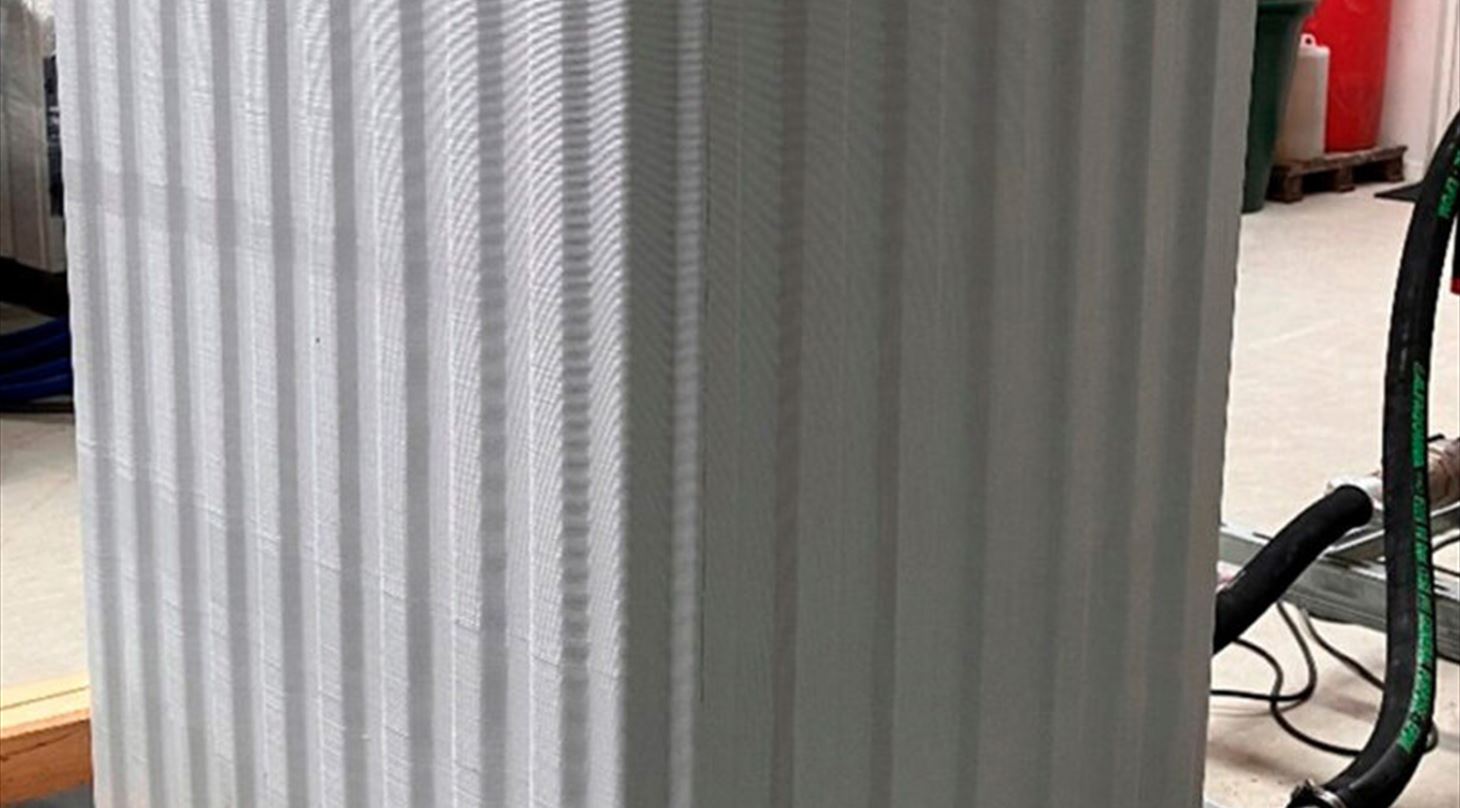
3D Printing shortens delivery time for in-demand cooling tanks
A MADE Demonstration Project together with the Danish Technological Institute has shown that the company CAAS can use 3D printing as a fast, flexible, and cost-effective method to produce custom-designed tanks for the rapidly growing market for so-called 'immersive cooling' – that is, cooling by immersion in a liquid – in Europe.
Hot Chips, Cool Liquid
When the body works, it generates heat. The same applies to computers and servers.
