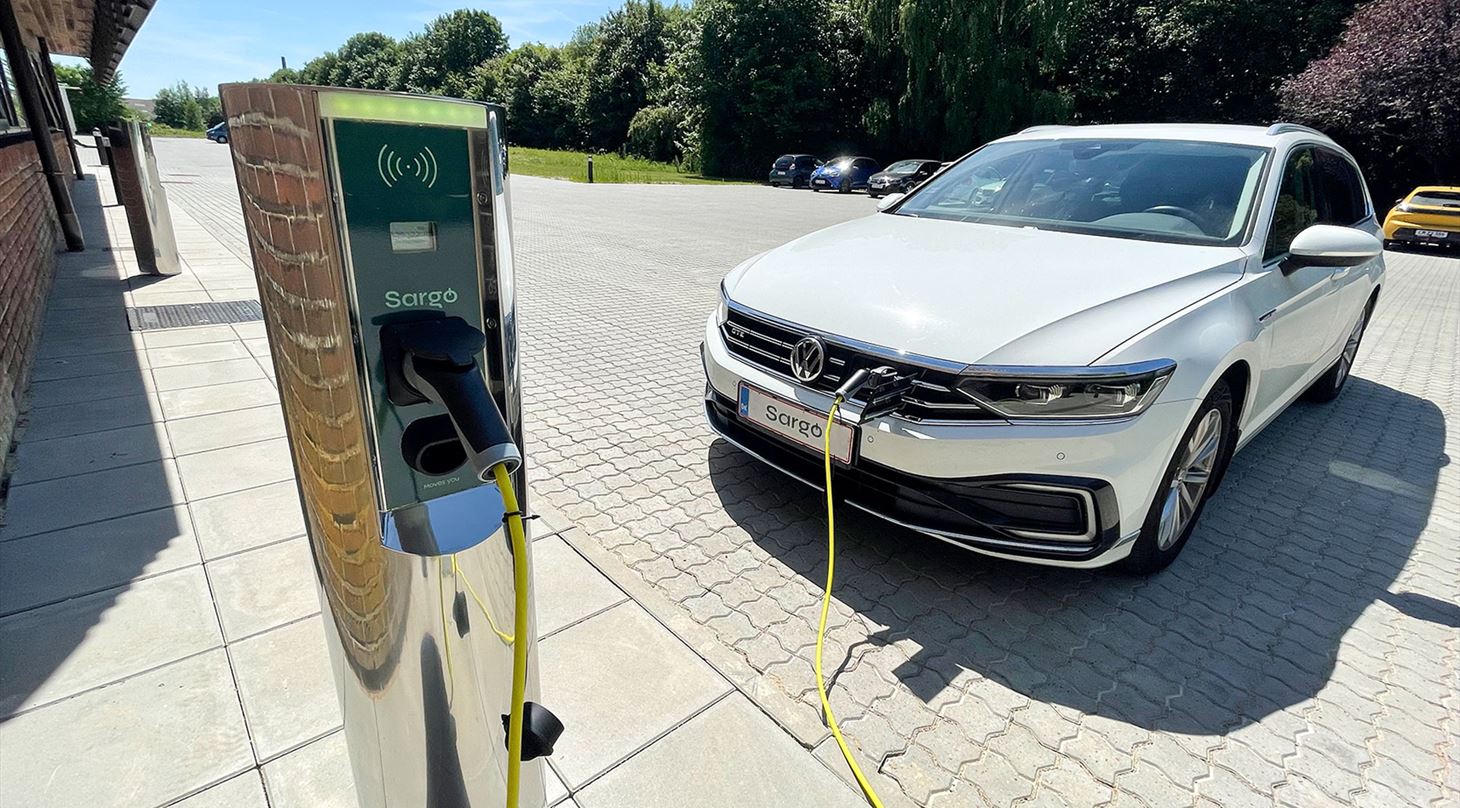
Hamag gets better products and easier manufacturing with 3D printing
The Danish company Hamag A/S develops and manufactures products and solutions that support all types of fuels – e.g. solutions for gas stations - and they have really adopted 3D printing.
Hamag has invested in an FDM 3D printer themselves, and they use it both for prototypes and tools, but also for actual production. Among other things, they print holders for electric car charging cables and components for card readers at the payment terminals, and here they especially take advantage of the great design freedom of the 3D printing technology.
- With 3D printing, we can build in functions such as gaskets, so we get a better product, which is also easier to manufacture than before, says Jens Ejnar Pedersen, Production Technician at Hamag.
Because they can design the components themselves, Hamag can easily come up with a solution - and it is much cheaper than if they had to make an expensive tool and have the parts injection moulded.
In addition, there is great production flexibility. If, for example, it is only a few parts, Hamag prints them themselves, and if there are large numbers, they order from the Danish Technological Institute, where the industrial 3D printers are much faster. For instance, the Danish Technological Institute could print and deliver 100 charging plug holders in 10 days, while it would take Hamag 70 days to print them themselves.
With 3D printing, we can build in functions such as packages, so we get a better product, which is also easier to manufacture than before
- Jens Ejnar Pedersen, Hamag
In the video below, Jens Ejnar Pedersen talks more about Hamags use of 3D printing - and about thew collaboration with Danish Technological Institute.
Benefits of 3D printing in this case
- Possibility of meeting special requirements thanks to ultimate design freedom and the ability to redesign without large tool costs
- By incorporating functions in the parts, such as gaskets or threads for screws, you get a better product, which is also easier to manufacture
- Avoid large inventory as only the 3D files need to be in stock. The parts are produced as needed - either on their own printer or at the Danish Technological Institute with a short delivery time
- Opportunity to quickly get from idea to physical product, and Hamag can design and manufacture the components themselves.
- Cheaper than injection moulding, as the number of parts is low