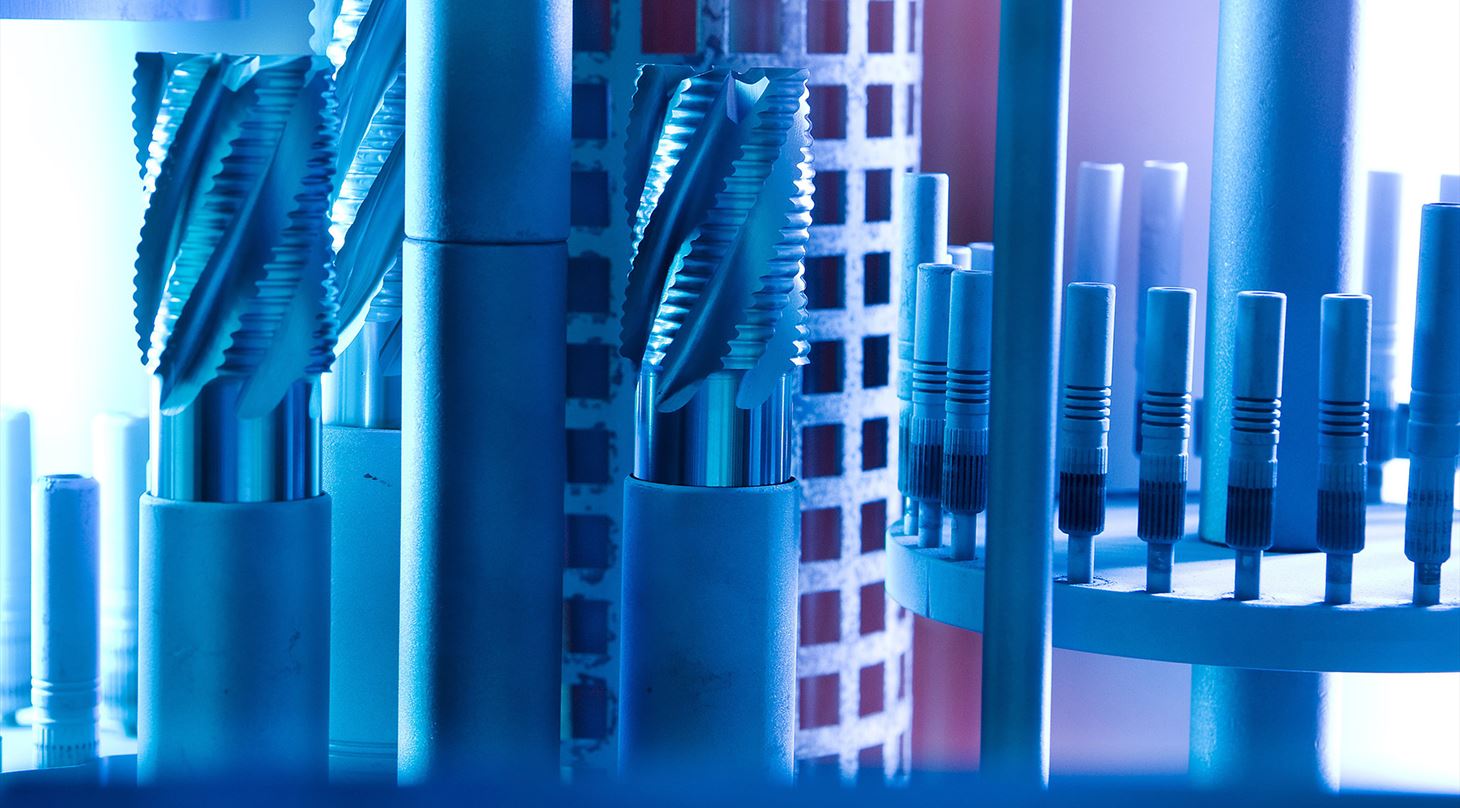
Tribology – friction, wear, release, lubrication
Coatings solve problems related to wear, galling, release, corrosion and more
The life span of tools and machine parts largely depends on the wear they are exposed to - but this wear can be substantially reduced with protective surface treatments.
The right surface treatment, combined with optimal material selection, can minimize or even eliminate wear. In many cases, lubricants can be dispensed with altogether, and a PVD coating can, for example, often replace problematic hard chrome plating.
PVD coatings can be applied to a wide range of materials, including steel, stainless steel, copper, titanium, and aluminium alloys, ceramics, plastics, and glass. The PVD process takes place without hazardous or environmentally harmful chemicals and typically adds only a very thin layer (usually 1–5 μm), meaning component dimensions and tolerances are only minimally affected.
We provide coatings for nearly all types of production tools, machine parts, and finished components - to prevent wear, corrosion, friction, galling, adhesion, and ensure easy-release.
Wear
Wear issues can almost always be solved with the right surface solution. For example, the service life of production tools in the metal and plastics industries, as well as a range of machine components, can be increased by more than a factor of 10. Hard chrome for wear protection, which is being phased out for health reasons, can often be replaced by PVD coatings.
We have extensive knowledge and experience with all types of wear and how each can be minimized or eliminated.
Galling and adhesion
Galling or adhesive wear - when two surfaces slide against each other - can be destructive to the surface. Whether it’s galling between a tool and the workpiece or between machine parts, sliding on each other (e.g., made of stainless steel), the Tribology Center has the right solution for you.
Release
Demolding and release in injection molding can be significantly improved. At the same time, wear and corrosion of the mold can be significantly reduced, and the quality of molded parts remains high throughout the (extended) lifetime of the mold. We have solutions for nearly all plastic types and tool materials (tool steel, aluminum, and copper alloys).
Minimization or elimination of lubrication needs
Reduction or elimination of lubricants in moving mechanical parts can often be achieved with our specialized self-lubricating, low-friction coatings - such as so-called Diamond-Like Carbon (DLC) coatings. Dry lubricating coatings can be used both without and and in combination with conventional lubricants and are also effective in vacuum and outer space applications.
Dimension correction
Our chromium nitride coating (CrN-SD) can be used for dimensional corrections during the repair of injection molding tools or in case of machining errors. Coatings can be locally applied in thicknesses up to 30 μm and are most often ready for immediate use without further processing.
Corrosion
PVD coatings provide highly wear-resistant corrosion protection for tool surfaces, etc. The coating prevents direct contact between the substrate and the environment, significantly reducing the risk of corrosion. PVD coatings are extremely hard and scratch-resistant, as well as highly resistant to oxidation and corrosive chemicals.
Pin-on-Disc (POD) wear testing
Pin-on-disc testing is a well-established method for assessing the tribological properties of materials. In the test, a pin is pressed against a rotating disc under controlled conditions, allowing friction and wear to be measured between different materials under varying load, speed, temperature, and atmospheric conditions, as well as under different types of lubrication.
Benefits:
- Reliable and reproducible results
- Tests can be performed under various environmental conditions (temperature, humidity, atmosphere)
- Both dry and lubricated contacts can be tested
- Results can be applied directly to material selection, optimization, and lifetime estimation
Our pin-on-disc tests are adaptable to a wide range of requirements and can be run at both low and high temperatures to simulate arctic, tropical, and industrial environments.
We help you assess your material’s wear and friction characteristics under realistic operating conditions.