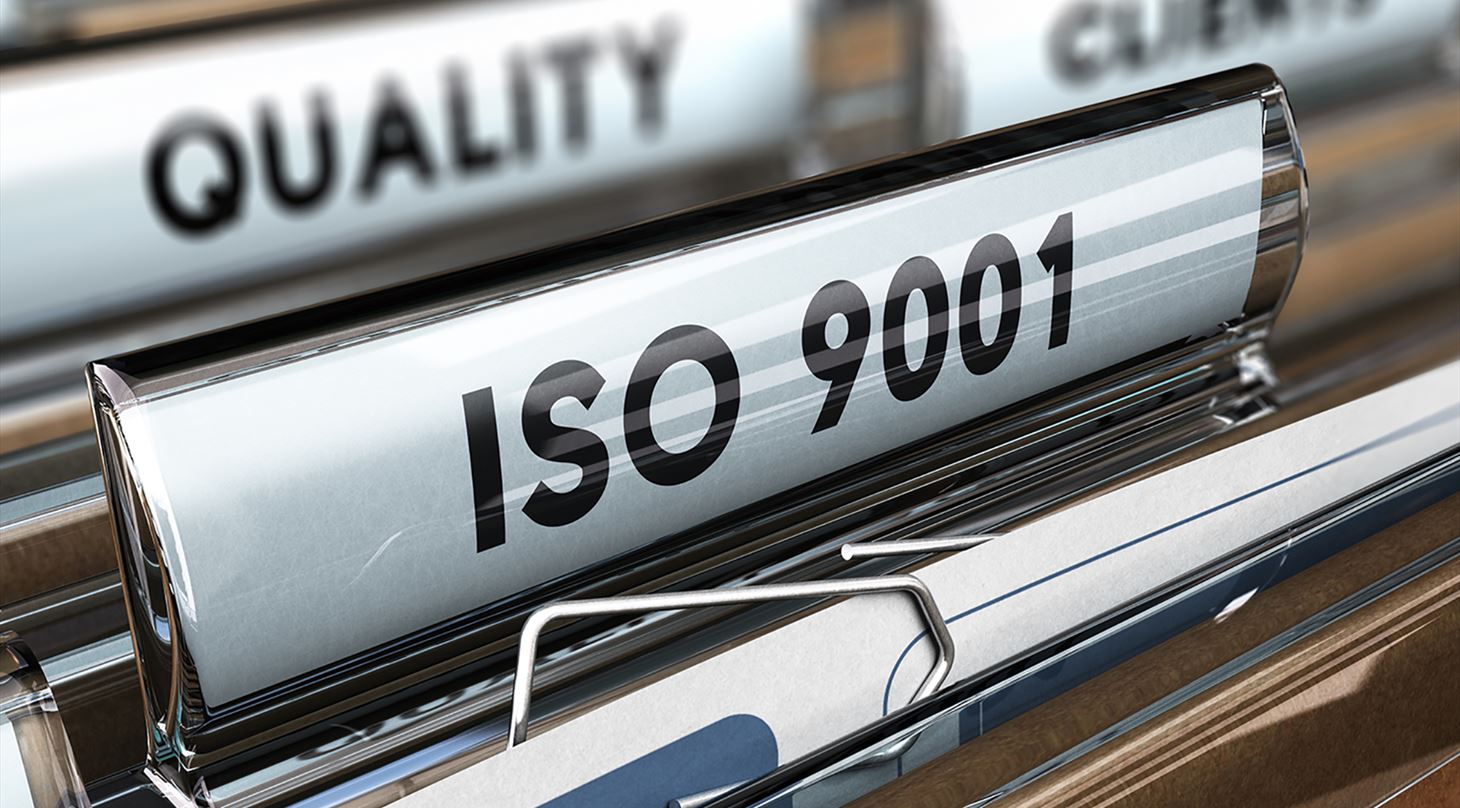
How to improve your maker setup using Quality Management Systems
Learnings from the Danish Technological Institute on implementation of ISO 9001 and ISO 13485 for additive manufacturing in an industrial setup - as part of the Horizon 2020 project Eur3ka.
During the supply chain crisis associated with COVID-19, a broad interest in helping was seen from makers all over the world. These makers had the production equipment - typically a hobby 3D printer - to make a difference and print face shield or face mask holders, which were not possible to source from other places. This has been reported in other Eur3ka deliverables, but how could the maker resource for crisis production be better utilized? Here, inspiration from the industry on utilization of quality management systems is proposed.
A Quality Management System (QMS) is used in most production companies to ensure the quality of products. But what is a quality management system? In any process where quality is managed, from checking an airplane before lift-off to cooking dinner for the family, a system for checking the quality is applied. For cooking dinner, you may check the freshness of the ingredients before applying them to the dish or taste the finished product for validating the taste before serving it. A QMS as understood within the manufacturing industry is typically based on one or more different international standards, depending on the industry segments, e.g., ISO 9001 for general production, ISO 13485 for MedTech production, or A9100 for most aerospace and defense. If you wish to communicate professionalism to the world, you can invite an external notified body to certify your company QMS according to the standards - in some cases, the external certification is mandatory.
These standards are typically found behind a paywall, e.g., at www.iso.org, and they use a specific language or terminology that may be difficult to appreciate the first time you meet them. An example could be in ISO 9001, the mandatory internal audits with the top management, as single person companies operating are forced to document. However, most of the content of the standards is common sense and something you, as a maker, already do to some extent - and it is only the framework and language that is different.
Guides and courses on all aspects of implementing, maintaining, and auditing QMS are easily available, but in the context of maker level additive manufacturing, the area is to our knowledge sparsely covered. Thus, we present this short guide to improving a maker setup for manufacturing by inspiration of standard QMS.
Imagine a situation where you wish to upgrade your personal hobby printer setup at home to supply a specific component needed in a global crisis. The printer itself may be able to manufacture the component, but how do you ensure the quality of the parts you ship off? And how do you achieve trust from the customers (even if you send the parts off for free, they are still customers in QMS terminology)?
Which process steps affect the quality?
Firstly, you must go through your process steps, from file preparation to shipping, and determine if there are any places where you expect errors to occur? How can you catch errors or avoid them? Several tools exist for going through this systematically, e.g. fish bone, risk matrix, and process failure mode analysis.
Is delamination or adhesion between layers in general the main issue which can affect the quality? In that case, you could print torsion or tensile test specimens close to the component. A method utilized for manufacturing at the Danish Technological Institute, is to build a qualification platform with plenty of relevant test specimens, tensile bars, bending tests, and density coupons, to validate that everything performs as expected. Then you lock all processing parameters which can affect the quality (build file, position, slicing parameters, etc.) and only test a part of the test the critical specimens in the following production platforms, see below.
Case study: Continous build control
Figure 1 and 2, Example from the Danish Technological Institute of how quality can be managed for metal 3D-printing.
How do you make sure to learn from your mistakes?
Keep a log on deviations (non-conformities in ISO 9001 terminology) and how they were fixed. This will help you improve your quality and keep track of your process. You could even make it publicly available for improved trust through transparency. An example of how this can be done could be a simple excel sheet as seen below. If the customer has a quality check, as the Danish Makers Against Corona did, where components were twisted to check for mechanical integrity, making sure that information reaches the maker would be essential input to the QMS in order to improve the quality.
Figure 3, Example on how to keep track of processes and improve quality continuously.
Additional info
For additional info on how quality can be managed in an industrial additive manufacturing setting, take a look here