus has been placed on developing specific standards for additive manufacturing materials and processes. Hence, today there are several ways to certify the items to ensure that they meet the industry's requirements. 9 standards have been published for additive manufacturing so far, and 25 more are on their way – and 20 new suggestions for standards are in the pipeline. In the international standardization work, the focus is on e.g. the terminology of additive manufacturing, processes, materials, test methods, quality specifications, data, design, environment, and health and safety. By participating in the standardization work, Danish companies can influence the future market requirements, because the standardization work is still in its infancy.
- The standards will form the basis for the future market requirements for additive manufacturing across industries and disciplines. Therefore, Danish companies can get a lot out of participating when the standards are to be written, says Berit Aadal, senior consultant at Danish Standards and responsible for the Danish committee, which contributes to developing international additive manufacturing standards. - It's difficult to get started
It is true that it takes a bit of work to get started with additive manufacturing in metal, and it is not necessarily the right solution to just buy a printer and experiment, as can be the case with small FDM printers. You typically need some sparring and maybe a collaboration with companies or partners who have some knowledge in this field - and the employees need more knowledge and training to be able to make the right setup and efficiently run the activities. All things considered, lack of knowledge is probably the most pressing challenge when it comes to additive manufacturing in metal, but fortunately there is a solution. As more and more 3D printers are sold for industrial use, an increase in education programmes with a focus on additive manufacturing have arisen - both in Denmark and abroad. Simultaneously, there is a large number of course offers of shorter or longer duration - e.g. at the Danish Technological Institute - providing an introduction to technology, machines, design rules, business models, safety etc.
A good start is to invest in building knowledge, e.g. by teaching the employees to design for additive manufacturing and start thinking the technology into the business. The specific machines and materials are not so important to start with, and it might not even make sense for your company to plunge into metal 3D printing right now. But development is going fast, and maybe it will make sense in 3-5 years - and by then it is too late to start the knowledge acquisition. - There is limited access to machines
This is no longer correct. From the recently published Wohlers Report, we can see that 2,297 metal 3D printers were sold in 2018, equivalent to a 29.9 % increase from 2017. In other words, more metal printers are being sold than ever before and there are access to these from several suppliers worldwide - also in Denmark, where the Danish Technological Institute offers additive manufacturing in metal, including titanium, aluminium, stainless steel and tool steel.
But in fact, it may not initially make sense for companies to invest in the metal 3D printers themselves. Instead, the companies can start focusing on building the necessary competencies and start thinking in additive manufacturing – e.g. which items could benefit from being done in additive manufacturing, how could new items be designed to utilize the benefits of additive manufacturing, or how additive manufacturing can be applied in business processes. A good example of this approach is Danfoss, who in the AM-LINE 4.0 project collaborates with the Danish Technological Institute to identify relevant cases, discuss design, make prototypes in metal and build competencies until that point in the future when they can assess whether to take home the production and invest in metal 3D printers themselves, or whether they should continue with extended arm partners.
The technology has matured
In conclusion, it is important to repeat the point that additive manufacturing is not the answer to everything. We need to look at the individual items and products, and then assess whether it makes sense to 3D print from a manufacturing perspective, but certainly also from an economic perspective – however, if it does, additive manufacturing enables companies to offer more individual or flexible products.
Overall, we can at least conclude that additive manufacturing in metal has reached a turning point, where the development in materials, print speed, and print quality has created some processes that are ready for industrial production. In the rest of Europe, printing in metal is already accepted as a cost-effective production process for more demanding applications, and the assessment by the Danish Technological Institute is that the market in Denmark is also ready - so it's just a question of getting started.