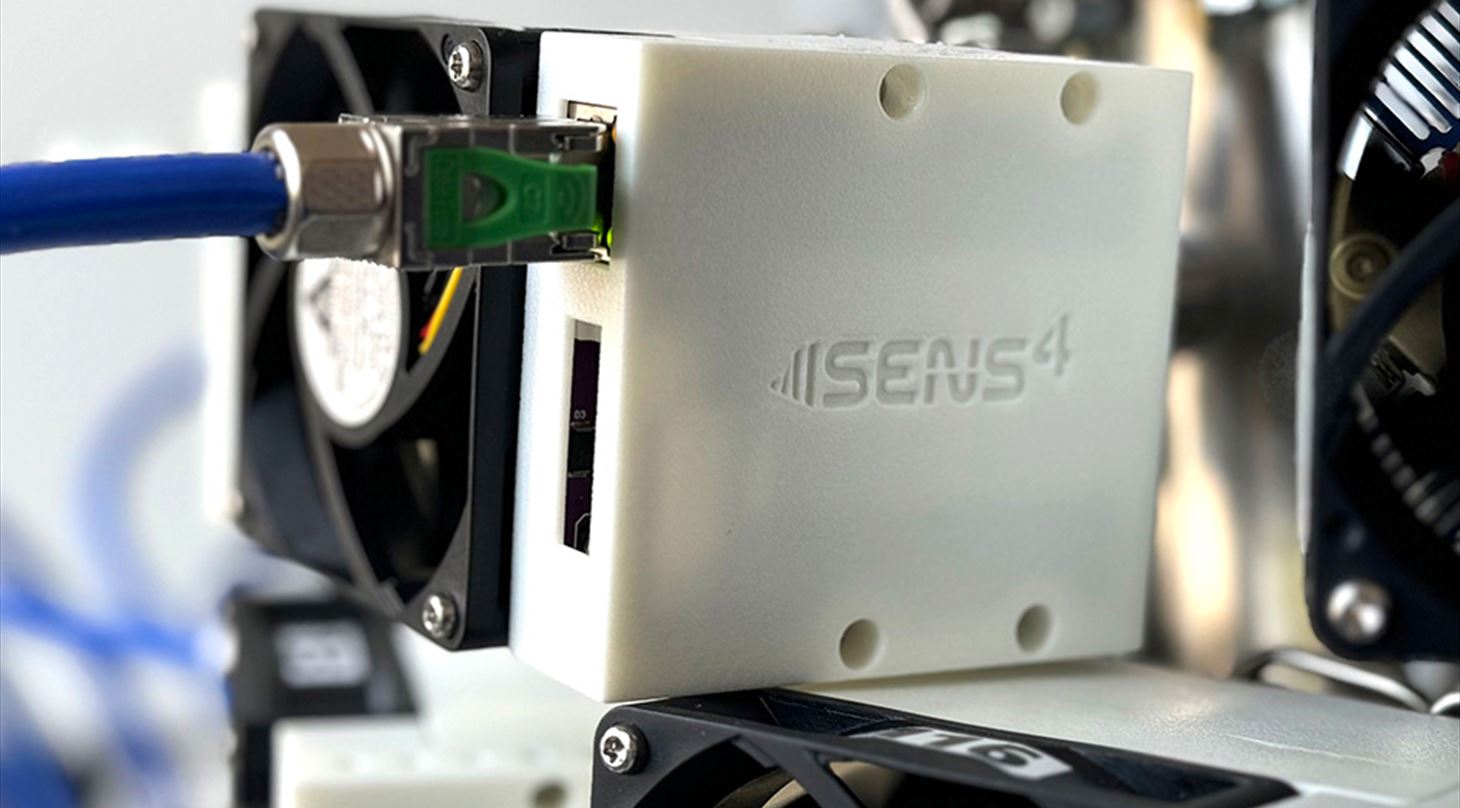
Faster calibration with 3D printing provides significant savings
3D-printed components enable optimized heat transfer design of production equipment, allowing Sens4 to calibrate their measuring instruments two hours faster than normal. With a shorter calibration process, the company will significantly reduce their production costs, according to the assessment after a completed MADE demonstration project together with the 3D printing specialists from the Danish Technological Institute.
An optimized, 3D-printed design resulted in a solution where the calibration time for Sens4's sensors has gone from around 10 hours to around 8 hours per sensor, a reduction of 20 percent.
