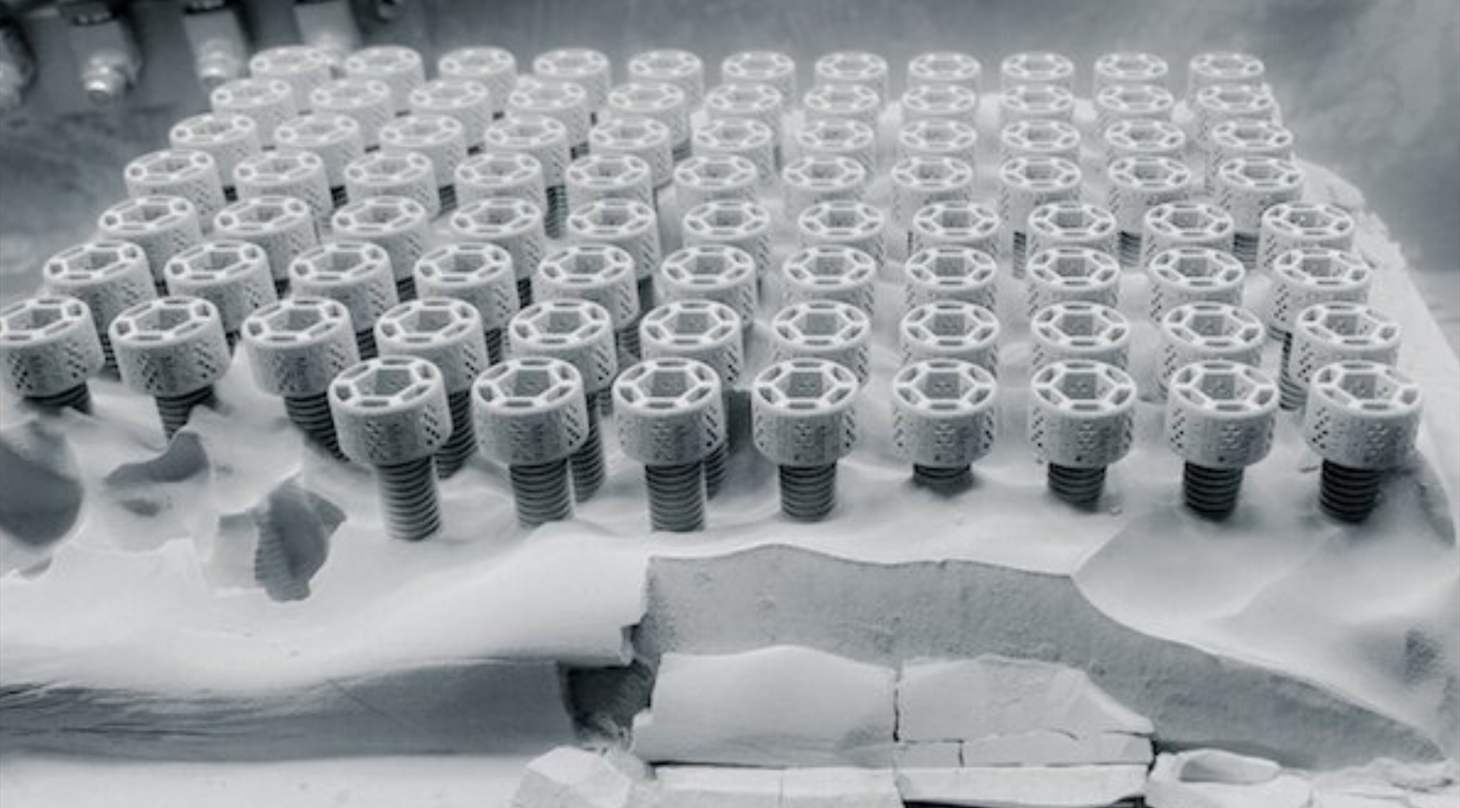
Metal Binder Jetting can benefit companies with high volume productions
One of the newer 3D printing technologies is Metal Binder Jetting, and with its scalability it can become a profitable and efficient solution for companies with high volume productions.
The Metal Binder Jetting and Laser Powder Bed Fusion technologies are similar in many ways since they are both powder-based technologies. The difference is that Metal Binder Jetting does not use a laser or an electron beam to melt the metal particles together in the printing process. Instead, the metal particles are glued together via a printhead.
