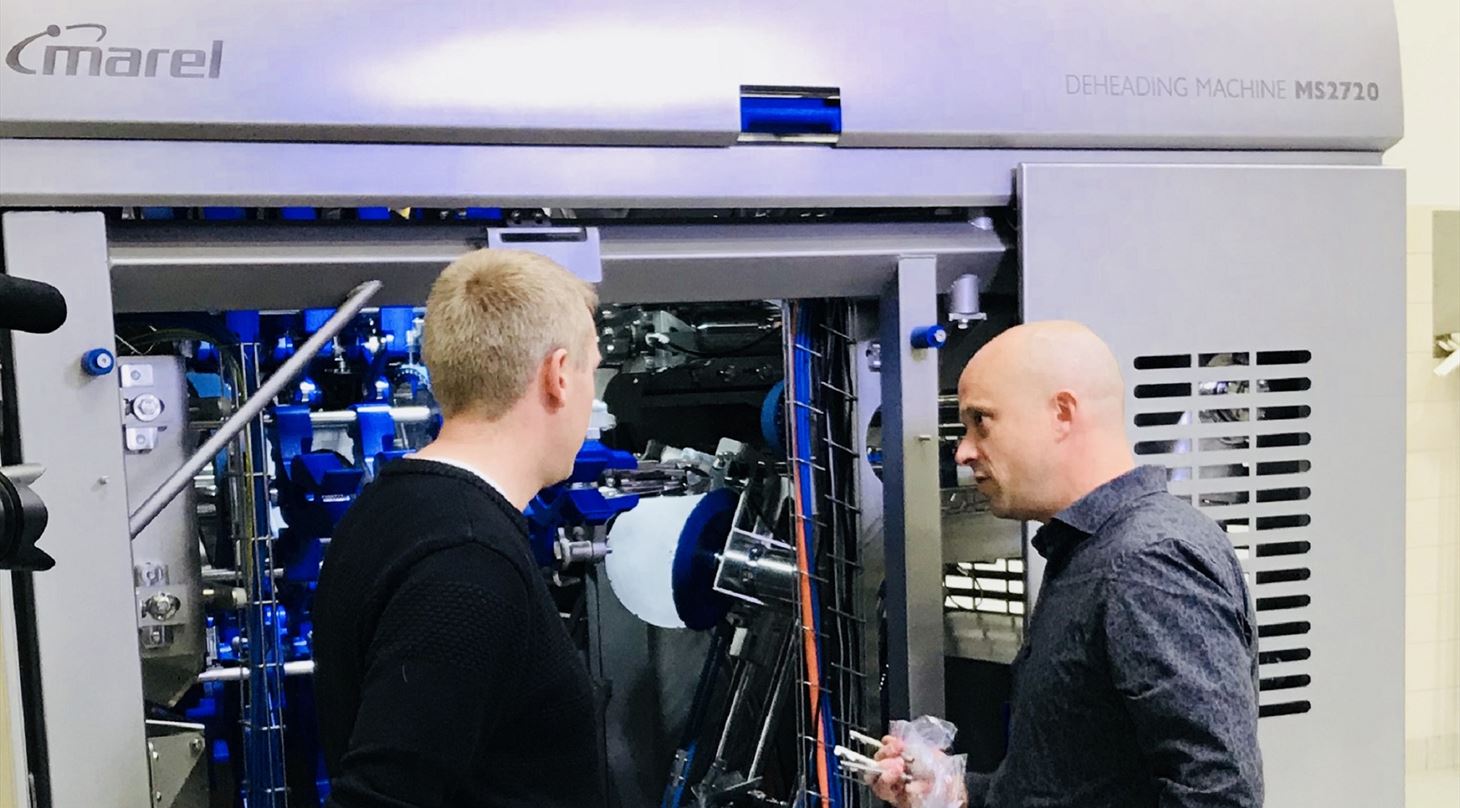
3D printing was the solution to the salmon gripper challenge
Marel had reached a dead end in the development process of a salmon gripper, and therefore they decided to test the 3D printing technology to solve the problem. Today, they produce titanium salmon grippers with 3D printing at the Danish Technological Institute. It gives them great freedom of design and a short response time.
The Marel Salmon Division makes equipment and process solutions for the salmon industry, and it is a world leader. During the development of a salmon gripper for the company's latest product, a salmon de-header, they ran into challenges.
- When we had designed the component, it turned out that it would be almost impossible to manufacture using traditional machining. So, we started looking at 3D printing to get moving and to achieve the design we wanted, says Peter Thisted Svoldgaard, mechanical designer at Marel.
This proved to be the right solution for Marel, as the 3D printing technology offers great freedom of design, short response time in the development process, and the opportunity to work with new types of materials. It ultimately gave them the opportunity to produce the salmon gripper with the properties they wanted.
- With 3D printing technology it is easy to change the geometry and get a new item printed with a short response time. It gives us complete freedom of design, since you do not have to think about leaving room for a cutter, or whether the item should be rigid enough so that it does not vibrate during milling. This means that you can think more out of the box and think in 3D printing, Peter Thisted Svoldgaard explains.
Titanium was the winner on material properties
Titanium proved to be the ideal material for the 3D-printed salmon gripper.
- We have gained more knowledge about titanium, which is a brittle material that fits well into our machine, since the salmon gripper will crack instead of bend if we have something crashing inside the machine. If something bends, we don't know where things are, so to avoid collision in the machine's robot, we would rather have things break, Peter Thisted Svoldgaard explains.
The Danish Technological Institute's role in the process has been as an advisor on the 3D printing technology as well as a producer of the salmon gripper.
- 3D printing has several advantages over conventional machining. It often makes sense if you need to be able to make relatively small series at a reasonable price in a very agile development process. Thus, it will be possible to continue to change the design very far in the process, says Thor Bramsen, senior consultant at the Danish Technological Institute.
3D printed items are food approved
A challenge in the production of the salmon gripper was the requirement to obtain food approval on the items, as this is not something that has previously existed on 3D printed items.
- We have worked to ensure traceability throughout the production, and we have succeeded so the material for the production of the salmon gripper is food approved. This opens up new opportunities for the food industry in general, Thor Bramsen concludes.
Read more about food approval of 3D-printed items here
Watch the movie about the salmon gripper here (only in Danish).