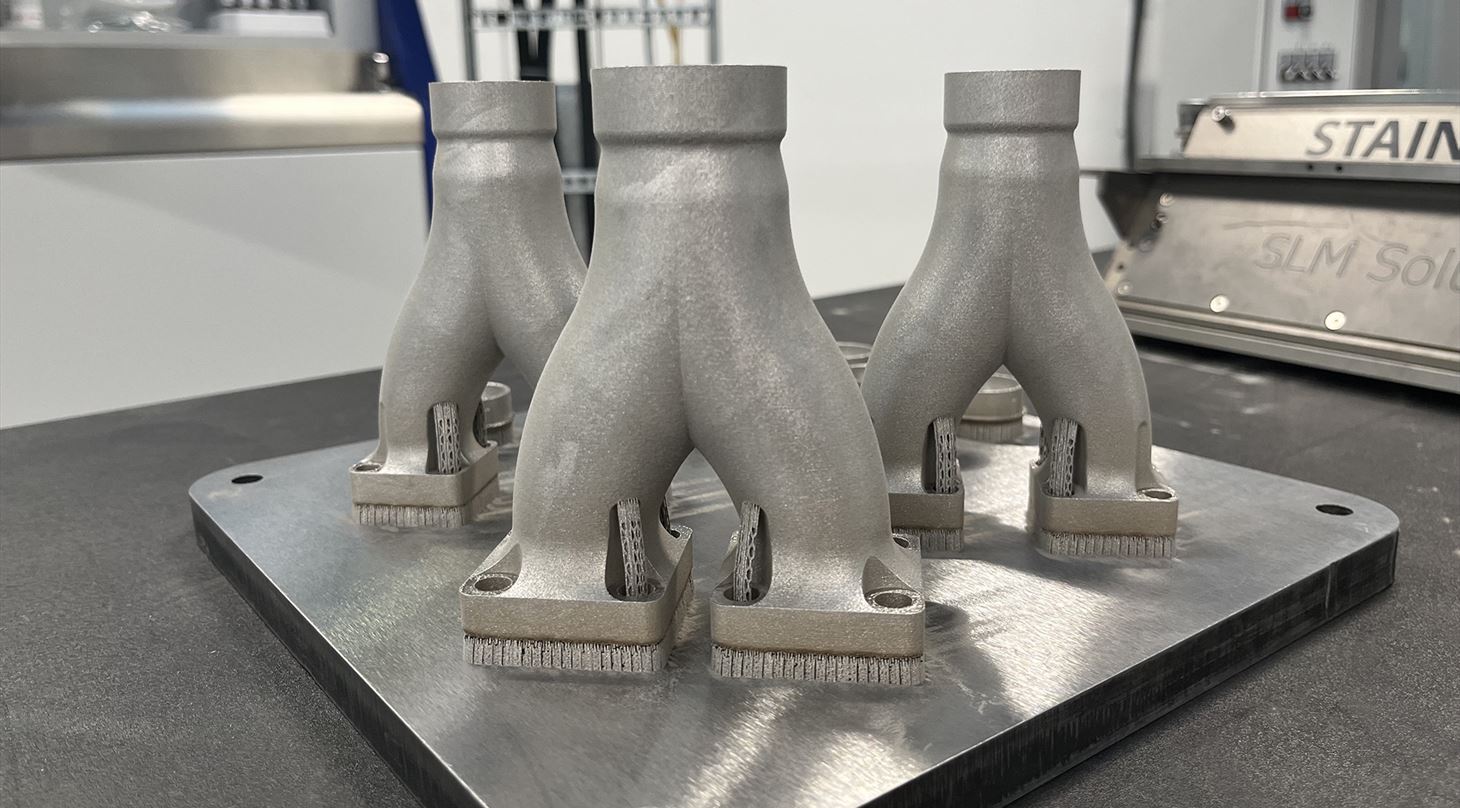
3D printing offers higher efficiency and lower energy consumption for Advansor's heat pump system
The Danish company Advansor produces CO2 climate solutions in the form of refrigeration systems - it can be heat pumps or air conditioning systems - and they have experienced issues with pressure loss before one of their ejectors. Therefore, they wanted to investigate whether the design could be optimized for 3D printing.
In the DfAM Green design course, which is initiated by Danish AM Hub, Advansor created a so-called Y-piece that can withstand the pressure from the gas inside, while also removing a lot of standard pipes that would otherwise need to be welded. For this, they had help from 3D printing specialists at the Danish Technological Institute (DTI). With the design for 3D printing, they have thus gone from 17 parts to just three parts. This means that they can create smoother transitions from one pipe size to another, thereby reducing pressure loss.
- For us, pressure loss is a matter of energy loss and a larger climate footprint, and therefore it is always interesting for us to optimize. 3D printing is ideal for us because of its large degree of design freedom, which means that we can design the desired geometry. With 3D printing, you can print a very compact part, which at the same time is easy to integrate into our systems," says Kenneth B. Madsen, CTO at Advansor.
In the video below, Kenneth B. Madsen talks more about the 3D printing optimization process and the participation in DfAM Green.
Saved energy results in a lower carbon footprint
By optimizing the design and using 3D printing there is a great potential to achieve a significantly lower carbon footprint. The system uses CO2 to generate heat, but with the design advantages of 3D printing, the heat can be utilized better when distributing the gas in the heat pump.
- With 3D printing, we can design a Y-piece and place two ejectors next to each other, so the flow into the ejectors becomes better. This results in higher pressure both before and after, generating more heat, thus saving energy from other energy sources to use for district heating. This gives you a better overall efficiency for your system, says Sigurd Vigen Pedersen, consultant at DTI.
When looking at sustainability, it can be divided into two parts. First, there is a material part, which in this project is a minor part because it is a relatively small amount of material that is saved. However, the energy aspect is substantial.
The energy saving on a single component is around 1 percent. This may not sound like much, but for a 2MW heat pump, 1 percent equals a saving of 70,000 kWh per year – or equivalent to 19,400 kg of CO2 annually.
For us, pressure loss is a matter of energy loss and a larger climate footprint, and therefore it is always interesting for us to optimize
- Kenneth B. Madsen, Advansor
About DfAM Green
Over a six-month period, Danish AM Hub - in collaboration with DTI, Hexagon, and Implement Consulting Group - has had four Danish SMEs engaged in an innovation course aimed at equipping the companies to take advantage of the sustainable, technological, and business potential within 3D printing to an even greater extent. The course has been named Design for Additive Manufacturing Green (or DfAM Green), and it focuses on spreading 3D printing to small and medium-sized enterprises, as well as providing concrete support and assistance in working with the technology through design.
The specific goal of the DfAM course is to redesign the SMEs’ products or components to make them more sustainable and, at the same time, capable of being manufactured with e.g. greater strength, less material waste, new and improved functionality, or on-demand.