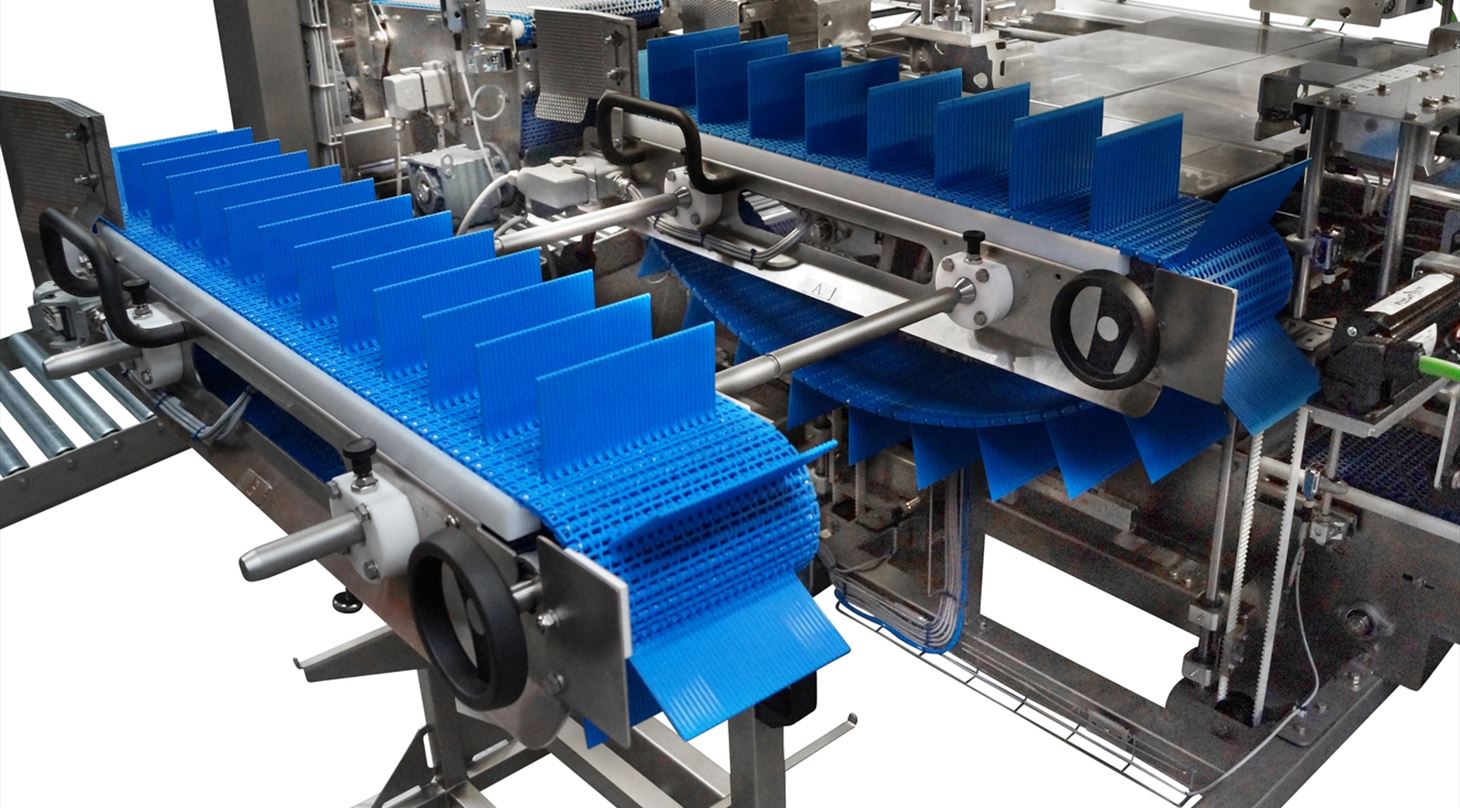
Custom 3D printed carriers for SR Pack's flight belts
SR Pack builds packaging machines for the food industry – and they had a challenge with a carrier for their flight belts. Thanks to 3D printing and help from the Danish Technological Institute, that challenge was solved.
The packaging machines from SR Pack are used for packaging and handling products in the food industry – especially bread, where SR Pack targets the larger industrial bakeries.
3D printing is interesting to us because we build high-tech machines, and 3D printing is rapidly developing - and we are as well.
- Heine Sønderskov, SR Pack
The machines from SR Pack are custom built solutions, and the company saw a potential for using 3D printing for some of the components. In this case, they have used 3D printing to create a carrier that is incorporated into a modular flight belt to lift and move products according to the customer's wishes.
In the video below, SR Pack purchaser, Heine Sønderskov, talks about the journey with 3D printing.
Better looks – and better planning
The reason for choosing a 3D printed component was that SR Pack was not entirely satisfied with the appearance of their existing carrier. It had two colours and was glued together, so the 3D printed version offered a nicer look that matched the appearance of the machines. Additionally, the 3D printed version offers much greater design flexibility, so SR Pack can shape the carrier the way they want it, without being limited by available components.
Another challenge with the original carrier was that it involved many handling processes. It had to be delivered from several suppliers, and SR Pack had to depend on those suppliers delivering on time – and when the parts arrived, they also need to be assembled.
The advantage of using 3D printing is that it reduces the time spent waiting for parts to arrive because SR Pack can order them in advance rather than afterward.
- Economically, the 3D printed model may not be the cheapest, but when considering the overall time and back-and-forth involved in assembly, it is clearly an advantage for us to use the 3D printed model, says Heine Sønderskov, Purchaser at SR Pack.
3D printing is part of the future
Now, SR Pack are starting to see more opportunities to use 3D printing - especially after the involvement of the Danish Technological Institute, which highlighted a number of benefits and possibilities within 3D printing. So the technology is now part of the toolbox when SR Pack is looking for solutions that can help the company develop and improve its products.
The collaboration with the Danish Technological Institute has been great with good sparring and exchange of ideas, and we have gotten some excellent parts – especially since they are challenging to print with very fine tolerances. So, it has been a great process.
- Heine Sønderskov, SR Pack