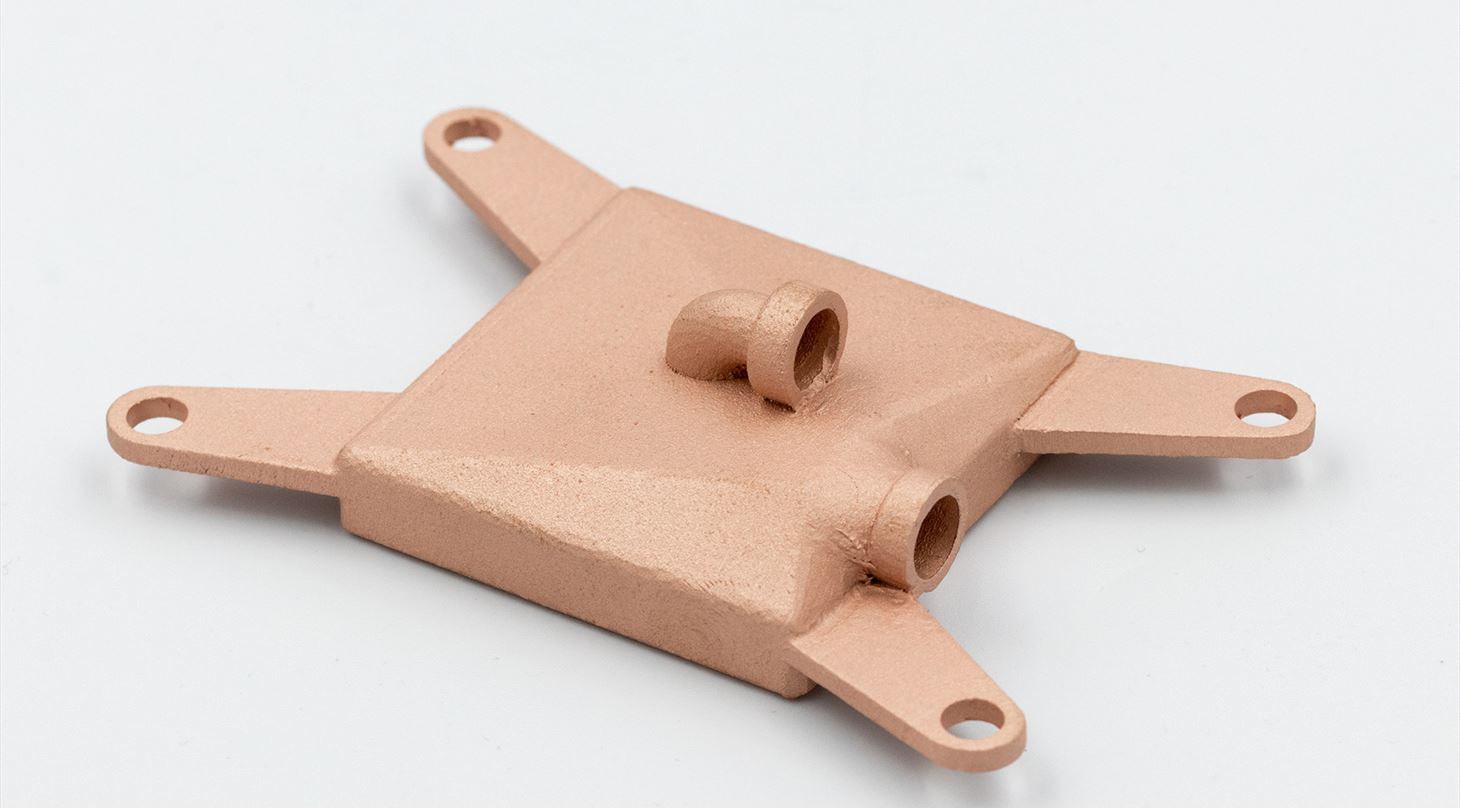.jpg)
3D printing provides better utilization of district heating in Heatflow's evaporator
Heatflow is a company that makes solutions within thermal systems which can be connected to e.g. servers to utilize the waste heat for district heating – for this, they wanted to investigate the possibilities of using 3D printing to address the thermal challenges.
Heatflow chose to participate in the design optimization course DfAM Green, which is initiated by Danish AM Hub, because 3D printing offers some possibilities to address thermal challenges with performance - i.e. to increase performance for customers by cooling electronics better.
In the project, Heatflow wanted to use 3D printing to optimize an evaporator which is part of a server application. The evaporator is used to retrieve heat from a server and transfer it to the district heating network - ideally with as little heat loss as possible. Through a re-design, the hope is that the excess heat can be utilized even better - and at the same time, Heatflow wanted to add some features that were missing in the existing design.
We are interested in improving our systems to better cool the electronics and utilize the surplus energy optimally. For instance, many of our customers want to reuse the waste heat generated by the electronics
- Dennis Nadal Jensen, Heatflow
In the video below, Vice President of Technology at Heatflow, Dennis Naldal Jensen, explains more about the participation in the DfAM Green course and the component they wanted to optimize.
Inner lattice structures preserve more heat
As it was a well-known product, the new 3D printing design could be benchmarked fairly quickly against the existing one. In a very short time and with very few resources compared to what was used in the original design, Heatflow and DTI succeeded in creating something that matches what Heatflow spent a long time developing – plus some additional features.
With a 3D-printed evaporator, the cooling system is more efficient and retains more heat due to the internal lattice structures. This results in a significant energy advantage, an environmentally friendly solution, and overall increased efficiency.
By designing it for 3D printing and increasing the efficiency of our cooling solution, we gain a huge energy advantage, which means that the overall result for our products and for our customers is increased efficiency and a great environmental benefit
- Dennis Nadal Jensen, Heatflow
The design freedom of 3D printing makes it possible to work with different lattice structures. Such lattices increase the surface area, contributing to better heat transfer and thus overall performance. The new design, which is optimized for 3D printing, consists of one component as opposed to the original design which consisted of six parts. Because 3D printing allows for new geometric solutions, it became possible to place the liquid intake directly on the hot zone, ensuring better distribution of the liquid used to cool the entire internal structure - and the design made it easier to get rid of the steam.
- 3D printing allows you to create a more efficient evaporator because you can create interesting structures. You can increase the effectiveness of the evaporator and thus make a greater contribution to district heating, instead using other energy sources, says Sigurd Vigen Pedersen, consultant at the Danish Technological Institute.
About DfAM Green
Over a six-month period, Danish AM Hub - in collaboration with DTI, Hexagon, and Implement Consulting Group - has had four Danish SMEs engaged in an innovation course aimed at equipping the companies to take advantage of the sustainable, technological, and business potential within 3D printing to an even greater extent. The course has been named Design for Additive Manufacturing Green (or DfAM Green), and it focuses on spreading 3D printing to small and medium-sized enterprises, as well as providing concrete support and assistance in working with the technology through design.
The specific goal of the DfAM course is to redesign the SMEs’ products or components to make them more sustainable and, at the same time, capable of being manufactured with e.g. greater strength, less material waste, new and improved functionality, or on-demand.