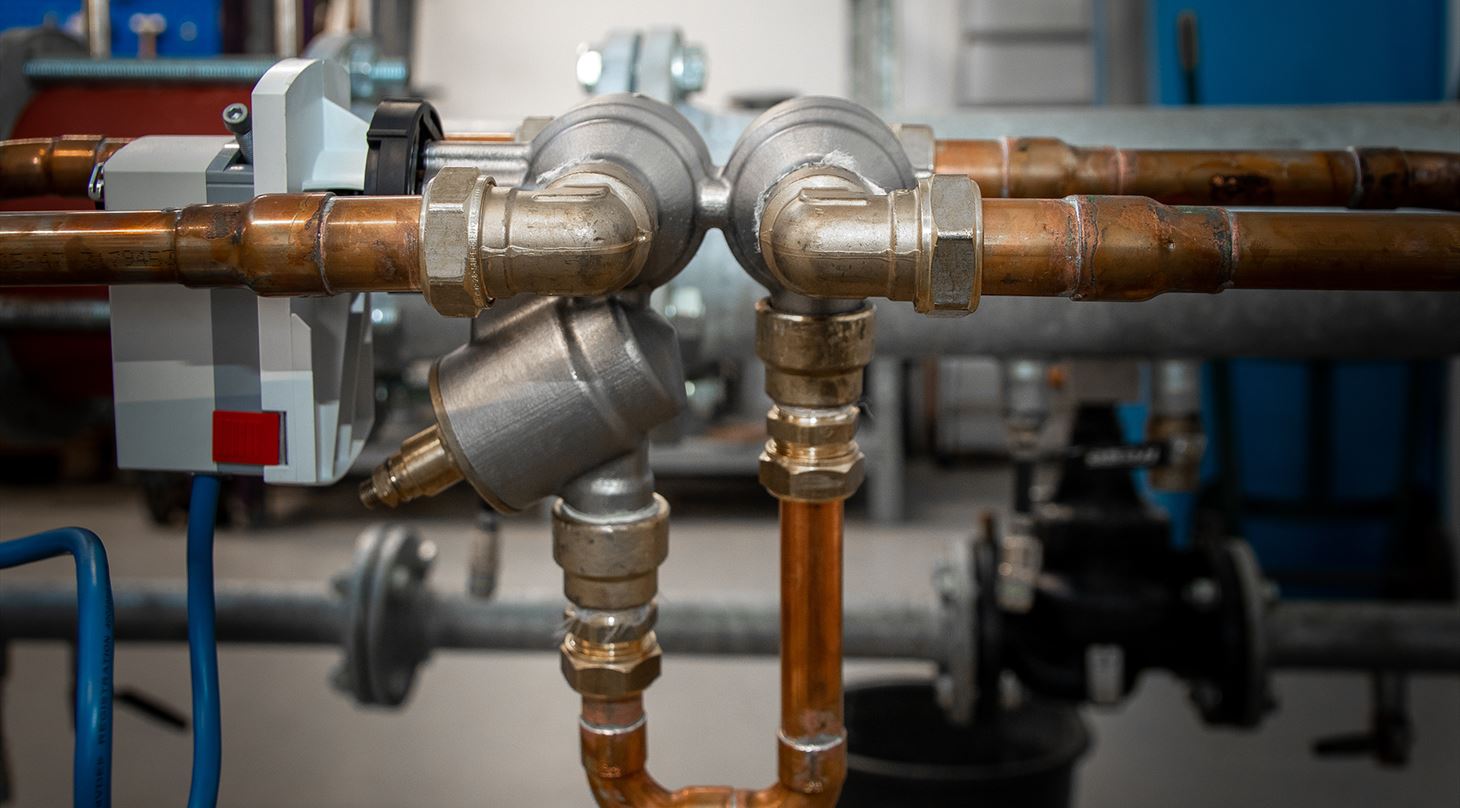
Frese develops special valve using metal 3D printing
The Danish company Frese is one of the world's leading manufacturers of innovative flow control and component solutions and has customers all over the world. Frese's development department focuses on valves and fittings for the HVAC market, and for the development of the world’s first dynamic 6-way valve, Frese decided to use metal 3D printing for the prototypes.
The valve that Frese developed was the world’s first dynamic 6-way valve that can 'feel', whether cold or hot water flows through it. The prototypes for the valve and the house in which it sits were 3D printed in two different sizes at the Danish Technological Institute, where the Center for Industrial 3D printing offers 3D printing in various metals - in this case stainless steel.
The finished valves are usually made of brass as it is a cheap material and because the valves are molded. But Frese is excited about using 3D printing as a prototype tool, and with metal 3D printing they have had the opportunity to develop the prototype with the correct properties and subsequently test it under pressure. In addition, 3D printing makes it possible to accelerate the development process itself, and this has meant that Frese could quickly develop and test a new design.
- It wasn’t possible for us to manufacture the prototypes like we use to, and therefore we were faced with having to start production without testing the design. By having the Danish Technological Institute 3D print stainless steel prototypes, we were able to save a lot of time and money by confirming the final design before we started the casting and heat-pressing tools. The prototypes were used to ensure that we had the right size, and we avoided having to make a full production of turning parts to clarify whether the dimensions met our functional requirements, says Jussi Svendsen of Engineering Research & Development at Frese.
In the video below, he tells more about the 3D print development and the collaboration with the Danish Technological Institute (video is in Danish). The case continues after the video.
Inner channels with 3D printing
During the design of the prototype, Frese has utilized another advantage of 3D printing, which is the possibility of making rounded interior channels.
Originally, the idea was that the channel should just be drilled straight through, but instead Frese made the prototype with a rounded channel inside. That way, they have the opportunity to test the rounded channel against one that is straight so they can assess how much better the rounded one is.
- Kristoffer Nielsen, Danish Technological Institute
Should the rounded channel prove significantly better, Frese will try to achieve some sort of rounding by drilling into the finished item several times. Although Frese would like the functionality of 3D printing, the valve is produced in such large numbers that it will not make sense to 3D print it, as it will be about a factor of 10 more expensive than molding, and the extra cost is difficult to get customers to pay. Therefore, the solution was to use 3D printing as a valuable tool in product development, and then mold the final product.
Development process offered new experiences
During the development work, Frese gained new experience with how to best work with metal 3D printing - and what challenges you may encounter. For example, there was a dent on the valve that Frese did not specify for post-machining, and that meant that there was a tolerance which was not ideal. Consequently, the lesson was that if a surface is important in terms of tolerances, machining supplements must always be applied to it. In addition, Frese wanted to make a channel larger in the 3D-printed prototype, and here they learned that it was extremely difficult to drill through, as stainless steel is a very hard material - here, the correct solution would therefore be to draw the channel a little larger in advance.
Going forward, Frese sees great potential in using metal 3D printing for similar development processes - but new opportunities have also been opened up on the plastic side. Thus, Frese has previously used 3D printing in resin to produce some couplings, but the couplings bursted because there was too much pressure when water flowed through. Conversely, 3D printing in nylon would be strong enough to handle the pressure, but here the challenge has previously been that nylon absorbs water - but with the new 3S treatment from the Danish Technological Institute, the surface is closed so that the nylon no longer absorbs water.