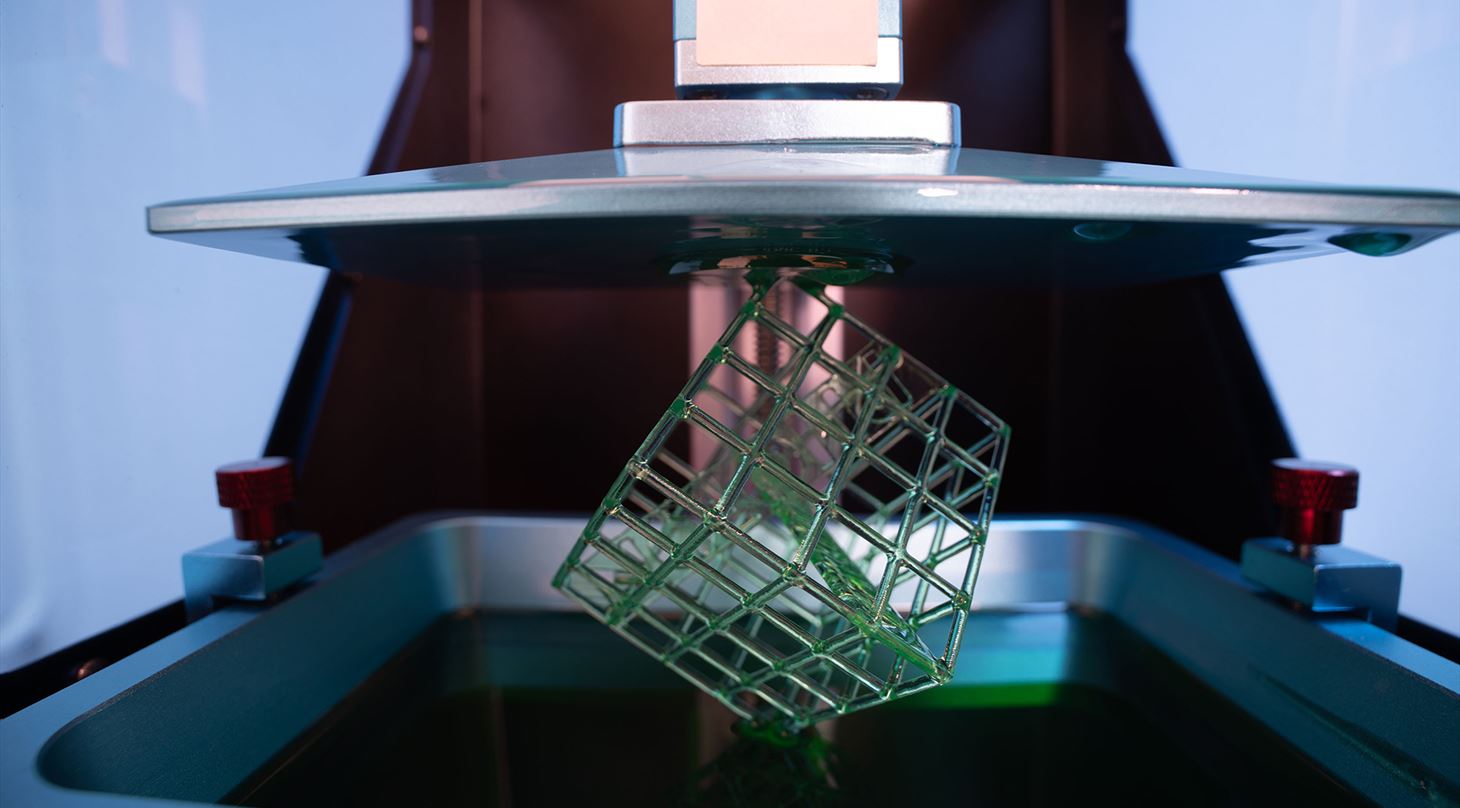
Vat Photopolymerization provides high precision and very fine surfaces
Today, several industries have embraced Vat Photopolymerization. This is mainly due to the technology's high precision in the surfaces, a large material selection, and unique material properties.
