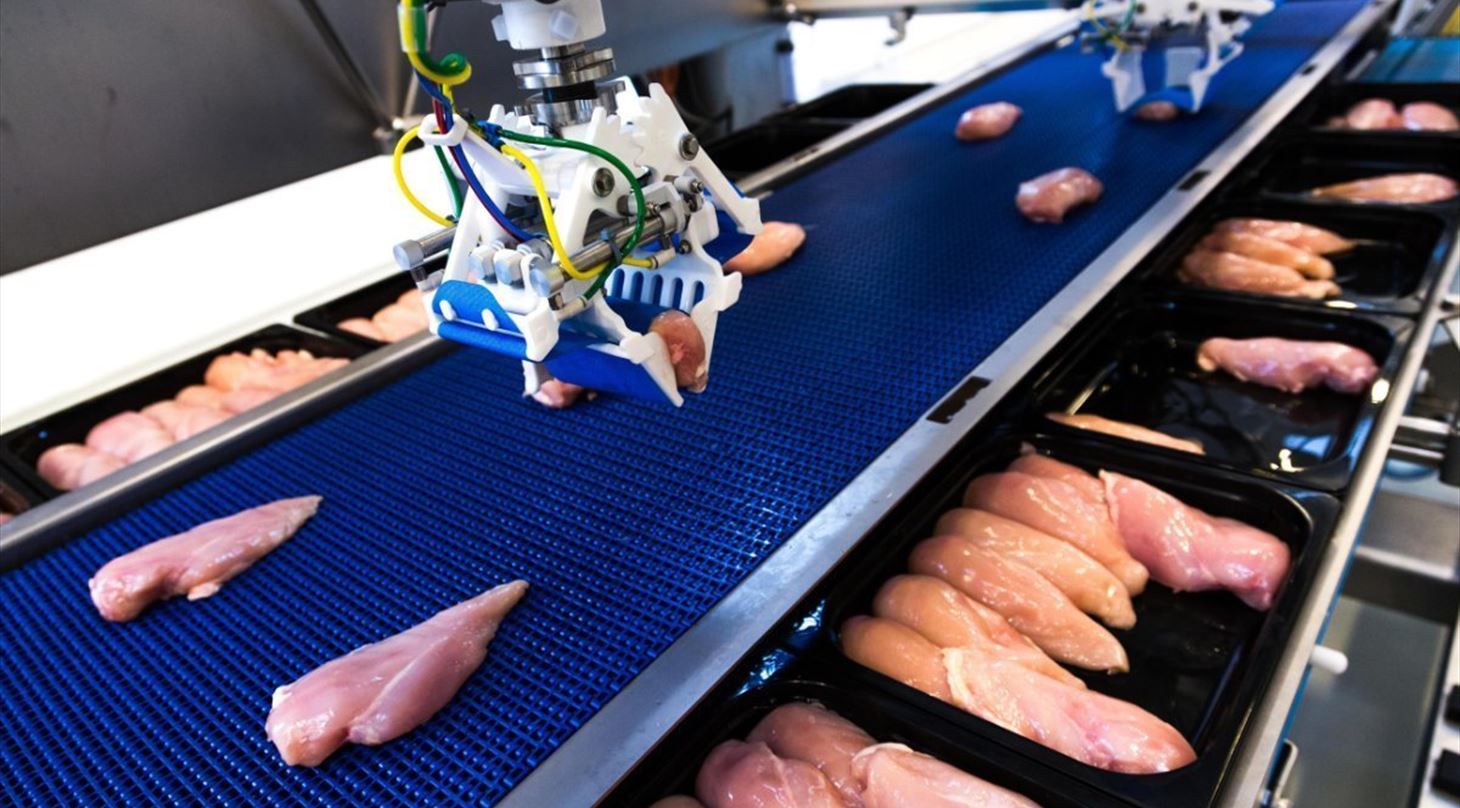
3D-printed robotic gripper in nylon – approved for food contact
Marel makes processing equipment for the food industry, and in order to increase the efficiency and adaptability of the production, they collaborate with the Danish Technological Institute on 3D printing of a number of components - including their robotic grippers.
The Danish Technological Institute has been delivering 3D printed parts to Marel for almost five years, and two years ago the robotic grippers became a regular part of the 3D printing production. The grippers, which are printed in nylon, comply with the standards of the food industry and are part of the processing equipment that Marel produces for their customers. Here, they are used on the robotic arms that grab e.g. fillets, when they have to be lifted off and on the conveyor belt. Initially, the grippers were produced in very small batches at an average of one set of grippers a month. But as the grippers have proven their worth and the benefits have become evident, production has increased significantly.
Design freedom and flexibility
Initially, 3D printing offers a great design of freedom during the development phase, but by 3D printing the robotic grippers, Marel also get a huge flexibility, as they have the possibility of making design changes on the grippers from customer to customer, without the extra cost of milling tools. In addition, Marel only need to have a small number of grippers in stock together with the CAD drawings, and then the gripper can be 3D printed on demand with a delivery time of down to 3 days - thus reducing the cost of storage.
Let us help you with AM production
- With 3D printing, we have a much greater freedom, since we can continuously optimize the design and e.g. combine several functions in a item. That way, we can avoid assemblies and at the same time reduce the overall weight of the item, says Jens Dalgaard, Mechanical Designer at Marel.
In the video below, Jens Dalgaard talks more about the opportunities that Marel gets from using 3D printing.
Approved for food processing
As the only 3D printing manufacturer in Denmark, the Danish Technological Institute meets the food regulations for 3D printing in both metal and nylon.
- The robotic grippers for Marel are 3D-printed in nylon, and our production processes as well as the material are completely in accordance with food regulations. This means that we have complete traceability throughout the production process - from powder to finished product - and the same applies to our 3D printing in metal, where we print in titanium, aluminium and stainless steel for the food industry, says Mads Østergaard, Section Manager at the Danish Technological Institute.
In addition to complete traceability, the 3D printing production at the Danish Technological Institute also complies with the rules of good manufacturing practice, which include that no toxic materials or bacteria-filled tools are used in production.
Furthermore, successful migration tests have been carried out on the finished products as part of the Declaration of Conformity, which ensures that substances from the 3D-printed product do not migrate into the food, and sensory tests have determined that the products do not emit fragrance and taste. Read more about AM and food contact
Subsequently, the Danish Technological Institute has also developed metal detectable nylon as well as the dipping process '3S' (Super Smooth Surface). With 3S, all surfaces of the 3D-printed item are treated - including interior channels. The treatment creates a chemical change of the surface which makes it extra smooth and thus easy to clean, while the dimensions, color and strength of the item remain unchanged.
The metal detectable nylon is obtained through a refining process where the nylon powder is mixed with metal in the right ratio, which allows the 3D printed nylon parts to be traced in the metal scanners of the food production. Initially, Marel expressed the need for these materials, which the Danish Technological Institute then developed, and subsequently Marel have had the materials for testing. Both materials are approved for food contact.