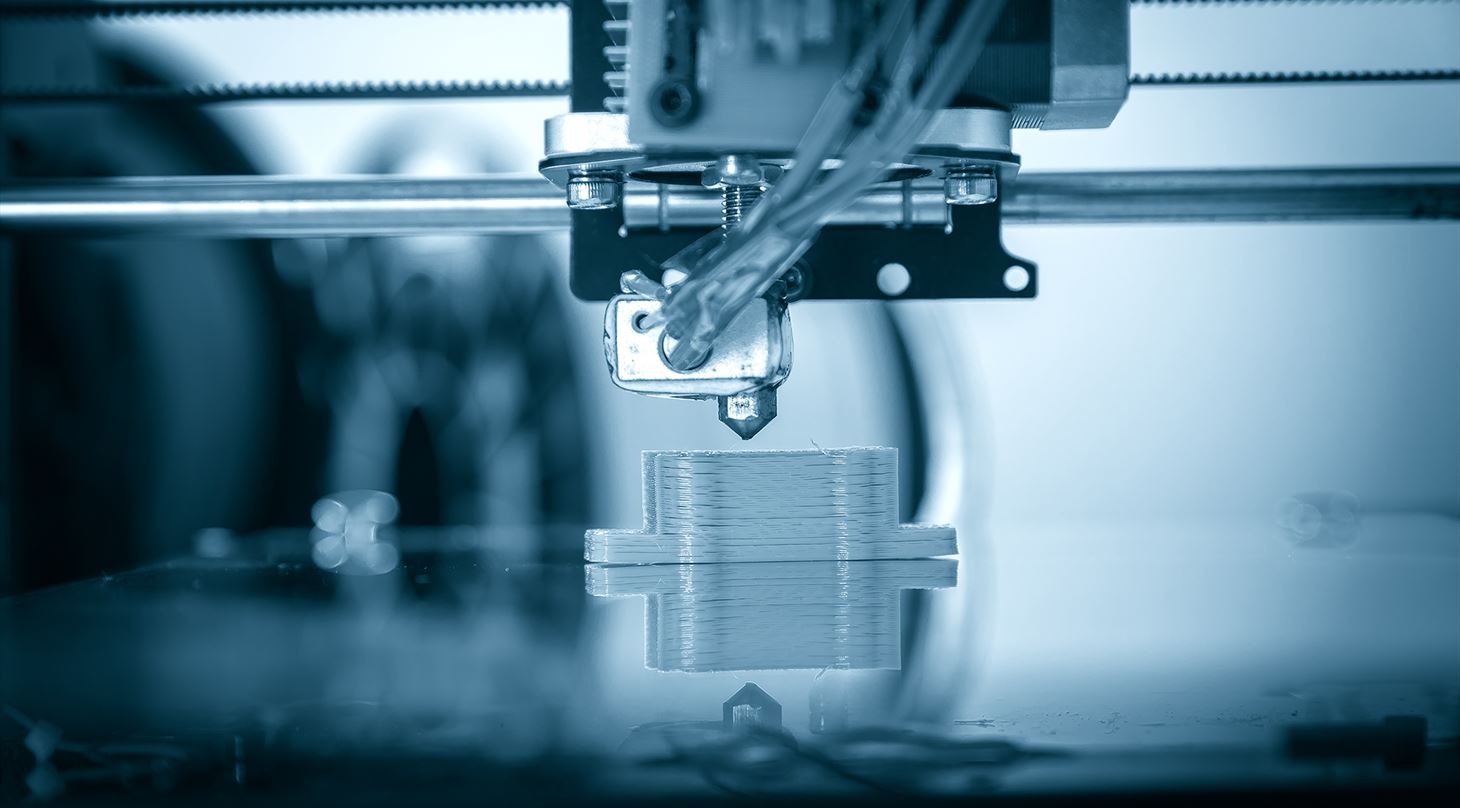
3D printing with Fused Deposition Modeling can optimize development processes
Fused Deposition Modeling - or FDM - is currently the most widely used 3D printing technology, and it offers various options for material selection, just as it is an obvious choice for production companies that want to optimize the development process.
With Fused Deposition Modeling, a material in the form of filament, i.e. a spool of wire, is heated and pressed through a movable nozzle that applies the material on the print platform, where the layers are partially fused together in a layer-on-layer method.