The Danish company Sens4 manufactures measuring instruments that can measure temperature and pressure with great precision. Sens4 has specialized in measuring vacuum in particular.
The measuring instruments are used in various industries, such as semiconductor electronics manufacturing, surface treatments of optics, pharmaceutical production, and high-tech analytical equipment such as mass spectrometers. Common to them is that they measure and control the pressure in a given process to ensure high quality and uniformity.
Sens4 has automated large parts of their production to reduce production costs and make manufacturing faster. The measuring instruments undergo individual temperature calibration, which is one of the most time-consuming steps in the manufacturing process. Therefore, the company wanted to find a faster method:
Calibration took up to 10 hours per sensor, which meant that with our current capacity we could test a maximum of 48 sensors per day on each of our systems. Our goal was to shorten the calibration time without compromising accuracy
- Caspar Christiansen, CTO at Sens4
This was the problem that Sens4 wanted to solve in a MADE material demonstration project together with the Danish Technological Institute.
3D printing changes airflows
During calibration, the measuring instruments are placed in small temperature control boxes that must reach certain temperatures. It takes time for the boxes to go from one temperature to another, and it was precisely these transition phases that Sens4 wanted to make more efficient.
The MADE demonstration project quickly revealed that there was potential for improvement in the way temperature changes were handled. Using 3D printing technology, more efficient cooling elements and components for controlling the airflow through the test chambers could be designed and manufactured.
On the right side of the image is an example of the optimized 3D-printed cooling fins (light gray), which are intended to cool the test chamber more efficiently than the original cooling fins (blue) with a smaller area.
- With 3D printing, we could experiment with different geometric designs that were not possible before, explains Kristian Rand Henriksen, business manager and 3D printing specialist at the Danish Technological Institute, and adds:
- We created cooling fins with a larger surface area and implemented gyro structures – i.e., indentations that increase the surface area and thus significantly improve heat transfer. This approach allowed us to significantly reduce the time it takes to switch between temperatures. An important part of the testing phase is to expose the sensors to different temperatures, and the faster we can go from one temperature to another, the faster the test is completed.
On the left is a model of the original test chamber. In the middle, a model of the new chamber with indentations in the surface – a so-called gyro structure. The gyro structure is executed to increase the surface area and thereby transfer more heat to the air in the calibration box. On the right is the finished product. The surface area has been increased by 61.5%.
2 hours saved per calibration
The new solution also involved optimizing airflows using specially designed fans and channels, which were strategically placed to maximize efficiency. By directing the airflow more purposefully, Sens4 was able to ensure that the boxes were cooled and heated faster, reducing the overall calibration time.
They tried different designs, resulting in an optimized solution where the calibration process went from around 10 hours to around 8 hours per measuring instrument, a reduction of 20 percent.
- We have seen very reasonable results from the tests that have been carried out. The shorter calibration time means that we can perform two calibration runs in one day, which doubles the capacity and thus the production volume, says Caspar Christiansen.
Significant savings on production costs
The shortened calibration time is expected to cut production costs by approximately DKK 200 per product, which will become more noticeable as demand increases
- Caspar Christiansen, CTO at Sens4
For Sens4, the project has therefore led to an increase in production capacity and more efficient production, and not least a deeper understanding of how 3D printing can be used to tackle complex challenges.
- The collaboration with the Danish Technological Institute has been very positive. We have experienced a solution-oriented team that has been good at presenting new ideas and sharing their knowledge. This has helped us, so now we see great opportunities in using 3D printing for production purposes – also in the future – as it provides the flexibility to quickly adjust and improve our equipment, says Caspar Christiansen.
About MADE demonstration projects
With a MADE Demonstrations Project, a small or medium-sized company can receive up to 100,000 DKK in support to solve a specific challenge in the company or test a new technology in production.
By being connected with the Danish Technological Institute, FORCE Technology, Alexandra Institute, or DAMRC, one gains access to the technologies, knowledge, and expertise necessary to address the specific challenge in the company. This can be within materials or production.
MADE demonstration projects are co-financed by the European Regional Development Fund and the Danish Executive Board for Business Development and Growth. Would you like to hear more about the opportunities to test and demonstrate new solutions in MADE? Please reach out to MADE - they cover all of Production Denmark.
This article is originally published by MADE