Try an online course about Binder Jetting
- When Binder Jetting starts with 'binder', it specifically means glue that binds the metal particles together. ‘Jetting’ then refers to how the layers are a form of liquid or gas that is placed in a layer-on-layer method from a nozzle, says Anders Bæk Hjermitslev, project manager at the Danish Technological Institute.
Three process steps lead to the finished product
Before you have the finished print, Metal Binder Jetting requires you to go through three process steps: The first step is a 'green part', where the glued print is finished. The next step is a ‘brown part’ where the binder is burned away from the print. Finally, in the sintering process the print is heated to close to the melting point, whereupon the metal powder is sintered together in the places where the binder has been sitting. After the three process steps, you have the option of post processing the print.
An obvious choice for high volume productions
Since Metal Binder Jetting is a print head technology, it also means that the part you’re printing is not melted in the printing process. As such, it is not necessary to take cooling time into account. This results in a shortened production time, which in turn contributes to a more profitable and efficient production.
- Several companies have a great interest in scalability, where Metal Binder Jetting is well suited for parts with high volume – i.e. where you need to produce a really high number of parts. If, for example, a company needs to put printed a metal component into their product, and they make 10,000 products a day, then Metal Binder Jetting will be an obvious choice for that, says Anders Bæk Hjermitslev.
The video below shows the printing process for Binder Jetting.
Possibility of printing with new materials
Another value of Metal Binder Jetting is that the technology makes it possible to print with materials that are not otherwise suitable for laser printing.
- With Laser Powder Bed Fusion, it can be difficult to print with pure copper. The reason for this is that copper has a high reflection, which means that a large part of the energy in the laser will be reflected back, and therefore it can be difficult to melt the copper. In addition, a material such as tungsten is very hard, so if you print with a laser, there may be a risk of cracks in the part. With Metal Binder Jetting, you get around those two problems because you work under different premises, says Anders Bæk Hjermitslev.
READ MORE ABOUT LASER POWDER BED FUSION HERE
Best suited for printing smaller components
One of the areas where Metal Binder Jetting is challenged is the size of the parts. Metal Binder Jetting is best suited for parts that are not much larger than 5 x 5 cm, as there is otherwise a risk that the cooling after the sintering process will cause deformations. Although printing without a support structure provides great design freedom, it can be a challenge to ensure geometric tolerances after the sintering process if the print exceeds the recommended size or if the geometry has overhangs. However, printing of smaller parts provides an increased level of detail as well as finer geometry, as it is not limited by the laser’s melt pool.
Let us help you with AM production
Openness to technical development is absolutely critical
Since Metal Binder Jetting is one of the newer technologies in 3D printing, it has not yet gained a foothold in the industry. In order for the technology to succeed, Anders Bæk Hjermitslev emphasizes that companies' openness to technical development is absolutely critical.
I think it's basically about companies daring to use and implement the technology - because it already works. At present, companies may have a hard time seeing the possibilities of Metal Binder Jetting because they do not know the technology. And, of course, there is still a technical barrier, because it also requires time and resources to get Metal Binder Jetting up and running
- Anders Bæk Hjermitslev, Danish Technological Institute
Danfoss has been looking at Binder Jetting for a long time and gained experience with the technology. Here, they also see the potential, but they are equally aware that there are still some challenges.
- I believe Binder Jetting will play a niche role in Additive Manufacturing in the future – the size of that niche depends largely on technical and commercial developments in the coming years. The benefits include lower material costs and material variety, different surface properties, and possibly faster building time – that all contributes to a lower price per part. However, the challenges lie e.g. in designing for each individual process - both printer, de-binder and sinter oven – achieving high material density consistently, and making part sizes larger than a fist. It sounds simple, but in practice it is very complicated, says Werner Stapela, Global Head of Additive Design & Manufacturing at Danfoss.
Read about the other AM technologies
Danish Technological Institute can offer companies an insight into Metal Binder Jetting
If your company is interested in learning more about Metal Binder Jetting, the Danish Technological Institute has insight into the processes and contact with partners using the technology, and we are involved in several different projects that investigate Metal Binder Jetting. Therefore, we can help you price and design parts as well as help get them into production. If you are interested in implementing Metal Binder Jetting in your own production, we also have insight into the implementation and transition phase.