In short, the Vat Photopolymerization technology works by bonding a plastic material together by a chemical reaction in a closed system. The material itself consists of a liquid resin which is placed in a vessel where the resin is cured with a light source. This way, so-called radicals are released in the liquid and form polymer chains which are then cured into a solid material on the platform located in the machine. Consequently, when printing with resin, it is important that you consider internal channels or escape holes during the design process, so you ensure that you can get all excess resin out of the parts.
Try an online course in Vat Photopolymerization
Bottom-Up or Top-Down?
Depending on where the platform is located in the machine, a distinction is made between Bottom-Up and Top-Down machines where the difference lies in the elevation technology and where the light source is located.
- In both machines, you will have a tub – or a vat - with the photochemical liquid: But with Top-Down machines there will be a platform that gradually goes further down into the tub, and the light source is located on top. On the other hand, with Bottom-Up machines, the platform will be pulled up from the tub with the photochemical liquid, and the light source is located at the bottom. Of course, for the latter this will also give some restrictions on how big you can make your part, because if the part is too heavy, there is a probability that it will fall off the print platform, says Sigurd Vigen Pedersen, consultant at the Danish Technological Institute.
High accuracy and many materials to choose from
An obvious advantage of Vat Photopolymerization is the large inventory of materials that offer fine tolerances that are super accurate compared to other 3D printing technologies. The precise surfaces of the parts mean - among other things - that the technology is widely used in both the dental and audio industry, where 97 percent of all hearing aids today are manufactured with Vat Photopolymerization. At the same time, Vat Photopolymerization is one of only two 3D printing technologies that have the ability to print with transparent materials which has gained great popularity in the dental industry for printing braces - or printing prototypes for car headlights.
Although the technology offers great material freedom, it does not necessarily mean that all materials have equally good properties for the specific print.
- When it comes to materials, it is easier to design with materials for a specific use, but there is not one material that can do it all, as we more or less see with Powder Bed Fusion. Instead, each material has its specific use case which also means that you must be good at choosing material when working with Vat Photopolymerization, says Sigurd Vigen Pedersen.
From casting tools to finished components
When it comes to the development within Vat Photopolymerization, it is especially about casting tools for injection moulding of plastic, where it is both possible to make complex cast parts or to make a wax model of the final mould.
Read about all the AM technologies
In addition to the development of casting tools, the technology has great development potential in the manufacture of shoe soles. Vat Photopolymerization makes it possible to print with elastomers, which are polymers with elastic properties - a rubber-elastic plastic. Therefore, the technology is an obvious choice for designing shoe soles that require individual adaptation - Adidas and New Balance, for example, have used this.
Brittle and UV-sensitive parts
There are a number of immediate benefits to using Vat Photopolymerization, but there are also certain disadvantages.
The disadvantages of the technology are related to the material properties: Although the technology makes it possible to use many different types of material, you must be aware that the parts are often more brittle and porous than with other 3D printing technologies. Therefore, the mechanical properties are not as good in the end product, because the technology prints with hardened plastic
- Sigurd Vigen Pedersen, Danish Technological Institute
- Another disadvantage is that hardened plastic is UV-sensitive. This means that if the part is out in the sun, it will harden over a period of time, and thus the properties will also deteriorate over time - unless of course you close the surface with a surface coating or varnish, says Sigurd Vigen Pedersen, and adds:
- At the same time, we also see that there has been much more data on the materials, and this means that the materials will continuously become better and better at resisting UV light.
Faster machines and (more) unique materials
Regarding the future of Vat Photopolymerization, there are several parameters that you will be able to tweak to get even more out of the technology. Therefore, Sigurd Vigen Pedersen guesses that a possible future scenario for the technology could be an increase in the speed of the machines to streamline the printing process. Another guess on a possible future scenario is that there is a further development on the material front, which could mean (more) unique customized materials with special applications that can ultimately function as end components.
It will be interesting to see if the materials and processes that are on the market now and in the near future will be good and strong enough to print end components for the high-runner industries, such as automotive and aviation
- Sigurd Vigen Pedersen, Danish Technological Institute
Want to know more about Vat Photopolymerization?
If you as a company are interested in knowing more, trying out Vat Photopolymerization or having the technology implemented, the Danish Technological Institute is ready to guide companies to the best possible solutions or establish contact with the right partners. In addition, the Danish Technological Institute offers online training material to provide insight into Vat Polymerization as well as the possibilities and limitations of other 3D printing technologies.