However, instead of muscles, it is chips – small square pieces of electronics that work hard to perform calculations and processes – that generate the heat.
Just like the human body, chips can overheat, and when that happens, performance deteriorates, and the component's lifespan is shortened.
In fact, it is a necessity in data centers that store servers to constantly cool the many floors of IT equipment. Otherwise, there is a risk of system crashes and data loss, which can have serious consequences for businesses and users.
An effective way to cool IT components is to immerse the heat-generating elements in a liquid that is continuously cooled – that is, what is called immersive cooling.
The image shows the inside of the 3D-printed tank. It is filled with a clear, non-conductive oil. On the right side, hardware from a TV is submerged in the oil.
CAAS is a technology company that operates and finances cooling systems for larger customers and companies with significant cooling needs. CAAS initiated a MADE Demonstration Project with the aim of creating 3D-printed tanks for the rapidly expanding immersive cooling market in Europe. An objective that largely succeeded, although further development is needed to prevent small leaks.
- Now we know that it can be done. 3D printing has proven to be a fast, flexible, and cost-effective manufacturing method for these tanks, says Søren Dalgaard, CEO at CAAS
Custom-designed tanks produced on European soil
When using immersive cooling, the chips are immersed in a special non-conductive liquid. This liquid can absorb and transport heat away from the components. To keep the liquid cool, it circulates through a cooling system. The system works by passing the heated liquid through a heat exchanger, where the heat is absorbed and transferred to another liquid or air, which is then discharged from the tank. The now cooled liquid is then sent back to the chips to once again help them get rid of the heat.
- Immersive cooling requires a tank that fits the cooling needs. Today, you can get custom-made tanks, but they are manufactured in China and have a long delivery time due to transportation. If you could find a way to produce custom-designed tanks quickly and cost-effectively in Europe, you would be able to deliver significantly faster and thus meet the market's needs, says Søren Dalgaard, CEO at CAAS.
With this problem in mind, CAAS teamed up with specialists from the Danish Technological Institute to investigate whether 3D printing is a usable production technique for this purpose.
From the start, we have had our sights set on 3D printing because it is a fast and flexible production method
- Søren Dalgaard, CEO at Caas
Success – with a small leak
In the project, the Danish Technological Institute developed a design that was 3D printed by MDT Flexible Products.
- In the final solution, we have 3D printed a tank with some special features. At the bottom, we have incorporated a pipe system that can evenly distribute the cool liquid throughout the tank. The sides of the tank are hollow and therefore act as an overflow safeguard for the tank. Everything except the bottom is printed as a single unit using large-scale FDM printing, where the printer is assembled with a robot arm, and the material is PETG (a variant of polyester modified with glycol to improve the plastic material's properties), says Malthe Wellendorf Gissel, consultant at the Technological Institute.
The sides of the tank are hollow and act as an overflow safeguard for the tank. At the bottom, the white, built-in pipe system can be seen, which evenly distributes the cool liquid throughout the tank.
At CAAS' workshop in Vejle, the tank has been filled with a transparent and non-conductive oil, and IT equipment has been submerged for cooling.
It works as it should. And the heat that we extract from the liquid can be used for other purposes. If you use this on a larger scale than just this relatively small tank, it can even be used for district heating
- Søren Dalgaard, CEO at Caas
However, the product is not yet fully developed and ready for the European market.
- There is a slight leak. It's not gushing out, but there are some small leaks that need to be addressed before we can send such a tank anywhere. It was outside the scope of this investigation, but the next step will be to fix that, so we get closer to a finished product. Now we know that it can be done. 3D printing has proven to be a fast, flexible, and cost-effective manufacturing method for these tanks, says Søren Dalgaard.
About MADE demonstration projects
With a MADE Demonstrations Project, a small or medium-sized company can receive up to 100,000 DKK in support to solve a specific challenge in the company or test a new technology in production.
By being connected with the Danish Technological Institute, FORCE Technology, Alexandra Institute, or DAMRC, one gains access to the technologies, knowledge, and expertise necessary to address the specific challenge in the company. This can be within materials or production.
MADE demonstration projects are co-financed by the European Regional Development Fund and the Danish Executive Board for Business Development and Growth. Would you like to hear more about the opportunities to test and demonstrate new solutions in MADE? Please reach out to MADE - they cover all of Production Denmark.
This article is originally published by MADE