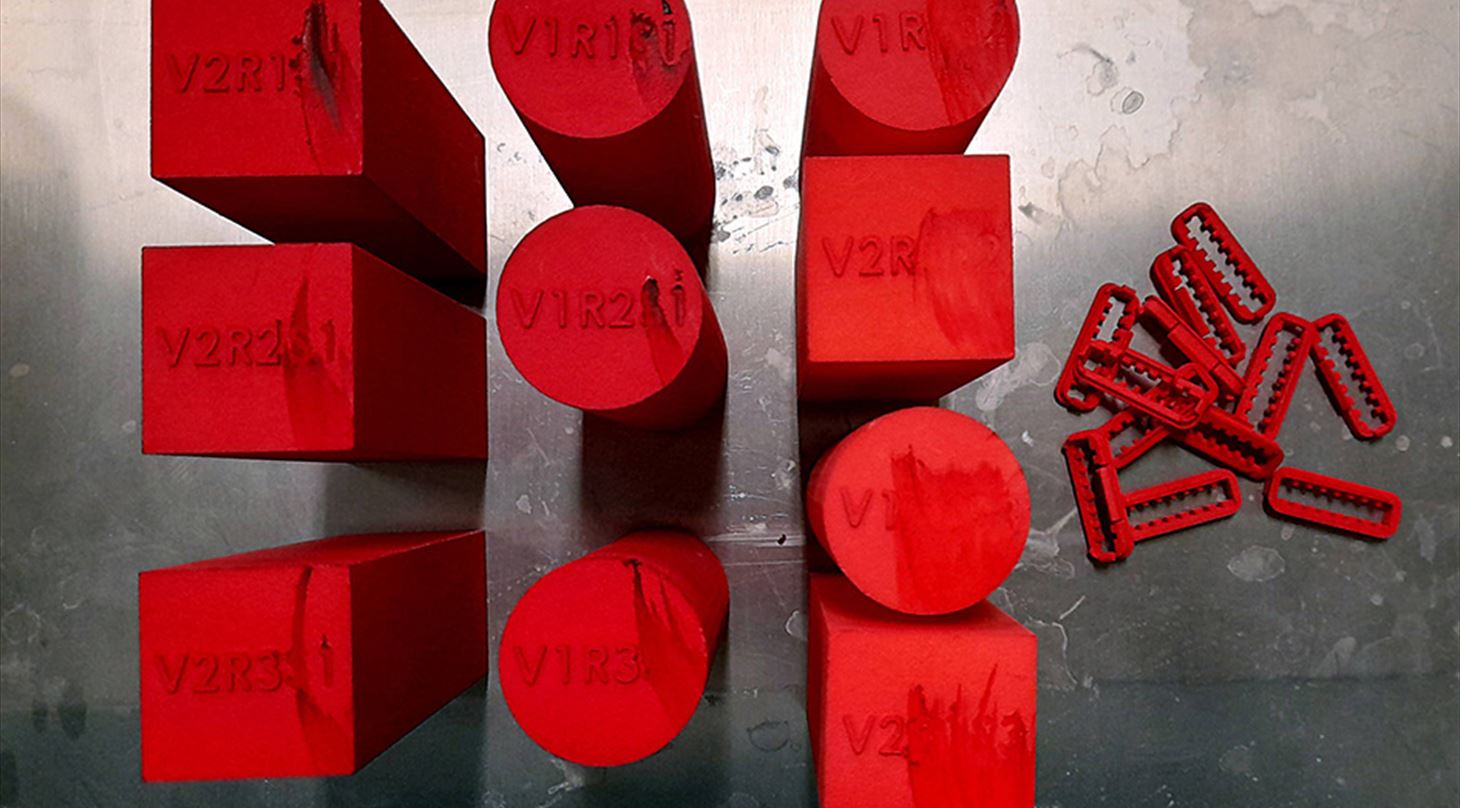
Attention: New standards for colours tested on 3D printed parts
How do we develop new standards for coloring materials to increase workplace safety? That was the question Pers Group sought to answer in a MADE Material Demonstrations project with the Danish Technological Institute.
Red sign = Attention
We are familiar with warning colors on roads, which signal danger with striking colors and high-contrast color drawings - and the same principle is used on the factory floor in production when sharp objects need to be avoided.
