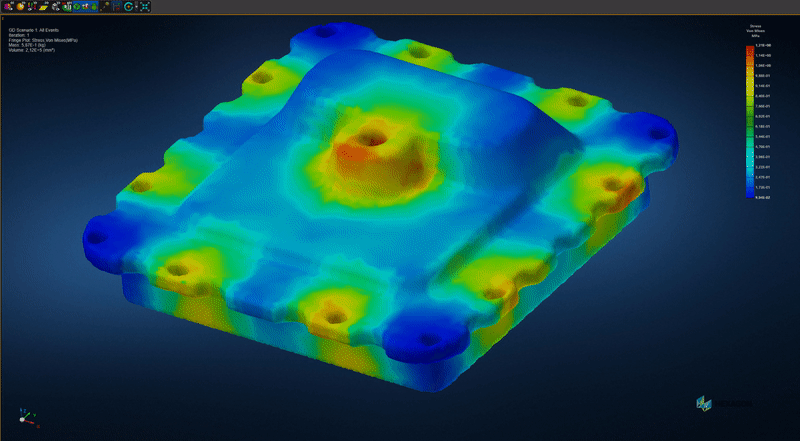
BEWI achieved a lower price, shorter delivery time and increased efficiency with 3D printing
BEWI produces polystyrene and they have been curious about 3D printing. But when they were offered a 3D printing design course in collaboration with the Danish Technological Institute and Danish AM Hub, they did not know that the results would prove to have huge potential for BEWI's future components. But with 3D printing, you can actually reduce both the weight, price, and delivery time of some of the tools used in the process - and they appear to be more efficient.
BEWI is a plastics company that produces polystyrene - what we in Denmark know as Flamingo® - in customized solutions. When the complex geometries in Flamingo® cannot be produced in a traditional way, it requires a casting tool that can cast complex shapes and designs based on the customers' specifications. The casting process itself requires moulds with good heat conducting properties that must be able to quickly cool down and heat up again.
Therefore, BEWI was interested in investigating whether it was possible to make the cycle more efficient by using 3D-printed aluminium moulds, where rapid cooling and heating is essential to potentially increase capacity with the least possible energy consumption.
With help from the Danish Technological Institute, they looked at this in a 3D printing design optimization course, where they optimized one of the tools that is part of the casting process. The goal was to get a printed solution that can contribute with flexibility.
In the video below, development manager Ole Krebs from BEWI talks about the design process and the potential of 3D printing technology.
An efficient production is a crucial parameter
An obvious place to take a critical look a BEWI's moulds was in terms of weight reduction. Here, 3D printing's design freedom has become a decisive element in achieving BEWI's desire for more efficient production.
The mission was a complete success. In the process, which was initiated by Danish AM-Hub, the design of the tool was optimized, and in doing so the weight was reduced by 74 percent compared to traditional tools, but time-to-market was also improved by having cut 25 percent of the delivery time.
- BEWI's current moulds are milled from aluminium and consist of three parts. They are subsequently assembled and have a weight of 550 grams. The challenge with these moulds is that they are expensive to manufacture and at the same time they have difficulty emitting heat. In addition, the milled moulds are complex to make, and therefore BEWI often encounters limitations when it comes to design, says Morten Lisberg Jørgensen, consultant at the Danish Technological Institute.
Improved freedom of design
During the project, it made sense to take a closer look at the possibilities of improving the design with topology optimization, where you get a computer to calculate the most ideal design based on a number of parameters that you specify in advance. A well-known fact is that 3D printing has a high degree of design freedom, as you don’t have the same limitations in the manufacturing itself, and in the project, BEWI had the opportunity to collaborate with the company Hexagon, who are experts in topology optimization – this revealed enormous potential for BEWI.
It gives enormous flexibility, and it is a potential where, by optimizing the tool, we can offer more complex and better solutions in terms of both quality and economy and thus meet the challenges that our machine settings cannot help us with. Furthermore, we see signs that the optimized component can increase our production capacity and lower energy consumption in production if we implement it fully – simply because it is more efficient
- Ole Krebs, BEWI
From 6 weeks to 10 working days - and 74% weight reduction
With the design freedom of 3D printing, BEWI has been able to determine the geometry themselves, which they were otherwise limited by before. The moulds are printed in aluminium, which is a material BEWI is used to working with. During the course of the project, they succeeded in reducing the weight of the mould by 74 percent just by optimizing the design. The weight of the component has gone from 550 grams to 145 grams. This is absolutely essential because it means significantly less material consumption. In addition, by using 3D printing, BEWI also saves a lot on the delivery time of the moulds: The delivery time of the milled moulds is 4-6 weeks, whereas the 3D printed mould has a delivery time of only 10 days.
The reduced delivery time is of great value to BEWI. This means that they do not have to pause their production for a very long time and they can quickly get started on new projects. In addition to design freedom, they also get more freedom in production to quickly test new ideas
- Morten Lisberg Jørgensen, Danish Technological Institute
Hopefully the future offers more 3D printing
Another advantage of the 3D-printed moulds is that BEWI cuts the price in half, and this is e.g. due to the reduced mass. The project concluded with a physical test of the 3D printed moulds to verify their longevity, and the test showed positive results. Compared to previous projects, the big difference has been that BEWI has obtained some results in the project that they can go out and use tomorrow.
- We can create a solution for the customer that provides a greater financial gain for them because we can exempt them from some costs. It could be, for example, a faster assembly time and being more efficient in several areas. And that is probably the big driver for us to stay in a market that is developing rapidly: That we can offer something extra and still be competitive, Ole Krebs concludes.
About the DfAM course
During 2022, Danish AM Hub, in collaboration with the partners Danish Technological Institute, PLM Group, Hexagon and Wikifactory, has taken 15 Danish SMEs through a new innovation course with the aim of strengthening the companies to benefit even more from the technological and business potential within 3D printing. The course is called Design for Additive Manufacturing (or DfAM) and focuses on rolling out 3D printing to small and medium-sized companies as well as providing concrete support and help to work with the technology through design. The specific aim of the DfAM course is to re-design the participants' products or components, thus enabling these to be produced e.g. with greater strength, less material waste, new and better functionality, and on-demand.