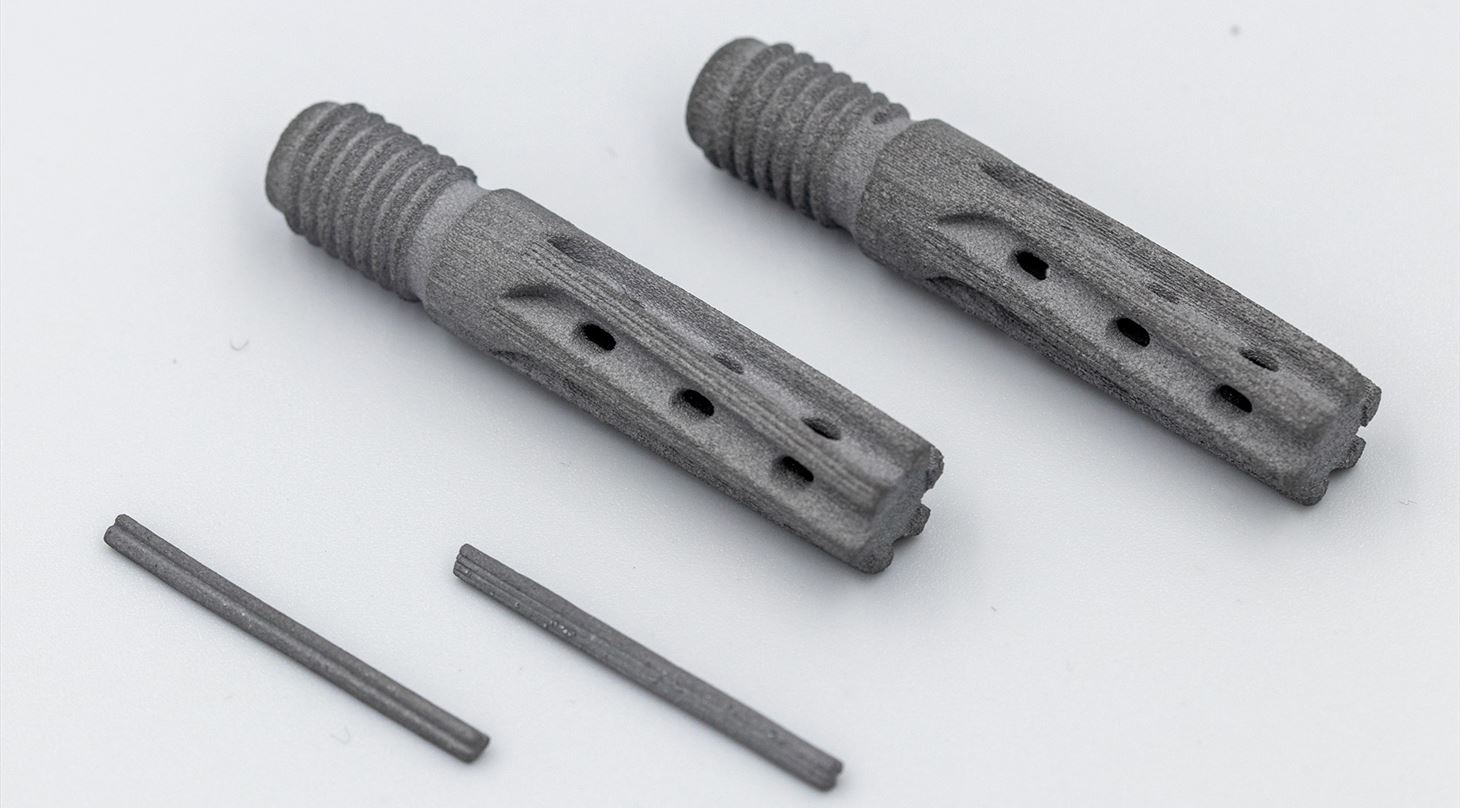
3D printing increases durability of mortar rake - and shows sustainability potential
Norse is a Danish company that produces cutting tools and protective equipment for a wide range of industries - for the development of a new tool, they had help from the 3D printing specialists at the Danish Technological Institute.
Among other cutting tools, Norse produces wall joint cutters, a tool used to scrape out the joints in brickwork. However, the mortar rake – the unit that is in contact with the joints – is easily worn down and thus calls for frequent replacement.
With the vision of a mortar rake that is more durable and sustainable, Norse decided to take part in the design optimizing course DfAM Green (Design for Additive Manufacturing), which is initiated by Danish AM Hub. The team linked up with the Danish Technological Institute (DTI) to take advantage of their expertise within 3D printing.
Rethinking material and form
Many changes have been made to the original component. Initially, the specialists at DTI decided on using different materials for the new unit. They selected a mix between tungsten carbide and 440C steel. Both materials have high hardness and high heat resistance.
The 3D printing format allows us to play with the geometry of the unit in ways that wouldn’t be possible in traditional manufacturing
- Morten Clemmensen, Norse
The shape of the unit has also changed. It has evolved from having 1 to 4 so called teeth. It also has a hollow inside, which allows for easier cooldown and less material used in production. The blades – the parts that do the actual cutting – have been slightly rotated in order to remove excess material more easily.
A durable and sustainable design
Having undergone the re-design process, the new unit has a 29% lower volume in terms of material used. It has a new, improved, more effective shape for better cooling and moving material off the blades. These changes essentially mean that the unit will last longer.
- Through this project we have gained new knowledge. We have produced a part, tried it out and concluded that is in fact very durable. The blades, however, need sharpening before the unit is fully usable in industry. So, the next step is to find a solution where we can make the blades even sharper and hold on to the newfound durability and material savings, says Morten Clemmensen, project manager at Norse.
About DfAM Green
Over a six-month period, Danish AM Hub - in collaboration with DTI, Hexagon, and Implement Consulting Group - has had four Danish SMEs engaged in an innovation course aimed at equipping the companies to take advantage of the sustainable, technological, and business potential within 3D printing to an even greater extent. The course has been named Design for Additive Manufacturing Green (or DfAM Green), and it focuses on spreading 3D printing to small and medium-sized enterprises, as well as providing concrete support and assistance in working with the technology through design.
The specific goal of the DfAM course is to redesign the SMEs’ products or components to make them more sustainable and, at the same time, capable of being manufactured with e.g. greater strength, less material waste, new and improved functionality, or on-demand.