The company Pers Group from Vejle, a supplier of industrial equipment such as industrial washing machines and heaters, colors materials for many different industries. A growing interest in coloring in signal colors - for example, orange and red - has prompted the company to test new types of coloring and develop new standards for the industry to enhance quality assurance:
- Coloring is used, for example, for traceability of machine parts such as knives or cable ties. The colors currently used - primarily blue - do not suit all productions. One should be able to see if there is a small piece from the production machines that falls onto the actual product, so it does not end up with the end user, says Jens Brietzke, Area Sales Manager at Pers Group.
Coloring can also be used to increase employee safety by warning of potential dangers in the workplace. For example, sharp objects can be colored red or orange to indicate that employees should be particularly attentive and avoid placing their hands in those areas.
New knowledge in MADE projekt
The method used for the already approved colorings may not necessarily work for red or orange. So what is needed before coloring in signal colors meets customers' needs?
Many parameters can affect the result, and in the MADE project, Pers Group has been focused on ensuring a solid factual basis for their future colorings.
We have gained new knowledge that we could not have obtained in the same time frame without the MADE project. It was an obvious opportunity to get external input.
- Jens Brietzke, Pers Group
Avoid colors rubbing off
To investigate the limitations of the new coloring techniques, the Technological Institute 3D-printed test elements in the form of nylon round bars. These test elements were then colored by Pers Group and cut into slices for further analysis and evaluation.
- We tested the penetration depth - that is, how far the color penetrates into the material - the difference between different colors, smudging, and to what extent the coloring can withstand the chemical reality awaiting them in the industry, where machines are cleaned with harsh basic or very acidic cleaning agents, says Morten Lisberg Jørgensen, consultant and 3D printing specialist at the Danish Technological Institute.
After correspondence with companies in the food industry, a strong basic and strongly acidic chemical was selected. Both are foam cleaning agents commonly used in the industry for cleaning items for food contact. The smudging test revealed whether it is possible to see color smudging on the nylon slices when exposed to the chemicals according to the manufacturer's Ecolab instructions.
It turned out, among other things, that the coloring tended to smudge unless it had undergone a 3S post-treatment. A 3S post-treatment is a process where chemical vapors smooth the surface, make it water-resistant, and encapsulate the coloring so that it does not smudge during cleaning. On the 3S post-treated elements, there was no smudging at all.
Surprising penetration dept
While smudging yielded promising results, the penetration depth posed difficulties. Using a microscope, the exact depth to which the color had penetrated into the nylon slices was analyzed. The desired penetration depth was 300 micrometers, but the tests yielded results only between 40 and 80 micrometers.
We expected the penetration depth to vary if we adjusted parameters such as temperature, duration, or color, but our tests show no significant difference. The penetration depth remains fairly consistent even when we adjust the different settings.
- Morten Lisberg Jørgensen, Danish Technological Institute
”The project made a big difference”
The results of Pers Group's tests showed a penetration degree that, although it did not reach the originally desired depth, proved to be within acceptable limits for many of their customers.
- The next step is to work with the customers for whom, based on these tests, we can document that we meet the identified criteria. These are customers from the industrial production of plastic parts and 3D printing. This area currently covers around 60 percent of our current inquiries. Within the food industry, we still need to further investigate whether we can meet the desired requirements, says Jens Brietzke and continues:
- As coloring in signal colors is such a new concept that there are not yet widely accepted standards, we hope that with pioneering demonstrations like these, we can help define what the requirements should be in the future.
- It is a great advantage for small and medium-sized companies to participate in MADE projects. Both because companies can achieve more through this - but also because our results are verified by a competent third party, which is extremely important in the markets we target, Jens Brietzke concludes.
About MADE demonstration projects
With a MADE Demonstrations Project, a small or medium-sized company can receive up to 100,000 DKK in support to solve a specific challenge in the company or test a new technology in production. By being connected with the Danish Technological Institute, FORCE Technology, Alexandra Institute, or DAMRC, one gains access to the technologies, knowledge, and expertise necessary to address the specific challenge in the company. This can be within materials or production.
There is an ongoing application deadline for demonstration projects.
MADE Demonstrations Projects are made possible with support from the Industry Foundation and the Danish Business Promotion Board.