The construction of the machine itself means that printing can take place in both open and closed systems, depending on the material you are printing with and how much control you want to have over the temperature in the printing process.
Online course in Fused Deposition Modeling
- If it is a closed system, it simply means that there is a box around the machine, which can make it easier to control the temperature and at the same time reduce noise, says Kristoffer Ryelund Nielsen, business manager at the Danish Technological Institute.
An (even) larger catalogue of materials
When it comes to materials, Fused Deposition Modeling has an extra feature: The technology makes it possible to make composite materials where other materials are mixed into the plastic, such as carbon fibre, fiberglass, wood, or metals. The ability to make composite materials is an advantage of the technology because it enables parts with new and unique properties and expressions.
Usually you print in plastic with Fused Deposition Modeling, but it is also possible to mix metal in the plastic, after which the plastic can be burned away in an oven after printing, and then you are left with a metal part. So in that way, it is actually also possible to print in metal with this technology
- Kristoffer Ryelund Nielsen, Danish Technological Institute
The technology is also paving the way for new composite materials. For instance, you can use a printer from Markforged to print with continuous carbon fibre threads inside plastic parts, which gives an incredibly strong part - in fact as strong as aluminium.
The weakness is in the surface
Despite the fact that there are several benefits to using Fused Deposition Modeling, you still need to take some precautions before embarking on the technology. Although some printers give strong parts, as just mentioned, the weakness of the parts is a general weakness of Fused Deposition Modeling - this is because the parts are often anisotropic.
- When a part is anisotropic, it means that it is not equally strong in all directions. For example, parts printed with Fused Deposition Modeling are stronger in the X and Y direction than they are in the Z direction, which is the vertical direction across the layers, says Kristoffer Ryelund Nielsen.
In addition to the weaknesses of the parts, it is worth paying attention to their surfaces: If you desire smooth and neat surfaces, it is usually necessary to post process your parts with either acetone or sanding. For the same reason, the technology is not suitable for the medico or food industry, where there are strict requirements for surface tolerances, and where it is extra important that the surfaces are easy to clean, as they must be cleaned frequently.
You can print as big as you want
While there may be weaknesses in the technology, it also has some very special features, one of which is the size of the parts. Today, the largest pre-produced printers are about 1 x 1 meter in size - but if you can build a scaffolding, there are no restrictions on the size of the printer.
- For example, the University of Maine has printed an entire boat with Fused Deposition Modeling. If you can build a giant scaffolding where there is a print head that can move around, you can print as big as you want. And by depositing concrete rather than plastic, you can also 3D-print houses, as we see at the Danish company COBOD international A / S, says Kristoffer Ryelund Nielsen.
Fast prototypes streamline the development process
One place where Fused Deposition Modeling is particularly suitable is in the development process of manufacturing companies, because the technology opens up for rapid production of 3D-printed prototypes.
- Companies can save time in the process because you can quickly test a concept and correct it before ordering the final components from a subcontractor. In this way, you will save money and time by detecting any errors early in the process, says Kristoffer Ryelund Nielsen.
Typically, you want to start a print in the afternoon, and then it is ready the next morning when you show up for work. In this way, you can make quick iterations and thereby get to market quickly with your product
- Kristoffer Ryelund Nielsen, Danish Technological Institute
Although Fused Deposition Modeling is an obvious choice in the development process, the technology is not suitable for printing higher numbers. Here, powder-based 3D printing technologies such as Selective Laser Sintering (SLS) will be faster and often cheaper to print with.
It is not far from a finished product
A final benefit that is worth having in mind if you are considering embarking on the Fused Deposition Modeling journey, is that it is not far from the 3D-printed prototype until you are done with the finished product.
- If you intend to 3D print in metal, the leap from Fused Deposition Modeling is not as far as you might think. Many of the design rules are the same, so if a part is optimized to be printed without difficulty on an FDM printer, there’s a high probability that it will also be unproblematic printing on a metal printer, Kristoffer Ryelund Nielsen concludes.
In addition, the FDM technology has a very user-friendly application because the machines are easy to manage which makes the technology easy and straightforward to get started with.
Read about the other AM technologies
Interested in Fused Deposition Modeling?
If you as a company are interested in trying out the technology, the Danish Technological Institute offers online courses that provide an in-depth introduction to Fused Deposition Modeling as well as the rest of the 3D printing technologies. In addition, the Danish AM Hub offers to lend out FDM printers for free to companies that are interested in trying out the technology.