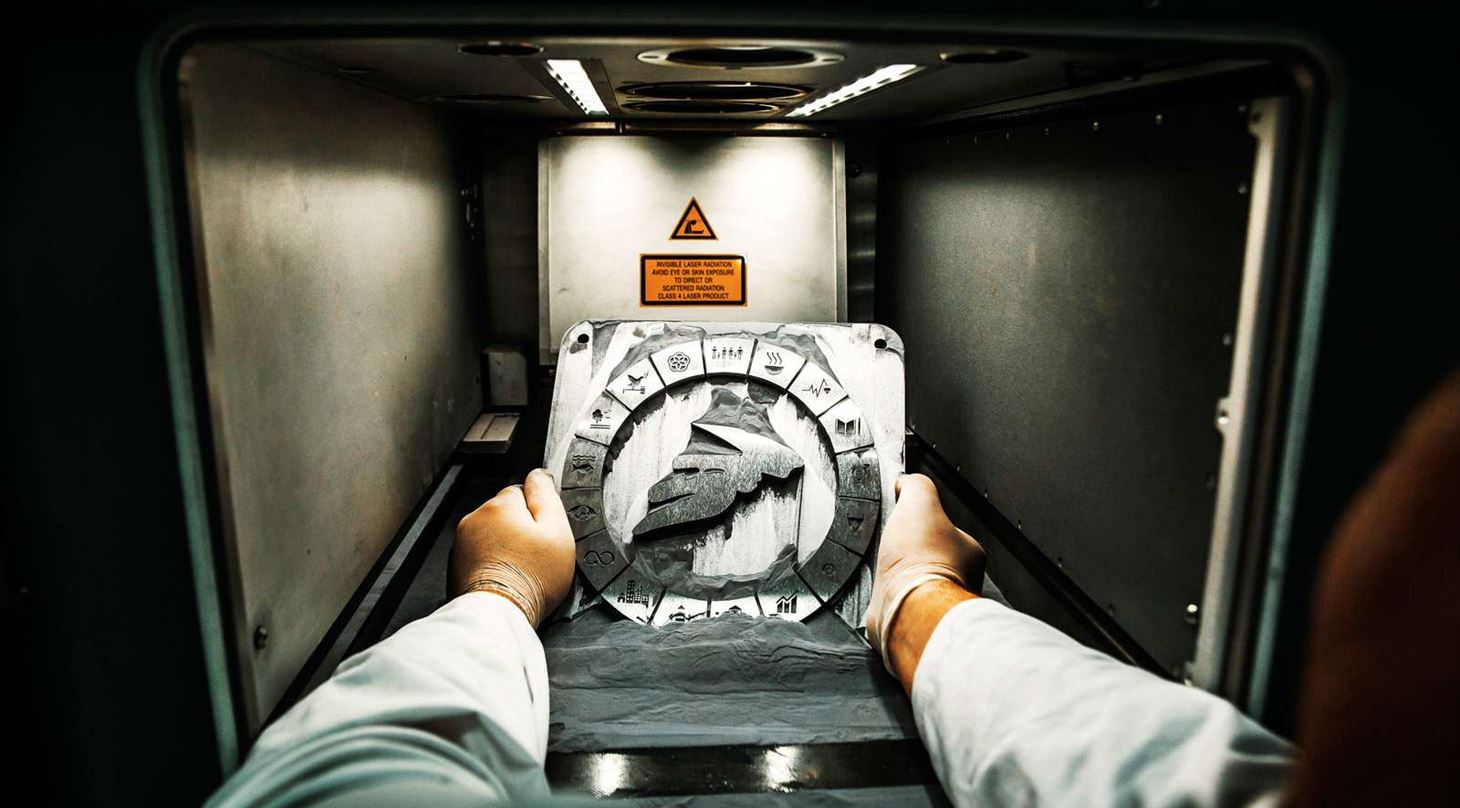
Recycled powder paves the way for more sustainability in the metal industry
A recently finished project shows that recycled titanium scrap can replace virgin raw materials and significantly reduce CO2 emissions. After three years of research and development, the Eureka-supported project VARETIT can now present promising results.
The purpose of the project has been to investigate the potential of recycling titanium chips - a by-product from the metal industry - for the production of titanium powder that can be used for 3D printing.
The project has demonstrated that we can turn waste into a valuable raw material. This opens up new opportunities for circular and energy-saving production methods within the metal industry
- Anders Hjermitslev, Danish Technological Institute
Significant Savings
The difference in environmental impact between traditional manufacturing and the VARETIT method is evident. The VARETIT method uses only 23% of the energy and 16% of the CO2 emissions required for traditional manufacturing.
- We see significant savings in both energy and carbon footprint, says Anders Bæk Hjermitslev, adding that the VARETIT project has focused on producing powder on a small scale, and that larger-scale production may yield different results, says team manager Anders Bæk Hjermitslev from the Danish Technological Institute.
While the recycled powder can be used for a wide range of applications, the quality is not as high as traditionally manufactured titanium powder.
- We knew that we would not be able to use it in medical applications or aircraft components, but the quality that we can print with the recycled powder has proven to be sufficient to meet the needs of many applications.
Scaling Up the Technology
- We have shown that the concept works. Now we need to look at how we can turn it into a product that the industry accepts, says Anders Bæk Hjermitslev.
This includes scaling up powder production from two kg to over 100 kg.
- In addition, the powder quality itself and the 3D printing process need to be further optimized before the industry will truly embrace the new recycled powder.
Although there is still potential for improvements, the VARETIT project, with its promising results, has paved the way towards a more sustainable metal production.
We are excited about the results and will now try to assemble a new consortium to seek support for a follow-up project. This should bring the recycled powder closer to becoming an integral part of mainstream production
- Anders Hjermitslev, Danish Technological Institute
The VARETIT project ran from June 1, 2021, to November 30, 2023. The project was a collaboration between the Danish Technological Institute, Euler3D, Bühler-Meincke, Ionics, CRM Group, Revatech, and Granutools.